Wprowadzenie do malowania proszkowego
Zanim przejdziemy do szczegółów procesu nakładania farby proszkowej, poświęćmy chwilę na omówienie koncepcji malowania proszkowego jako całości. Malowanie proszkowe wyróżnia się jako jedno z najnowszych osiągnięć w popularnych obecnie technikach wykańczania powierzchni. Pojawiła się jako nowatorska metoda wykańczania w latach sześćdziesiątych XX wieku, a jej przyjazne dla środowiska zalety sprawiają, że jest to wiodący wybór wśród systemów powłokowych ze względu na swój bezrozpuszczalnikowy skład. Technologia ta pozwala osiągnąć grubość powłoki około 2-4 milicali przy pojedynczej warstwie, wykazując wyjątkową wydajność w zużyciu materiału.
Co więcej, malowanie proszkowe zapewnia solidne właściwości mechaniczne i wyjątkową ochronę krawędzi, zapewniając, że gotowy produkt zachowa swoją integralność i wygląd. Warto zauważyć, że ta metoda wykończenia konsekwentnie zapewnia optymalne wyniki przy zaledwie jednej aplikacji. Ponadto minimalizuje ilość odpadów dzięki niezwykłemu współczynnikowi odzysku nadmiaru natrysku, który może sięgać nawet 95%. Podsumowując, malowanie proszkowe okazuje się być opłacalnym wyborem, korzystnym zarówno dla środowiska, jak i budżetu poprzez zmniejszenie wydatków na materiały i aplikację.
Różne rodzaje podłoży do malowania proszkowego
Wybór podłoża odgrywa kluczową rolę w określaniu ostatecznego wykończenia, trwałości i przydatności do szerokiego zakresu zastosowań. Poniżej omówimy niektóre z najpopularniejszych podłoży do malowania proszkowego i zagłębimy się w ich unikalne właściwości i zastosowania.
1. Stal: Konstrukcje stalowe są jednym z najpopularniejszych podłoży do malowania proszkowego. Jest trwała, mocna i wszechstronna, co czyni ją doskonałym wyborem dla różnych gałęzi przemysłu. Stal malowana proszkowo jest powszechnie spotykana w częściach samochodowych, urządzeniach, meblach zewnętrznych i sprzęcie przemysłowym. Jej odporność na trudne warunki środowiskowe, takie jak ekspozycja na promienie UV i wilgoć, czyni ją niezawodną opcją.
2. Aluminium: Aluminium jest kolejnym bardzo popularnym podłożem do malowania proszkowego. Charakteryzuje się lekkością i doskonałą odpornością na korozję, dlatego jest idealnym wyborem dla elementów architektonicznych, konstrukcji zewnętrznych i komponentów lotniczych. Gładka powierzchnia aluminium pozwala na uzyskanie nieskazitelnego wykończenia powłoki proszkowej, zwiększając jej estetykę.
3. Drewno (MDF): Podłoża drewniane, w szczególności płyty pilśniowe o średniej gęstości (MDF), zyskały w ostatnich latach popularność w zastosowaniach związanych z malowaniem proszkowym. Malowane proszkowo powierzchnie drewniane są stosowane w meblach, szafkach i wystroju wnętrz, oferując szeroką paletę kolorów i trwałe wykończenie.
4. Tworzywa sztuczne: Malowanie proszkowe na podłożach z tworzyw sztucznych to kolejne innowacyjne podejście. Zwiększa trwałość i odporność na zarysowania materiałów z tworzyw sztucznych, zapewniając jednocześnie atrakcyjne wizualnie wykończenie. Podłoża z tworzyw sztucznych, takie jak polietylen i polipropylen, są wykorzystywane w częściach samochodowych, sprzęcie zewnętrznym i towarach konsumpcyjnych.
5. Pultruzja (materiał kompozytowy): Pultruzja to materiał kompozytowy wykonany z włókien i żywic. To mocne i lekkie podłoże jest wysoce odporne na korozję, dzięki czemu nadaje się do wymagających środowisk. Malowanie proszkowe materiałów pultruzyjnych jest często spotykane w konstrukcjach takich jak mosty, poręcze i platformy morskie, gdzie trwałość i długowieczność są najważniejsze.
Zasadniczo, malowanie proszkowe zapewnia wszechstronne i trwałe wykończenie dla różnorodnych podłoży. Wybór podłoża zależy od zamierzonego zastosowania i wymaganych konkretnych jego właściwości - wytrzymałości stali i aluminium, estetycznych możliwości drewna i tworzyw sztucznych oraz specjalistycznych atrybutów materiałów pultruzyjnych. Niezależnie od tego, czy chodzi o cele funkcjonalne, czy dekoracyjne, malowanie proszkowe oferuje rozwiązanie poprawiające wydajność i wygląd niezliczonych produktów i konstrukcji.
Zrozumienie etapów procesu malowania proszkowego
Malowanie proszkowe to proces wykańczania na sucho, który polega na nakładaniu drobnych, naładowanych elektrostatycznie cząstek proszku na powierzchnię podłoża. Ta metoda aplikacji zapewnia równomierną i spójną powłokę, wolną od kropelek, zacieków lub nierówności.
1. Przygotowanie powierzchni i obróbka wstępna
Przed nałożeniem proszku podłoże musi zostać dokładnie oczyszczone, aby usunąć wszelkie zanieczyszczenia, takie jak olej, smar lub rdza. Ten kluczowy krok zapewnia właściwą przyczepność i nieskazitelne wykończenie. Podłoże jest wolne od kurzu, zgorzeliny, rdzy, tłuszczu, brudu i wszelkich warstw tlenku (na przykład na aluminium). Istnieją chemiczne i mechaniczne procesy obróbki wstępnej. Aby zwiększyć ochronę antykorozyjną i poprawić przyczepność powłoki proszkowej, podczas obróbki wstępnej na elemencie tworzona jest warstwa konwersyjna. Następnie element musi całkowicie wyschnąć.
Metody czyszczenia: Proces czyszczenia obejmuje użycie słabych zasad i neutralnych detergentów, często w zbiornikach zanurzeniowych lub stacjach mycia. Stacje te są wyposażone w urządzenia do natryskiwania części gorącą wodą, parą, detergentami i innymi roztworami do obróbki wstępnej w celu oczyszczenia i chemicznego przygotowania powierzchni przed powlekaniem. Zapewniają one nieskazitelne podłoże dla powłoki proszkowej.
Metody maskowania dla precyzyjnych aplikacji: Czasami części wymagają pozostawienia określonych obszarów bez powłoki. W tym miejscu do gry wkraczają produkty maskujące, takie jak kropki maskujące. Są one dostępne w różnych kształtach i formach, zazwyczaj wykonane z papieru lub folii z tworzywa sztucznego pokrytej klejem wrażliwym na nacisk. Te sprytne narzędzia przylegają do podłoża, chroniąc pokryte obszary przed kontaktem z materiałem proszkowym podczas procesu powlekania.
Rola chemicznej obróbki wstępnej: Wstępna obróbka chemiczna polega na użyciu chemikaliów do czyszczenia powierzchni, co sprzyja przyleganiu powłoki proszkowej do śliskich lub trudnych metali. Proces ten jest zwykle przeprowadzany przy użyciu serii dysz natryskowych lub alkalicznego zanurzania. Części poddawane są wielu etapom w celu zapewnienia optymalnego przygotowania powierzchni. Procesy wstępnej obróbki chemicznej mogą być zautomatyzowane, składające się z linii przenośników z wieloma etapami lub obsługiwane ręcznie przy użyciu części natryskowych z różdżkami lub wężami.
Najpierw podłoża są czyszczone przy użyciu alkalicznego, kwaśnego lub neutralnego środka czyszczącego (zazwyczaj alkalicznego). Następnie części są poddawane obróbce powierzchniowej za pomocą powłoki konwersyjnej, po czym kwas wytrawia powierzchnię, aby przygotować ją do kolejnych operacji. Konkretny rodzaj powłoki konwersyjnej może się różnić w zależności od powlekanego materiału i pożądanych właściwości produktu końcowego. Etap płukania jest zwykle uwzględniany między każdym etapem obróbki wstępnej w celu usunięcia wszelkich pozostałości chemikaliów i zanieczyszczeń. Na koniec stosuje się płukanie RO (odwrócona osmoza) lub DI (dejonizacja), aby poprawić wydajność powłoki i zmniejszyć zużycie chemikaliów do obróbki wstępnej. Należy jednak pamiętać, że płukanie to nie powinno zawierać żadnych chlorków ani fluorków, aby zapobiec dalszemu zanieczyszczeniu chemicznemu.
Mechaniczna obróbka wstępna dla trudnych zanieczyszczeń: Mechaniczna obróbka wstępna polega na użyciu środków ściernych, co zasadniczo oznacza pocieranie lub szlifowanie w celu wypolerowania lub oczyszczenia podłoża. W przypadku niektórych zastosowań, w których konieczne jest usunięcie zanieczyszczeń nieorganicznych, takich jak rdza, zgorzelina walcownicza i tlenek laserowy, preferowana jest ta metoda obróbki wstępnej. Techniki takie jak piaskowanie lub śrutowanie wykorzystują powietrze o dużej prędkości do napędzania materiałów ściernych (takich jak piasek, żwir lub śrut stalowy) w kierunku podłoża.
Tworzy to wzór kotwicy na powierzchni części, znacznie poprawiając przyczepność powłoki proszkowej do podłoża. Dostępnych jest kilka różnych rodzajów materiałów ściernych, a ich zastosowanie zależy od rodzaju wykończenia i zanieczyszczenia, które ma zostać usunięte. Na przykład, łupiny orzecha włoskiego będą używane do usuwania zadziorów, podczas gdy plastikowy piasek będzie używany do usuwania farby. Podobnie, szklane kulki są preferowane, jeśli celem końcowym jest uzyskanie matowego i satynowego wykończenia. Czyszczenie mechaniczne może być stosowane niezależnie lub wraz z obróbką chemiczną. Poprawia ono przyczepność, ale nie zapewnia dodatkowej ochrony przed korozją. W wielu przypadkach, po mechanicznym czyszczeniu strumieniowo-ściernym, powierzchnia jest pokrywana odpowiednim podkładem w celu zapewnienia dodatkowej ochrony antykorozyjnej. Podkład może również zawierać materiały zawierające cynk w celu dalszego wzmocnienia.
Najlepsze praktyki lub rzeczy, o których należy pamiętać podczas przygotowania powierzchni i obróbki wstępnej.
- Czyszczenie i odtłuszczanie: Zacznij od czystej powierzchni wolnej od wszelkich zanieczyszczeń, takich jak olej, smar, brud lub rdza. Użyj odpowiednich metod czyszczenia, takich jak czyszczenie alkaliczne, czyszczenie rozpuszczalnikiem lub czyszczenie mechaniczne, w zależności od stanu podłoża i rodzaju obecnych zanieczyszczeń.
- Ścieranie: W niektórych przypadkach, zwłaszcza w przypadku metali, konieczne może być zastosowanie metod ściernych, takich jak piaskowanie, szlifowanie lub trawienie chemiczne w celu uzyskania chropowatej powierzchni. Zwiększa to przyczepność powłoki proszkowej.
- Powłoka konwersyjna: Aby zwiększyć odporność na korozję, należy rozważyć zastosowanie powłoki konwersyjnej, takiej jak fosforan żelaza lub fosforan cynku. Proces ten chemicznie zmienia powierzchnię, aby poprawić przyczepność farby proszkowej.
- Płukanie: Po etapach czyszczenia i obróbki wstępnej należy wykonać dokładne płukanie w celu usunięcia wszelkich pozostałości chemikaliów lub zanieczyszczeń. Pozostawione zanieczyszczenia mogą wpływać na przyczepność i wydajność farby proszkowej.
- Suszenie: Prawidłowo wysuszyć podłoże, aby zapobiec powstawaniu plam wodnych lub defektów powierzchni farby proszkowej. W zależności od podłoża i możliwości zakładu można zastosować suszenie powietrzem, suszenie w piecu lub suszenie z wymuszonym obiegiem powietrza.
- Wybór metody obróbki wstępnej: Należy wybrać metodę obróbki wstępnej, która najlepiej pasuje do podłoża i specyficznych wymagań powłoki. Na przykład, fosforan cynku jest skuteczny w przypadku podłoży stalowych, podczas gdy chromianowa powłoka konwersyjna jest często stosowana w przypadku aluminium.
- Pomiar pH: Poziomy pH mają wpływ na reakcje chemiczne, przyczepność, odporność na korozję i opłacalność. Utrzymanie właściwego pH jest więc niezbędne.
- Temperatura, przewodność wody i ciśnienie dyszy natryskowej: Czynniki te zapewniają spójność, wydajność i jakość w procesie obróbki. Upewnij się więc, że odpowiednio je kontrolujesz, aby uzyskać optymalne wyniki.
Jak zmienia się proces obróbki wstępnej w zależności od wyboru podłoża?
Rodzaj używanego podłoża może mieć duży wpływ na proces obróbki wstępnej.
- Stal: Podłoża stalowe są zazwyczaj poddawane obróbce wstępnej fosforanem żelaza lub fosforanem cynku w celu zwiększenia przyczepności i zapewnienia odporności na korozję.
- Aluminium: Podłoża aluminiowe wymagają innego podejścia. Powłoka konwersji chromianowej jest często stosowana w celu poprawy przyczepności i odporności na korozję, szczególnie w zastosowaniach architektonicznych lub zewnętrznych.
- Drewno: W przypadku podłoży drewnianych nacisk kładzie się na czyszczenie powierzchni i upewnienie się, że w drewnie nie ma wilgoci, która może wpływać na przyczepność.
2. Faza aplikacji proszku - Jak nakładane są farby proszkowe?
W zależności od potrzeb projektu i wielkości firmy, istnieje wiele różnych opcji aplikacji proszku do wyboru. Ogólnie rzecz biorąc, istnieją dwie podstawowe metody stosowane w całej branży: Osadzanie elektrostatyczne (ESD) i malowanie proszkowe ze złożem fluidalnym.
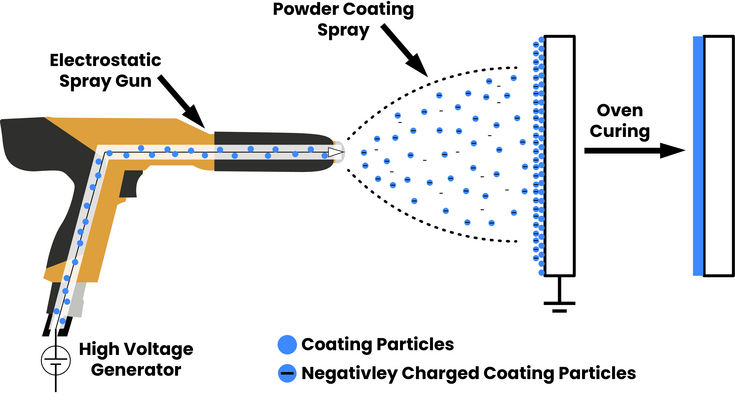
Osadzanie elektrostatyczne (ESD)
ESD jest bardziej powszechną z dwóch metod, szczególnie w przypadku powlekania części metalowych. Proszek jest nakładany za pomocą pistoletu natryskowego, tworząc ładunek elektrostatyczny, który przyciąga cząsteczki do uziemionego podłoża. To przyciąganie skutkuje jednolitą i wydajną powłoką. Na tym etapie należy unikać przedostawania się kurzu i brudu. Pistolet do malowania proszkowego tworzy naładowaną chmurę proszku. W rezultacie cząsteczki farby przylegają elektrostatycznie do elementu i tworzą warstwę.
Typowa ręczna konfiguracja tego procesu aplikacji obejmuje następujące elementy:
- Kabina do napylania proszków: Służy jako obszar roboczy do nakładania materiału proszkowego na element. Działa również jako filtr powietrza oraz system zatrzymywania i odzyskiwania nadmiaru natrysku.
- Podajnik proszku: Ta jednostka rozprowadza materiał proszkowy do pistoletu natryskowego.
- Elektrostatyczny pistolet natryskowy: Pistolet przekazuje ładunek elektryczny na proszek i nakłada go na podłoże. Istnieją dwa popularne typy pistoletów elektrostatycznych: Corona i Tribo.
- Pistolety z ładowaniem Corona: Są one najczęściej używane i wytwarzają pole elektrostatyczne o wysokim napięciu i niskim natężeniu między elektrodą a powlekanym produktem. Cząsteczki proszku przechodzą przez zjonizowane pole elektrostatyczne, zostają naładowane i osadzają się na elektrycznie uziemionej powierzchni części.
- Pistolety natryskowe Tribo: W tym typie pistoletu cząsteczki proszku uzyskują ładunek elektrostatyczny poprzez tarcie, gdy ocierają się o stały izolator lub przewodnik wewnątrz pistoletu. Proces ten powoduje, że dodatnio naładowane cząsteczki proszku eliminują efekt klatki Faradaya - powszechny problem z pistoletami Corona, dzięki czemu idealnie nadają się do powlekania złożonych kształtów. Jest wszechstronny - działa z proszkami epoksydowymi, akrylowymi, nylonowymi, teflonowymi i poliestrowymi, zapewniając płynną i precyzyjną aplikację. Ponadto idealnie nadaje się do ponownego powlekania uszkodzonych części.
- Pistolety z ładowaniem Corona: Są one najczęściej używane i wytwarzają pole elektrostatyczne o wysokim napięciu i niskim natężeniu między elektrodą a powlekanym produktem. Cząsteczki proszku przechodzą przez zjonizowane pole elektrostatyczne, zostają naładowane i osadzają się na elektrycznie uziemionej powierzchni części.
- Systemy odzysku i odzyskiwania: Zbierają nadmiar materiału do ponownego wykorzystania w przyszłych aplikacjach powlekania.
Systemy natryskowe odgrywają kluczową rolę w procesie aplikacji proszków, oferując wydajne i precyzyjne nakładanie powłok na różne powierzchnie i geometrie części. Systemy natryskowe w malowaniu proszkowym obejmują takie elementy, jak zbiornik na proszek do przechowywania materiałów powłokowych, pistolet aplikacyjny do natryskiwania, system podawania do transportu proszku ze zbiornika do pistoletu, jednostkę sterującą, która reguluje i dostraja różne parametry aplikacji, a także systemy dostarczania i odzyskiwania powietrza. Co zatem składa się na dobry system napylania farb proszkowych? Dowiedzmy się!
Godną uwagi cechą skutecznych systemów natryskowych jest ich konstrukcja umożliwiająca serwisowanie w terenie i wykorzystanie komponentów szybkoobrotowych. To strategiczne podejście upraszcza procedury konserwacyjne, prowadząc do skrócenia czasu przestojów i zapewniając ciągłą, niezawodną wydajność podczas różnych zadań powlekania. Rozważając systemy natryskowe, należy również skupić się na możliwościach adaptacji i wybrać te o wszechstronnych konfiguracjach, ponieważ oferują one elastyczność w celu spełnienia różnorodnych wymagań dotyczących powlekania. Innowacyjna konstrukcja pompy jest kolejnym ważnym czynnikiem, ponieważ dodatkowo zwiększa funkcjonalność całego systemu poprzez optymalizację zużycia energii, przyczyniając się zarówno do wydajności, jak i zrównoważonego rozwoju procesów powlekania.
Wreszcie, w pełni cyfrowe jednostki sterujące stają się coraz bardziej powszechne, zapewniając precyzyjną kontrolę nad ustawieniami elektrostatycznymi i pneumatycznymi. Ten poziom kontroli ma kluczowe znaczenie dla osiągnięcia optymalnej wydajności powlekania, ostatecznie prowadząc do produkcji wysokiej jakości gotowych produktów.
Malowanie proszkowe w złożu fluidalnym
W przeciwieństwie do tego, malowanie proszkowe w złożu fluidalnym jest nieco inne. Oto jak to działa:
- Podgrzewanie: Części są wstępnie podgrzewane, aby zapewnić skuteczne przyleganie proszku. Musi on osiągnąć temperaturę co najmniej 350°F, a najlepiej od 400 do 450°F. Ta podwyższona temperatura jest niezbędna do utrzymania części w temperaturze wyższej niż temperatura topnienia proszku. Zazwyczaj do tego podgrzewania stosuje się konwencjonalny piec konwekcyjny opalany gazem.
- Powlekanie zanurzeniowe: Kolejnym krokiem jest powlekanie zanurzeniowe podgrzanej części. Pompa powietrza ułatwia przepływ powietrza przez fluidyzator do powlekania proszkowego, tworząc płynną zawiesinę cząstek proszku. Gorąca część jest następnie zanurzana w tym fluidyzowanym złożu farby proszkowej i przemieszczana w celu zapewnienia ciągłej powłoki.
- Zanurzanie: Część pozostaje zanurzona w złożu fluidalnym, aby umożliwić farbie proszkowej utworzenie grubej, odpornej na zużycie powłoki. Ostateczna grubość powłoki zależy od początkowej temperatury przedmiotu przed zanurzeniem i czasu spędzonego w złożu fluidalnym farby proszkowej.
- Post-fusing: Ostatnią fazą malowania proszkowego w złożu fluidalnym jest proces utrwalania końcowego. Po tym, jak nadmiar proszku ścieknie z produktu, jest on przenoszony do pieca ustawionego na niższą temperaturę w celu utwardzenia. Co ważne, temperatura po wygrzewaniu musi być niższa niż temperatura początkowego wygrzewania w piecu. Ten krok zapewnia, że cały proszek przylega do części podczas zanurzania i topi się, tworząc gładką, jednolitą powłokę. Użycie zbyt wysokiej temperatury w piecu może prowadzić do niepożądanych rezultatów, takich jak topnienie powłoki, zwiotczenie lub kapanie.
Zautomatyzowana optymalizacja aplikacji malowania proszkowego
Wykorzystanie oscylatorów, przeciwsobników i robotów do zarządzania sprzętem natryskowym zapewnia oszczędność kosztów i spójne pokrycie w wielu zastosowaniach. Wyzwalanie pistoletu, które obejmuje automatyczne włączanie i wyłączanie pistoletu natryskowego w oparciu o pozycjonowanie części, zmniejsza nadmierne rozpylanie, prowadząc do zmniejszenia zużycia materiału.
Znaczenie uziemienia i najlepsze praktyki podczas nakładania powłok proszkowych
Uziemienie jest prawdopodobnie najważniejszym aspektem udanej aplikacji farby proszkowej. Mówimy "prawdopodobnie", ponieważ jest to subiektywne stwierdzenie i dla niektórych inne czynniki mogą być ważniejsze, niezależnie od tego, czy jest to system natryskowy, czy sam proszek.
Z punktu widzenia bezpieczeństwa, nieuziemione części mogą gromadzić ładunek, stwarzając ryzyko wyładowania elektrycznego, gdy się do nich zbliżymy. Takie wyładowanie może być nie tylko zaskakujące, ale także niebezpieczne. Wyładowania na niewielkich odległościach między naładowanymi powierzchniami a uziemieniem mogą zawierać energię wystarczającą do zapłonu proszku rozpylanego z pistoletu, co dodatkowo podkreśla aspekt bezpieczeństwa.
Na poziomie jakości, utrzymanie solidnego podłoża jest kluczowe dla osiągnięcia stałej grubości powłoki i jednorodności aplikacji proszku. Problemy takie jak penetracja klatki Faradaya i jonizacja wsteczna mogą pojawić się bez odpowiedniego uziemienia. Badanie przeprowadzone przez Kolene Corporation wykazało, że utrzymanie doskonałego uziemienia podczas procesu aplikacji proszku znacznie poprawiło topografię powlekanej proszkowo powierzchni.
Wreszcie, z perspektywy kosztów, słabe uziemienie negatywnie wpływa na wydajność transferu i minimalną grubość powłoki. Nieefektywne uziemienie może skutkować nadmiernym zużyciem proszku w celu osiągnięcia pożądanej grubości powłoki, co prowadzi do zwiększenia ilości odpadów i kosztów.
Aby zapewnić skuteczne uziemienie, konieczne jest posiadanie identyfikowalnej ścieżki od części do pręta uziemiającego farby proszkowej, bez załamania przewodności elektrycznej. Zastosowanie pręta uziemiającego o długości od 8 do 10 stóp, najlepiej dłuższego w warunkach gleby o wysokiej rezystywności, oraz pomiar rezystancji między prętami uziemiającymi może pomóc w zapewnieniu niezawodnego uziemienia. Zastosowanie solidnych miedzianych prętów uziemiających o odpowiedniej długości dodatkowo zwiększa skuteczność systemu uziemienia. Ogólnie rzecz biorąc, prawidłowe uziemienie jest krytycznym czynnikiem w osiąganiu zarówno bezpieczeństwa, jak i wydajności w zastosowaniach związanych z malowaniem proszkowym.
3. Utwardzanie
Po nałożeniu, powlekane podłoże jest poddawane utwardzaniu w wysokiej temperaturze w piecu. Podczas tego procesu cząsteczki proszku topią się i łączą, tworząc solidne i trwałe wykończenie. Powłoka proszkowa jest utwardzana w piecu w temperaturze od 110 do 250 °C. Na ostateczny czas utwardzania wpływają różne czynniki, takie jak czas nagrzewania i grubość podłoża. Termoutwardzalne powłoki proszkowe wymagają określonej energii cieplnej i czasu, aby wywołać reakcję chemiczną potrzebną do usieciowania w film. Po wystawieniu na działanie ciepła materiał proszkowy topi się, tworzy gładką powłokę i zaczyna sieciować, ostatecznie osiągając pełne utwardzenie. W celu zapewnienia niezbędnej energii do utwardzania można zastosować różne metody.
Różne rodzaje pieców do utwardzania oraz znaczenie i ograniczenia każdego z nich
Piece konwekcyjne: Piece konwekcyjne wykorzystują źródło ciepła (zazwyczaj gaz ziemny) i wentylator do cyrkulacji ogrzanego powietrza przez kanał pieca. Gorące powietrze przenosi ciepło na część i powłokę. Jest to najpopularniejszy typ pieca do utwardzania proszków. Gdy część osiąga pożądaną temperaturę, przewodzi ciepło do powłoki, prowadząc do utwardzenia proszku.
Piece na podczerwień (IR): Piece na podczerwień wykorzystują gaz lub energię elektryczną jako źródło energii do emitowania promieniowania w paśmie długości fal IR. Promieniowanie to jest pochłaniane przez proszek i podłoże bezpośrednio pod proszkiem bez znacznego nagrzewania całej części. Takie podejście umożliwia szybszy wzrost temperatury, powodując, że proszek płynie i utwardza się, gdy jest wystawiony na działanie przez wystarczający czas. Jednak na jednorodność utwardzania może mieć wpływ kształt i gęstość części.
Technologie utwardzania promieniowaniem: Obejmują one procesy w bliskiej podczerwieni, ultrafiolecie (UV) i wiązce elektronów (EB). Technologie te oferują potencjalne zastosowania do malowania proszkowego na podłożach wrażliwych na ciepło, takich jak drewno, części z tworzyw sztucznych i zmontowane elementy o delikatnych cechach.
- Utwardzanie promieniami UV: Stosowane są specjalne proszki, które mogą utwardzać się pod wpływem światła ultrafioletowego. Proszki te są początkowo podgrzewane, zwykle za pomocą podczerwieni lub metod konwekcyjnych, do stanu stopionego. Lampy UV dostarczają następnie energię do zestalenia powłoki w ciągu kilku sekund.
- Utwardzanie w bliskiej podczerwieni: Metoda ta obejmuje specjalnie opracowane proszki, wysokoenergetyczne źródła światła i precyzyjne systemy reflektorów, aby zakończyć proces powlekania proszkowego i utwardzania w ciągu kilku sekund. Jest to szczególnie przydatne w przypadku wrażliwych na ciepło zmontowanych części.
Wskazówki dotyczące ulepszania linii do malowania proszkowego
Ogólnie rzecz biorąc, linie operacyjne do malowania proszkowego są mierzone na podstawie ich wydajności, braków/wad i generowanych odpadów. Idealnym rozwiązaniem byłaby szybka linia operacyjna z minimalną ilością przeróbek i odpadów materiałowych. Mając to na uwadze, oto kilka wskazówek, które pomogą Ci to osiągnąć i jak najlepiej wykorzystać proces malowania proszkowego.
- Konserwacja sprzętu: Regularnie konserwuj i czyść cały sprzęt, w tym pistolety natryskowe, filtry kabinowe i piece do utwardzania. Właściwa konserwacja zapewnia stałą wydajność i wydłuża żywotność maszyn.
- Zarządzanie proszkiem: Zoptymalizuj przechowywanie i obsługę proszku, aby zapobiec zanieczyszczeniu i marnotrawstwu. Zainwestuj w wydajne systemy dostarczania proszku i pojemniki do przechowywania.
- Proces obróbki wstępnej: Zapewnij dokładne czyszczenie i przygotowanie powierzchni przed malowaniem proszkowym. Właściwa obróbka wstępna zwiększa przyczepność i zapobiega defektom.
- Kontrola jakości: Wdrożenie solidnego procesu kontroli jakości, w tym inspekcji, testowania i monitorowania. Wczesne wykrywanie i rozwiązywanie problemów zapobiega kosztownym przeróbkom.
- Wybór proszku: Wybierz odpowiedni materiał do malowania proszkowego dla konkretnego zastosowania. Weź pod uwagę takie czynniki jak kolor, wykończenie, efekty, trwałość i kompatybilność z podłożem.
- Optymalizacja utwardzania: Dostosuj ustawienia pieca do utwardzania, aby uzyskać pożądane wykończenie i wydajność. Monitoruj temperaturę i czas, aby zapewnić prawidłowe utwardzanie.
- Szkolenie i certyfikacja: Upewnij się, że Twój zespół jest dobrze wyszkolony i certyfikowany w zakresie technik malowania proszkowego. Ciągła edukacja poprawia poziom umiejętności i spójność.
- Zarządzanie odpadami: Wdrożenie skutecznych praktyk zarządzania odpadami w celu odzyskiwania nadmiaru natrysku i recyklingu nadmiaru/resztek proszku.
- Personalizacja: Dostosowanie linii malowania proszkowego do konkretnych potrzeb produktów i klientów. Nie każda firma jest taka sama, dlatego niestandardowa konfiguracja będzie dla Ciebie najlepszym rozwiązaniem, aby poprawić wydajność i jakość operacyjną.
- Bezpieczeństwo przede wszystkim: Nadaj priorytet bezpieczeństwu swojego zespołu, zapewniając niezbędny sprzęt ochronny i szkolenia. Bezpieczne środowisko pracy przyczynia się do ogólnej produktywności.
Niektóre z najpopularniejszych powłok proszkowych TIGER
TIGER Superdurables
Nasze supertrwałe powłoki proszkowe są specjalnie opracowane i rygorystycznie testowane, aby przetrwać okresy znacznie dłuższe niż 10 lat. Ich wyjątkowa odporność na korozję, promieniowanie UV i warunki atmosferyczne sprawia, że są idealnym wyborem do zastosowań zewnętrznych, takich jak architektura i przemysł meblarski!
Wybierz TIGER dla najwyższej jakości kolorów i wykończeń farb proszkowych
Na zakończenie naszej podróży przez podstawy procesu aplikacji powłok proszkowych staje się jasne, że ta innowacyjna metoda wykończenia oferuje niezrównaną trwałość i wszechstronność. Niezależnie od tego, czy mówimy o branży motoryzacyjnej, architektonicznej, AGD, czy meblowej – powlekanie proszkowe rewolucjonizuje sposób, w jaki upiększamy nasz świat: powierzchnia po powierzchni. Skorzystaj z oferty powłok proszkowych TIGER w naszym sklepie internetowym i odkryj świat możliwości dla swoich projektów wykończeniowych.
Back to overview