Introducción al Recubrimiento en Polvo
Antes de entrar en los detalles del proceso de aplicación del recubrimiento en polvo, dediquemos un momento a explicar el concepto de recubrimiento en polvo en su conjunto. El recubrimiento en polvo es uno de los avances más recientes en las técnicas de acabado de superficies más populares hoy en día. Surgió como un novedoso método de acabado en la década de 1960, y sus ventajas ecológicas lo convierten en la principal opción entre los sistemas de recubrimiento gracias a su composición sin disolventes. Esta tecnología puede alcanzar un grosor de revestimiento de aproximadamente 2-4 mils con una sola capa, lo que demuestra una eficiencia excepcional en el uso de materiales.
Además, el revestimiento en polvo ofrece unas propiedades mecánicas sólidas y una protección excepcional de los bordes, lo que garantiza que el producto acabado conserve su integridad y su aspecto. En particular, este método de acabado ofrece siempre resultados óptimos con una sola aplicación. Además, minimiza los residuos gracias a su notable tasa de recuperación del exceso de pulverización, que puede alcanzar el 95%. En definitiva, el recubrimiento en polvo resulta ser una opción rentable, que beneficia tanto al medio ambiente como a su presupuesto al reducir los gastos de material y aplicación.
Diferentes tipos de sustratos para los recubrimientos en polvo
La elección de los sustratos desempeña un papel crucial a la hora de determinar el acabado final, la durabilidad y la idoneidad para una amplia gama de aplicaciones. A continuación, exploraremos algunos de los sustratos de recubrimiento en polvo más comunes y profundizaremos en sus características y usos únicos.
1. Acero: Las estructuras de acero son uno de los sustratos más populares para el recubrimiento en polvo. Es duradero, resistente y versátil, lo que lo convierte en una opción excelente para diversos sectores. El acero con recubrimiento en polvo es habitual en piezas de automóviles, electrodomésticos, muebles de exterior y equipos industriales. Su capacidad para soportar condiciones ambientales adversas, como la exposición a los rayos UV y la humedad, lo convierten en una opción fiable.
2. Aluminio: El aluminio es otro de los sustratos preferidos para el recubrimiento en polvo. Presenta propiedades de ligereza y una excelente resistencia a la corrosión, por lo que es una opción ideal para elementos arquitectónicos, estructuras exteriores y componentes aeroespaciales. La superficie lisa del aluminio permite un acabado de recubrimiento en polvo impecable, realzando su atractivo estético.
3. Madera (MDF): Los sustratos de madera, en particular los tableros de fibra de densidad media (MDF), han ganado popularidad en los últimos años para aplicaciones de recubrimiento en polvo. Las superficies de madera con recubrimiento en polvo se utilizan en mobiliario, ebanistería y diseño de interiores, y ofrecen una amplia paleta de colores y un acabado duradero.
4. Plástico: El recubrimiento en polvo de sustratos plásticos es otro enfoque innovador. Mejora la durabilidad y la resistencia al rayado de los materiales plásticos, al tiempo que proporciona un acabado visualmente atractivo. Los sustratos plásticos, como el polietileno y el polipropileno, se utilizan en piezas de automóviles, equipos para exteriores y bienes de consumo.
5. Pultrusión (material compuesto): La pultrusión es un material compuesto elaborado a partir de fibras y resinas. Este sustrato fuerte y ligero es muy resistente a la corrosión, por lo que es adecuado para entornos difíciles. El recubrimiento en polvo de materiales de pultrusión se encuentra a menudo en estructuras como puentes, barandillas y plataformas marinas, donde la durabilidad y la longevidad son primordiales.
En esencia, el recubrimiento en polvo proporciona un acabado versátil y duradero para una amplia gama de sustratos. La elección del sustrato depende de la aplicación prevista y de las cualidades específicas requeridas, desde la resistencia del acero y el aluminio hasta las posibilidades estéticas de la madera y el plástico, pasando por los atributos especializados de los materiales de pultrusión. Ya sea con fines funcionales o decorativos, el recubrimiento en polvo ofrece una solución para mejorar el rendimiento y el aspecto de innumerables productos y estructuras.
Pasos del proceso de recubrimiento en polvo
El revestimiento en polvo es un proceso de acabado en seco que consiste en la aplicación de finas partículas de polvo cargadas electrostáticamente sobre la superficie de un sustrato. Este método de aplicación garantiza un revestimiento uniforme y consistente, sin goteos, descuelgues ni irregularidades.
1. Preparación y pretratamiento de superficies
Antes de aplicar el polvo, el sustrato debe someterse a una limpieza a fondo para eliminar cualquier contaminante como aceite, grasa u óxido. Este paso crucial garantiza una adhesión adecuada y un acabado impecable. El sustrato se libera de polvo, cascarilla, grasa, suciedad y cualquier capa de óxido (por ejemplo, en aluminio). Existen procesos de pretratamiento químicos y mecánicos. Para aumentar la protección contra la corrosión y mejorar la adherencia del revestimiento en polvo, durante el pretratamiento se crea una capa de conversión sobre la pieza. A continuación, la pieza debe secarse completamente.
Métodos de limpieza: El proceso de limpieza implica el uso de álcalis débiles y detergentes neutros, a menudo en tanques de inmersión o estaciones de lavado. Estas estaciones están equipadas para rociar las piezas con agua caliente, vapor, detergentes y otras soluciones de pretratamiento para limpiar y preparar químicamente la superficie antes del recubrimiento. Garantizan una base impecable para el recubrimiento en polvo.
Método de enmascaramiento para aplicaciones precisas: A veces, las piezas requieren que determinadas zonas permanezcan sin recubrir. Aquí es donde entran en juego los productos de enmascaramiento (puntos de enmascaramiento). Los hay de varias formas y tamaños, generalmente de papel o plástico recubiertos de un adhesivo sensible a la presión. Estas ingeniosas herramientas se adhieren al sustrato y evitan que las zonas cubiertas entren en contacto con la pintura en polvo durante el proceso de recubrimiento.
El Papel del Pretratamiento Químico: El pretratamiento químico implica el uso de productos químicos para limpiar la superficie, lo que favorece la adherencia del revestimiento en polvo sobre metales resbaladizos o difíciles. Este proceso suele realizarse mediante una serie de boquillas de pulverización o una inmersión alcalina. Las piezas se someten a varias etapas para garantizar una preparación óptima de la superficie. Los procesos de pretratamiento químico pueden ser automáticos, con una línea transportadora de varias etapas, o manuales, con piezas pulverizadas con varillas o mangueras.
En primer lugar, los sustratos se limpian con un limpiador alcalino, ácido o neutro (generalmente alcalino). A continuación, las piezas se tratan superficialmente con un revestimiento de conversión, tras lo cual un ácido graba la superficie para prepararla para las operaciones posteriores. El tipo específico de revestimiento de conversión puede variar en función del material que se vaya a revestir y de las propiedades deseadas del producto final. Normalmente se incluye una fase de aclarado entre cada fase de pretratamiento para eliminar los productos químicos y contaminantes residuales. Por último, se aplica un aclarado de ósmosis inversa o desionización para mejorar el rendimiento del revestimiento y reducir el uso de productos químicos de pretratamiento. Sin embargo, es importante tener en cuenta que este aclarado no debe contener cloruros ni fluoruros para evitar una mayor contaminación química.
Pretratamiento Mecánico para Contaminantes Difíciles: El pretratamiento mecánico implica el uso de medios abrasivos, lo que esencialmente significa frotar o esmerilar para pulir o limpiar un sustrato. Para determinadas aplicaciones en las que es necesario eliminar contaminantes inorgánicos como óxido, cascarilla de laminación y óxido láser, se prefiere este método de pretratamiento. Técnicas como el chorro de arena o el granallado utilizan aire a alta velocidad para impulsar materiales abrasivos (como arena, gravilla o granalla de acero) hacia el sustrato.
Esto crea un patrón de anclaje en la superficie de la pieza, mejorando significativamente la adherencia del recubrimiento en polvo al sustrato. Existen varios tipos diferentes de abrasivos, y su uso depende del tipo de acabado y contaminante que se desee eliminar. Por ejemplo, las cáscaras de nuez se utilizarán para desbarbar, mientras que la granalla de plástico se empleará para eliminar pintura. Del mismo modo, se prefieren las perlas de vidrio si el objetivo final es conseguir un acabado mate y satinado. La limpieza mecánica puede utilizarse de forma independiente o junto con un tratamiento químico. Aunque mejora la adherencia, no ofrece protección adicional contra la corrosión. En muchos casos, tras el granallado mecánico, la superficie se recubre con una imprimación adecuada para añadir protección adicional contra la corrosión. La imprimación también puede incorporar materiales que contengan zinc para mejorar aún más la protección contra la corrosión.
Buenas prácticas o aspectos a tener en cuenta para la preparación de superficies y el tratamiento previo.
- Limpieza y Desengrase: empiece con una superficie limpia y libre de contaminantes como aceite, grasa, suciedad u óxido. Utilice métodos de limpieza adecuados, como la limpieza alcalina, la limpieza con disolventes o la limpieza mecánica, en función del estado del sustrato y del tipo de contaminantes presentes.
- Abrasión: en algunos casos, especialmente con metales, pueden ser necesarios métodos abrasivos como el chorro de arena, el esmerilado o el grabado químico para crear una superficie rugosa. Esto mejora la adherencia del revestimiento en polvo.
- Capa de Conversión: para mejorar la resistencia a la corrosión, considere la posibilidad de aplicar un revestimiento de conversión como el fosfato de hierro o el fosfato de zinc. Este proceso altera químicamente la superficie para mejorar la adherencia del revestimiento en polvo.
- Aclarado: después de los pasos de limpieza y pretratamiento, asegúrese de realizar un aclarado a fondo para eliminar cualquier producto químico o contaminante residual. Los contaminantes restantes pueden afectar a la adherencia y el rendimiento del revestimiento en polvo.
- Secado: seque adecuadamente el sustrato para evitar la formación de manchas de agua o defectos superficiales en el recubrimiento en polvo. Se puede utilizar secado al aire, secado en horno o secado con aire forzado, dependiendo del sustrato y de las capacidades de la instalación.
- Selección del Método de Pretratamiento: elija el método de pretratamiento que mejor se adapte al sustrato y a los requisitos específicos del revestimiento. Por ejemplo, el fosfato de cinc es eficaz para sustratos de acero, mientras que la capa de conversión de cromo suele utilizarse para el aluminio.
- Medición del pH: los niveles de pH influyen en las reacciones químicas, la adherencia, la resistencia a la corrosión y la rentabilidad. Por eso, mantener el pH adecuado es esencial.
- Temperatura, Conductividad del Agua y Presión de la Boquilla de Pulverización: estos factores garantizan la coherencia, eficacia y calidad del proceso de tratamiento. Por tanto, asegúrese de controlarlos adecuadamente para obtener resultados óptimos.
¿Cómo cambia el proceso de pretratamiento en función de la selección del sustrato?
El tipo de sustrato que utilice puede influir mucho en el proceso de pretratamiento que siga.
- Acero: los sustratos de acero suelen pretratarse con fosfato de hierro o fosfato de zinc para mejorar la adherencia y proporcionar resistencia a la corrosión.
- Aluminio: los sustratos de aluminio requieren un enfoque diferente. A menudo se utiliza una conversión al cromo para mejorar la adherencia y la resistencia a la corrosión, especialmente en aplicaciones arquitectónicas o exteriores.
- Madera: para los sustratos de madera, se hace hincapié en la limpieza de la superficie y en garantizar que no haya humedad en la madera, que puede afectar a la adherencia.
2. Fase de Aplicación del Polvo - ¿Cómo se Aplican los Recubrimientos en Polvo?
En función de las necesidades de su proyecto y del tamaño de su empresa, existe una amplia gama de opciones de aplicación de polvo entre las que elegir. Pero, en general, hay dos métodos principales que se utilizan en todo el sector: La deposición Electrostática (ESD) y el recubrimiento en polvo de lecho fluidificado.
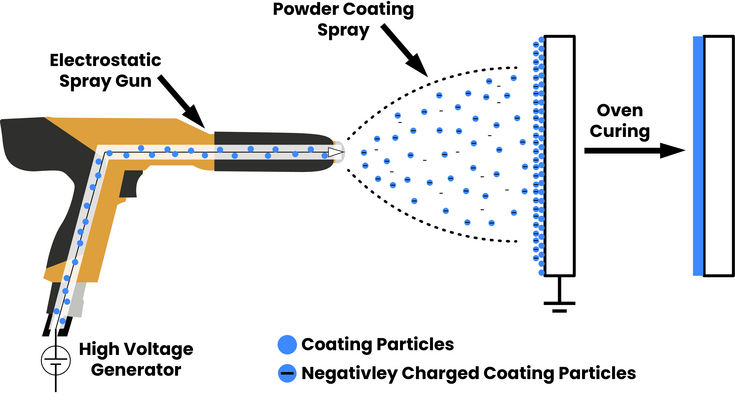
Deposición Electrostática (ESD)
El método ESD es el más común de los dos, sobre todo para el recubrimiento de piezas metálicas. El polvo se aplica con una pistola pulverizadora, creando una carga electrostática que atrae las partículas hacia el sustrato conectado a tierra. Esta atracción da lugar a un recubrimiento uniforme y eficaz. Es esencial evitar la entrada de polvo y suciedad en este paso. La pistola pulverizadora crea una nube cargada de polvo. Como resultado, las partículas de pintura se adhieren electrostáticamente a la pieza y forman una capa.
Una configuración manual típica de este proceso de aplicación implica los siguientes componentes:
- Cabina de Pintura en Polvo: sirve como espacio de trabajo para aplicar el material en polvo a una pieza. También actúa como filtro de aire y sistema de contención y recuperación del exceso de pulverización.
- Alimentador de Polvo: esta unidad distribuye el material en polvo a la pistola pulverizadora.
- Pistola Electrostática: la pistola imparte una carga eléctrica al polvo y lo aplica al sustrato. Existen tres tipos comunes de pistolas electrostáticas: Corona y Tribo.
- Pistolas de Carga Corona: son las más utilizadas y crean un campo electrostático de alta tensión y bajo amperaje entre el electrodo y el producto a recubrir. Las partículas de polvo atraviesan el campo electrostático ionizado, se cargan y se depositan en la superficie de la pieza conectada a tierra.
- Pistolas de Carga Tribo: en este tipo de pistola, las partículas de polvo adquieren su carga electrostática por fricción cuando rozan un aislante sólido o un conductor dentro de la pistola. Este proceso da como resultado partículas de polvo cargadas positivamente que eliminan el efecto de jaula de Faraday, un problema común con las pistolas Corona, lo que las hace perfectas para el recubrimiento de formas complejas. Es versátil - trabaja con polvos epoxi, acrílicos, nylon, teflón y poliéster, asegurando una aplicación suave y precisa. Además, es ideal para volver a recubrir piezas defectuosas.
- Sistemas de Recuperación: recogen el exceso de material pulverizado para reutilizarlo en futuras aplicaciones de revestimiento.
Los sistemas de pulverización son fundamentales en el proceso de aplicación de polvo, ya que ofrecen una aplicación de revestimiento eficaz y precisa en diversas superficies y geometrías de piezas. Los sistemas de pulverización en el recubrimiento en polvo incluyen componentes como el depósito de polvo para contener la pintura en polvo, una pistola de aplicación para pulverizar, un sistema de alimentación para transportar el polvo del depósito a la pistola, una unidad de control que regula y ajusta con precisión diversos parámetros de aplicación, así como sistemas de suministro y recuperación de aire. Entonces, ¿en qué consiste un buen sistema de pulverización de pintura en polvo? ¡Averigüémoslo!
Una característica notable de los sistemas de pulverización eficaces es su diseño apto para el mantenimiento in situ y la utilización de componentes de giro rápido. Este enfoque estratégico simplifica los procedimientos de mantenimiento, lo que reduce el tiempo de inactividad y garantiza un rendimiento continuo y fiable en las distintas tareas de recubrimiento. A la hora de considerar los sistemas de pulverización, preste atención también a la adaptabilidad y elija los que tengan configuraciones versátiles, ya que ofrecen flexibilidad para satisfacer diversos requisitos de recubrimiento. Otra consideración importante es el diseño innovador de la bomba, ya que mejora aún más la funcionalidad del sistema general al optimizar el consumo de energía, lo que contribuye a la eficiencia y la sostenibilidad de los procesos de recubrimiento.
Por último, cada vez son más comunes las unidades de control totalmente digitales, que proporcionan un control preciso de los ajustes electrostáticos y neumáticos. Este nivel de control es crucial para lograr un rendimiento óptimo del revestimiento, lo que en última instancia conduce a la elaboración de productos acabados de alta calidad.
Recubrimiento en polvo de lecho fluido
En cambio, el recubrimiento en polvo de lecho fluido es algo diferente. Así funciona:
- Precalentamiento: las piezas se precalientan para garantizar que el polvo se adhiera eficazmente. Debe alcanzar una temperatura de al menos 175°C, e idealmente entre 200 y 240°C. Esta temperatura elevada es esencial para mantener la pieza a una temperatura superior al punto de fusión del polvo. Normalmente, se utiliza un horno de convección de gas convencional para lograr este precalentamiento.
- Recubrimiento por inmersión: el siguiente paso consiste en recubrir por inmersión la pieza precalentada. Una bomba de aire facilita el flujo de aire a través del fluidizador de recubrimiento en polvo, creando una suspensión fluida de partículas de polvo. A continuación, la pieza caliente se sumerge en este lecho fluidizado de recubrimiento en polvo y se mueve para garantizar un recubrimiento continuo.
- Inmersión: la pieza permanece sumergida en el lecho fluidizado para permitir que la pintura en polvo cree un revestimiento grueso y resistente al desgaste. El grosor final del revestimiento depende del calor inicial del objeto antes de la inmersión y del tiempo que pase en el lecho fluidizado de pintura en polvo.
Post-fusión: la última fase del recubrimiento en polvo de lecho fluido es el proceso posterior a la fusión. Después de que el polvo sobrante gotee del producto, éste se transfiere a un horno a una temperatura más baja para su curado. Es importante que la temperatura de postcurado sea inferior a la del horno de precalentamiento inicial. Este paso garantiza que todo el polvo se adhiera a la pieza durante la inmersión y se funda en un revestimiento liso y uniforme. Si se utiliza una temperatura demasiado alta en el horno, pueden producirse resultados no deseados, como que el revestimiento se derrita, se descuelgue o gotee.
Aplicaciones automatizadas de recubrimiento en polvo
El uso de osciladores, reciprocadores y robots para gestionar los equipos de pulverización permite ahorrar costes y garantiza una cobertura uniforme en numerosas aplicaciones. La activación de la pistola, que consiste en encender y apagar automáticamente la pistola de pulverización en función de la posición de la pieza, reduce el exceso de pulverización y, por tanto, el consumo de material.
Importancia de la conexión a tierra y buenas prácticas al aplicar pintura en polvo
La conexión a tierra es posiblemente el aspecto más importante para el éxito de una aplicación de pintura en polvo. Decimos "posiblemente" porque se trata de una afirmación subjetiva y para otros, algunos factores pueden ser más importantes, ya sea el sistema de pulverización o el propio polvo.
Desde el punto de vista de la seguridad, las piezas sin conexión a tierra pueden acumular carga, lo que supone un riesgo de descarga eléctrica al acercarse a ellas. Esta descarga no sólo puede ser molesta, sino también peligrosa. Las descargas a través de pequeñas distancias entre las superficies cargadas y el suelo pueden contener energía suficiente para inflamar el polvo que se pulveriza desde la pistola, lo que acentúa aún más el aspecto de la seguridad.
A nivel de calidad, mantener una conexión a tierra sólida es crucial para conseguir un espesor de película y una uniformidad constantes en la aplicación de polvo. Sin una conexión a tierra adecuada pueden surgir problemas como la penetración de la Jaula de Faraday y la retroionización. Un estudio realizado por Kolene Corporation uso de manifiesto que mantener una excelente conexión a tierra durante el proceso de aplicación de polvo mejoraba significativamente la topografía de la superficie recubierta de polvo.
Por último, desde el punto de vista de los costes, una mala conexión a tierra afecta negativamente a la eficacia de la transferencia y al espesor mínimo de la película. Una conexión a tierra ineficaz puede dar lugar a un uso excesivo de polvo para lograr el espesor de película deseado, lo que aumenta los residuos y los gastos.
Para garantizar una conexión a tierra eficaz, es esencial disponer de una trayectoria trazable desde la pieza hasta la varilla de tierra, sin interrupciones en la conductividad eléctrica. El uso de una varilla de tierra de 2,5 a 3 metros, preferiblemente más larga en suelos de alta resistividad, y la medición de la resistencia entre las varillas de tierra pueden ayudar a garantizar una puesta a tierra fiable. El empleo de varillas de tierra de cobre macizo de longitud adecuada aumenta aún más la eficacia del sistema de puesta a tierra. En general, una toma de tierra adecuada es un factor crítico para conseguir seguridad y eficacia en las aplicaciones de recubrimiento en polvo.
3. Curado
Tras la aplicación, el sustrato recubierto se somete a un curado a alta temperatura en un horno. Durante este proceso, las partículas de polvo se funden y fusionan, formando un acabado robusto y duradero. El recubrimiento en polvo se cura en un horno a temperaturas de entre 110 y 250 °C. Diversos factores, como el tiempo de calentamiento y el grosor del sustrato, afectan al tiempo final de curado. Los recubrimientos en polvo termoendurecibles requieren una energía térmica y un tiempo específicos para desencadenar la reacción química necesaria para la reticulación en una película. Cuando se expone al calor, el material en polvo se funde, forma una película lisa y empieza a reticularse, alcanzando finalmente el curado completo. Se pueden emplear distintos métodos para proporcionar la energía necesaria para el curado.
Diferentes tipos de hornos de curado & significado y limitaciones de cada uno
Hornos de Convección: los hornos de convección utilizan una fuente de calor (normalmente gas natural) y un ventilador para hacer circular aire caliente por el conducto del horno. El aire caliente transfiere calor a la pieza y al revestimiento. Este es el tipo de horno más común para el curado de polvo. Cuando la pieza alcanza la temperatura deseada, transmite calor al revestimiento, lo que provoca el curado del polvo.
Hornos de Infrarrojos (IR): los hornos IR utilizan gas o electricidad como fuente de energía para emitir radiación en la banda de longitud de onda IR. Esta radiación es absorbida por el polvo y el sustrato, sin calentar significativamente toda la pieza. Este sistema permite un aumento más rápido de la temperatura, haciendo que el polvo fluya y se cure cuando se expone durante el tiempo suficiente. Sin embargo, la uniformidad del curado puede verse influida por la forma y la densidad de la pieza.
Tecnologías de Curado por Radiación: entre ellas se encuentran los procesos de infrarrojo cercano, ultravioleta (UV) y haz de electrones (EB). Estas tecnologías ofrecen aplicaciones potenciales para el recubrimiento en polvo de sustratos sensibles al calor, como madera, piezas de plástico y componentes ensamblados con características delicadas.
- Curado UV: se utiliza polvo especial que puede curarse al exponerse a la luz ultravioleta. Este polvo se calienta inicialmente, normalmente por infrarrojos o convección, hasta fundirse. A continuación, las lámparas UV proporcionan la energía necesaria para solidificar el revestimiento en cuestión de segundos.
- Curado por Infrarrojo Cercano: este método utiliza polvo especialmente formulado, fuentes de luz de alta energía y sistemas de reflectores precisos para completar el proceso de recubrimiento en polvo y curado en cuestión de segundos. Es especialmente útil para piezas ensambladas sensibles al calor.
Consejos para mejorar su línea de recubrimiento en polvo
Por lo general, las líneas de recubrimiento en polvo se miden en función de su eficacia, los desechos/defectos y los residuos generados. Lo ideal sería una línea de alta velocidad con un mínimo de repeticiones y desperdicio de material. Así que, con esto en mente, aquí tiene algunos consejos que le ayudarán a conseguirlo y a sacar el máximo partido de su proceso de recubrimiento en polvo.
- Mantenimiento de Equipos: mantenga y limpie regularmente todo el equipo, incluidas las pistolas de pulverización, los filtros de cabina y los hornos de curado. Un mantenimiento adecuado garantiza un rendimiento constante y prolonga la vida útil de la maquinaria.
- Gestión del Polvo: optimice el almacenamiento y la manipulación del polvo para evitar la contaminación y los residuos. Invierta en sistemas de suministro de polvo y contenedores de almacenamiento eficientes.
- Proceso de Pretratamiento: asegúrese de realizar una limpieza y una preparación de la superficie minuciosas antes de aplicar el polvo. Un tratamiento previo adecuado mejora la adherencia y evita defectos.
- Control de Calidad: implantar un sólido proceso de control de calidad, que incluya inspección, pruebas y seguimiento. Detecte y aborde los problemas en una fase temprana para evitar costosas repeticiones.
- Selección del Polvo: Elija el material de recubrimiento en polvo adecuado para su aplicación. Tenga en cuenta factores como el color, el acabado, los efectos, la durabilidad y la compatibilidad con el sustrato.
- Optimizar el Curado: ajuste la configuración del horno de curado para conseguir el acabado y el rendimiento deseados. Supervise la temperatura y el tiempo para garantizar un curado adecuado.
- Formación y Titulación: asegúrese de que su equipo está bien formado y homologado en técnicas de recubrimiento en polvo. La formación continua mejora los niveles de destreza y la coherencia.
- Gestión de Residuos: aplique prácticas eficaces de gestión de residuos para la recuperación del exceso de pulverización y el reciclado del polvo sobrante.
- Customization: adapte su línea de recubrimiento en polvo a las necesidades específicas de sus productos y clientes. No todas las empresas son iguales, por lo que una configuración personalizada será la más adecuada para mejorar la eficiencia y la calidad operativa.
- La Seguridad ante todo: dé prioridad a la seguridad de su equipo proporcionándole los EPI y la formación necesaria. Un entorno de trabajo seguro contribuye a la productividad general.
Acabados de Pintura en Polvo Más Populares de TIGER
TIGER Superdurables
Nuestros recubrimientos en polvo superdurables están especialmente formulados y rigurosamente probados para durar más de 10 años. Su extraordinaria resistencia a la corrosión, a los rayos UV y a la intemperie los convierte en la opción ideal para aplicaciones en exteriores, como la arquitectura y la industria del mueble.
Elija TIGER para Colores y Acabados de Pintura en Polvo de Alta Calidad
A medida que concluimos nuestro recorrido por los fundamentos del proceso de aplicación del recubrimiento en polvo, se hace evidente que este innovador método de acabado ofrece una durabilidad y versatilidad. Ya sea en el sector de la automoción, la arquitectura, los electrodomésticos o el mobiliario, el recubrimiento en polvo sigue revolucionando la forma en que embellecemos nuestro mundo: superficie a superficie. Aproveche el poder de la oferta de recubrimiento en polvo de TIGER en nuestra webshop y abra un mundo de posibilidades para sus proyectos de acabado de superficies.
Back to overview