Powder Coating: Everything you need to know
A blank sheet of metal does not look appealing nor is it properly protected against external influences such as corrosion or scratches. Powder coating is a process that enhances surfaces both mechanically and visually, by applying powder and curing it. Many everyday objects such as windows, doors, furniture, and facades are being powder coated today. Additionally, powder coatings can also be used for products such as industrial machines or for certain car parts. New innovations also allow nonmetallic surfaces, such as plastic, wood, ceramics or glass, to be finished with powder coatings.
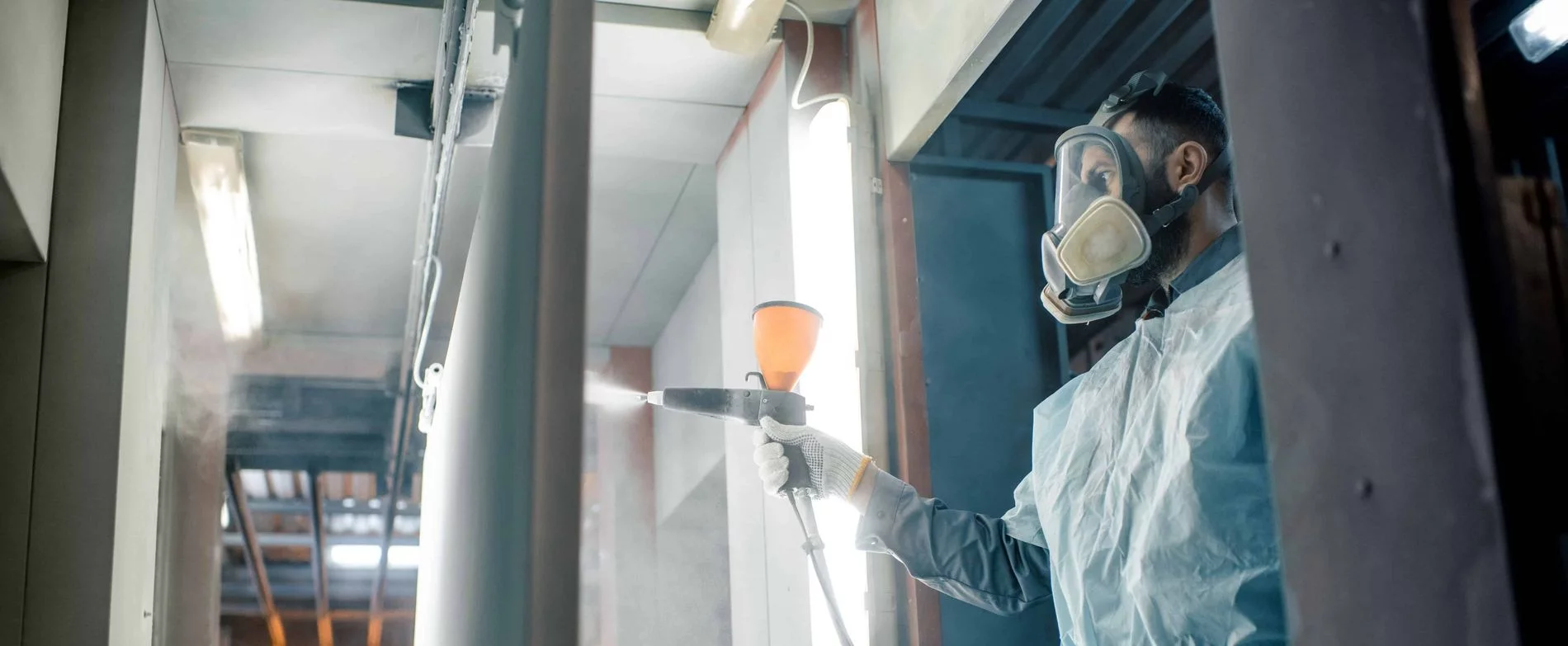
What is Powder Coating?
Powder coating describes the finishing of surfaces with powder coatings, which is done by electrostatically charging surfaces. After this the object is placed in an oven, causing the powder to melt and harden again. This process is applicable to both metallic and nonmetallic surfaces. Generally, the process takes place automatically along a conveyor system.
Advantages of Powder Coating
- No solvents
- Protection and Decoration
- Resistant surface
- Close to 100% material utilization
- Outstanding results in one coat
- High mechanical resistance
- Easy and clean application
- Applicable on various substrates
What are Powder Coatings made of?
Powder coatings are dry mixtures, that generally consist of four main components:
Binders
Think of resin and hardener as the base duo of powder coatings. They are responsible for the coating's foundational structure and performance. Here are some common resin chemistries:
- Polyester: Known for its excellent exterior durability, polyester resin is often used for applications where exposure to the elements is a concern, like outdoor furniture or architectural elements.
- Epoxy: Epoxy resin offers outstanding mechanical properties and corrosion resistance. It's commonly found in industrial and automotive coatings where durability is essential.
- Polyurethane: Polyurethane resin excels in providing a smooth and glossy finish. You'll find it in high-quality automotive coatings and wood finishes.
- Epoxy-Polyester (Hybrid): This is a versatile option that combines the strengths of both epoxy and polyester resins, making it suitable for a wide range of applications.
- Acrylic: Acrylic resin provides excellent color and gloss retention, making it a great choice for decorative and architectural applications.
These resins are important ingredients that provide powder coatings with crucial properties like mechanical strength, chemical resistance, exterior durability, and corrosion resistance.
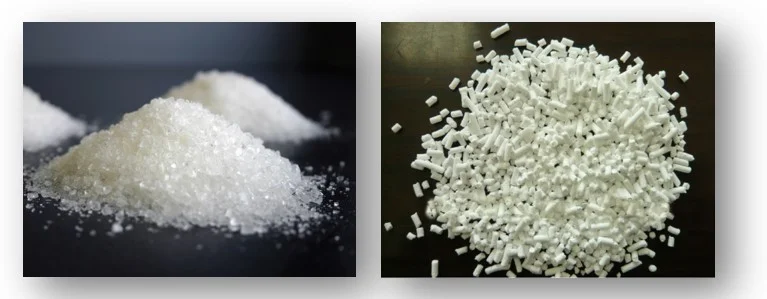
Additives
Additives are, as the name suggests, ingredients that give a powder coating its unique characteristics and performance enhancements. They come in various categories. Some of those are for example:
- Appearance (Flow Control) Additives: These additives prevent issues like cratering or orange peel, ensuring a smooth and even finish.
- Degassing Additives: They help release air from the film while maintaining its open structure.
- Exterior Durability Additives: Including UV absorbers, these additives protect the coating from the harmful effects of sunlight and other environmental factors.
- Corrosion Resistance Additives: For coatings that need extra protection against corrosion, zinc dust additives come to the rescue.
- Charge Control Additives: They enhance the coating's ability to accept an electric charge during application.
- Gloss Control Additives: Achieving the desired level of gloss can involve both chemical and physical methods. This helps control the coating's shine.
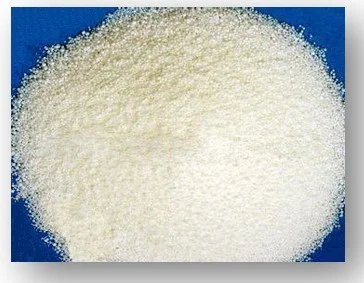
Pigments and Dyes
Pigments bring life and color to the powder coating film. They can be organic or inorganic and play a primary role in defining the coating's aesthetic appeal. Considerations for pigments include their thermal stability at curing temperatures and their resistance to exposure conditions, such as sunlight.
Pigments provide two primary properties:
- Hiding Power: This determines how effectively the coating conceals the substrate's color or imperfections beneath it.
- Appearance: Pigments are key in creating the desired look and finish of the coating, from high gloss to matte.
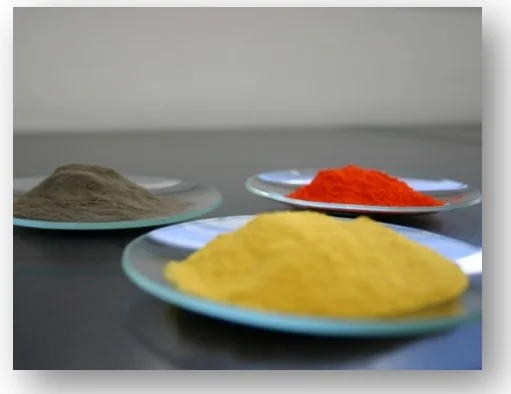
Fillers
These substances give the powder volume and, thanks to their particle size, ensure optimum packing density (ratio between pigments, fillers and binders). Natural minerals such as calcium carbonate are being used as fillers.
How are Powder Coatings manufactured?
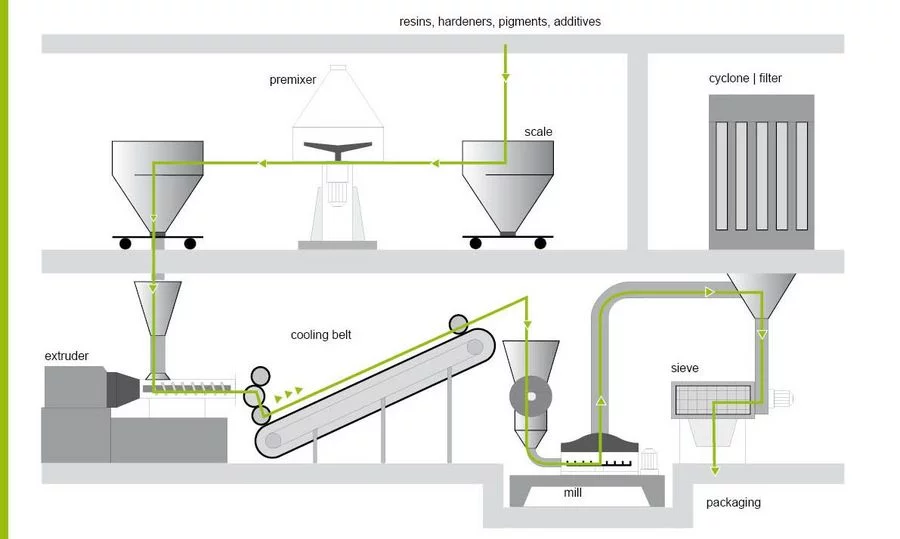
1. Formula: No powder coating is like the other - just like the different requirements for powder coatings. Henceforth, even prior to production, the right recipe is needed. This can be specially adapted according to customers and usage.
2. Weighing: In the following step, the ingredients are weighed out correctly into a container. Differences in density and grain size do not play a role for the time being.
3. Mixing: The weighed raw materials are then mixed both horizontally and vertically using a special machine. The speed of the mixing tool and the mixing time are precisely defined.
4. Extrusion: The mixture is now melted in the extruder. The aim of the extrusion is to create a homogeneous mass - this is achieved with heat and the shearing forces generated in the machine.
5. Cooling: After the mass exits the extruder, it is cooled on a cooling belt and rolled out. The solid mass is then broken up into small chips by a shredder.
6. Grinding: In the first step, the now hardened, cooled extrudate is broken into rough chips (10 to 20 mm) and then ground into powder coating in the fine grinding step.
7. Sieving: Before the powder leaves the mill, coarse particles and fine parts are filtered out of the mixture using sieves and suction.
8. Filling: The finished powder coating is then filled by weight and packaged in airtight containers.
Possible Applications for Powder Coatings
Due to their diverse properties, powder coatings are being used in a wide variety of industries and different markets. The main customers come from the following areas:
How does Powder Coating work?
There are many step-by-step instructions for powder coating - the powder coating process can be split into three main tasks:
1. Pre-treatment: The substrate is freed from dust, scale, rust, grease, dirt and any oxide layers (for example on aluminum). There exist chemical and mechanical pre-treatment processes. In order to increase the corrosion protection and improve the adhesion of the powder coating a conversion layer is created on the piece during the pre-treatment. Following this the workpiece must dry completely.
2. Application of the Powder Coating: By using a powder spray gun, the powder coating is applied to the grounded surface. It is essential to avoid the entry of dust and dirt at this step. The powder spray gun creates a charged cloud of powder. As a result, the paint particles adhere electrostatically to the piece and form a layer.
3. Curing: The powder coating is then cured in an oven at temperatures between 110 and 250 °C. Various factors such as heating time and substrate thickness affect the final curing time.
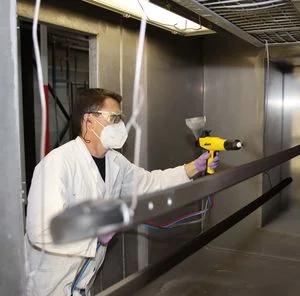
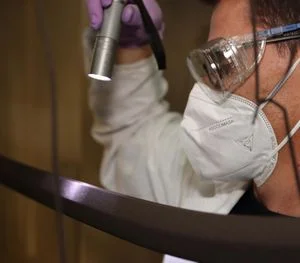
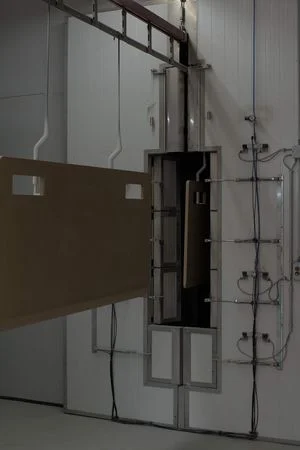
Typical Powder Coating Mistakes
Mistakes happen – also with powder coating. High-quality powders provide a good basis for optimal coating results. In order to ensure that the following steps won’t cause any types of mistakes, it is important for a coater to be aware of potential errors and to minimize risks. In our TIGER Troubleshooting Guide and our Youtube Playlist we have summarized the most common errors - including ways to fix them!
An overlook of the most common powder coating errors:
During application
- Poor fluidization
- Powder drizzles off the work piece
- Fluctuations in layer thickness
Surface defects
- Powder puffs on the workpiece
- Craters
- Pin holes
- Picture framing effect
- Dripping
- Orange peel effect
Optical & Technical defects
- Color deviations
- Gloss level deviations
- Poor mechanical properties
- Loss of chemical resistance
Colors and Effects
Powder coatings are available in all possible colors, different surface structures and gloss levels. Manufacturers often base selections on the RAL color system. In addition, unique effects can be achieved by adding special pigments. Popular effects include Metallics, Flip-Flop and Dormant powders.
Special Powder Coatings
Advanced development enables production of special powder coatings for specific requirements. These are for example:
Differences to Wet Paint
Due to the differences between wet paint and powder coatings, there are applications, where one is more suitable than the other.
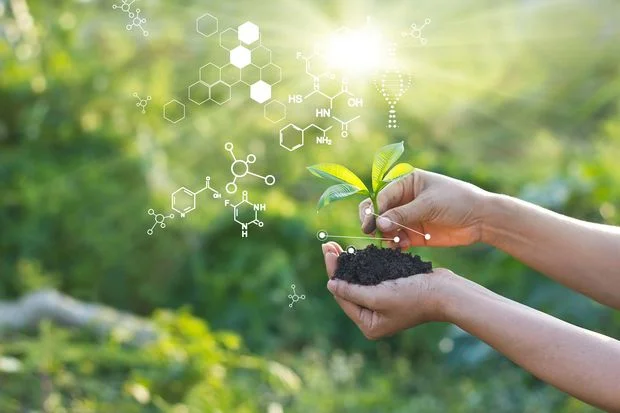
Powder Coating and the Environment
Powder coatings do not contain toxic heavy metals, are free of solvents and therefore do not release VOCs (volatile organic compounds) during coating or curing. This is also reflected in the CO2 footprint, where powder coatings have the lowest values of all available coating solutions.
This means that, unlike solvent-based wet coatings, powder coatings are inherently environmentally friendly and offer the highest quality as well as outstanding performance.
With the Green Deal in mind, TIGER is doing everything it can with its Green TIGER initiative to further increase the environmental performance of TIGER's powder coating products and drive the energy revolution.