Why PÖTTINGER relies on Powder Coating
Coloring of agricultural machinery not only has an aesthetic purpose, but is also an indicator for quality and durability. In an interview with Rudolf Mayrhuber, Head of Coating Technology at PÖTTINGER since 1996, we look into the question of why the company opted for powder coating, talk about initial challenges and their long-term partnership with TIGER.
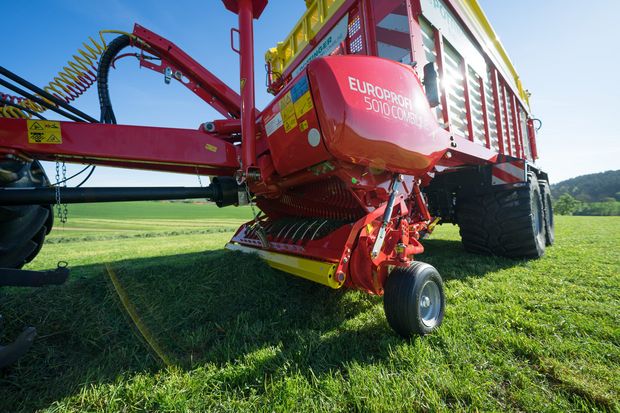
Info - PÖTTINGER Landtechnik GmbH
The Austrian family-owned company based in Grieskirchen specializes in farming, grassland management and digital agricultural technology. The extensive product range covers everything from ploughs, sowing machines, mowers and round balers to loader wagons and technology for crop care. The company's focus lies on reliability, efficiency and outstanding performance.
PÖTTINGER was founded more than 150 years ago as a small workshop, operates six production plants, 17 sales locations worldwide and employs around 2,200 people.
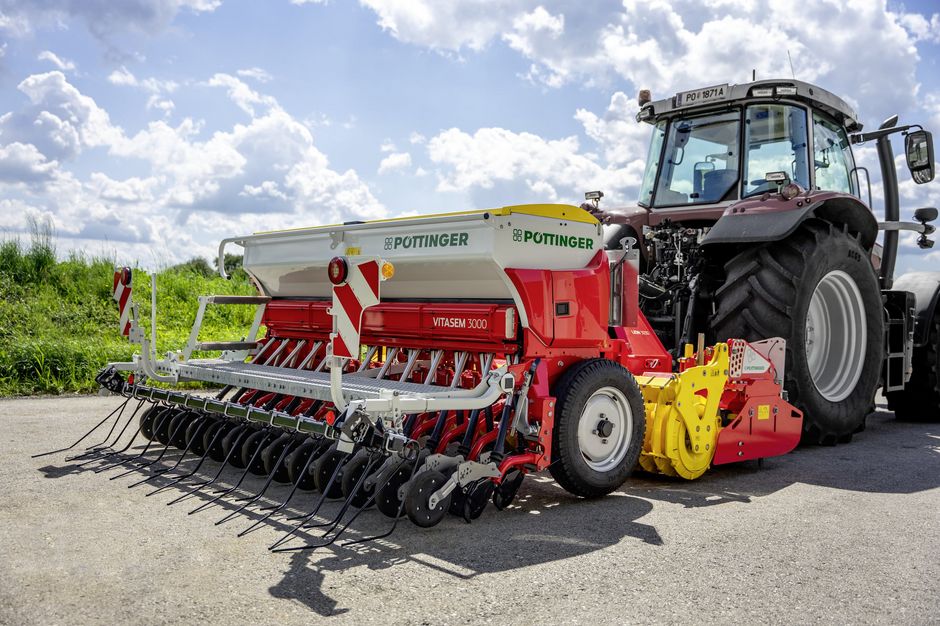
TIGER: What role does color play in your industry?
Rudolf Mayrhuber: As in many other industries, color plays an important role for recognition in the agricultural machinery sector. It helps to differentiate products and brands. For example, when I see a round baler or a plough in the field, I can recognize the brand from a distance thanks to the color of the machine.
TIGER: Which colors are predominant on PÖTTINGER machines?
Rudolf Mayrhuber: Like Ferrari, PÖTTINGER also uses red (laughs). The brilliant color was developed by TIGER exclusively for our company and is not available as a RAL color. We also use Black grey, Light grey and a sunny Colza yellow for our machines. This multi-colored finish is a special quality feature that is intended to highlight how we coat our parts individually. Unlike other manufacturers, our machine parts are first painted individually and then assembled. This means that the screw holes are also perfectly coated and the machines are fully protected against external influences such as corrosion.
TIGER: Agricultural Machinery is used outdoors during heat, rain and wind. What requirements do the surfaces of these machines have to meet?
Rudolf Mayrhuber: Reliability and durability are top priorities in the agricultural machinery sector. Particularly for contractors who take on a variety of agricultural tasks, heavy-duty equipment is essential. These machines work practically 24/7 and are confronted with a variety of challenges. To keep the resale value high, the visual appearance must still be impressive even after years of use.
TIGER: How long have you been working in your field and when was the first time you had to deal with powder coating?
Rudolf Mayrhuber: I have worked at PÖTTINGER for 48 years and will soon be retiring. As a trained mechanical engineer, I initially worked for several years in prototype construction, in the testing department and in preparation. I was actively involved in setting up the first powder coating plant in our painting center in Grieskirchen. The technology impressed me right from the start, and I am still enthusiastic about powder coating and its potential applications today.
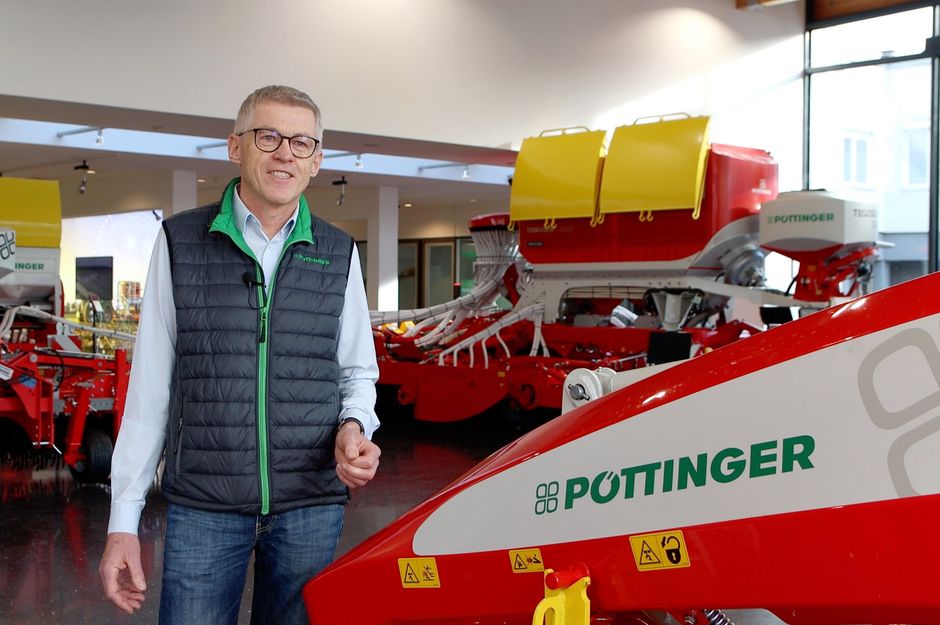
TIGER: Why did the company decide to use powder coating?
Rudolf Mayrhuber: In the mid-1990s, our liquid paint shop, which employed 35 people at the time, reached capacity limits. In addition, different environmental regulations were an issue. After reviewing several options - a process that was supported by external consultants - we decided on an investment project worth millions and built a 4,500 square meter facility featuring cathodic dip coating (CDC) and powder coating in Grieskirchen. The painting center went into operation in 1996 and has been managed by me ever since.
“When coating agricultural machinery, good edge coverage is more important than a smooth finish as required on facades. We therefore rely on the weather-resistant TIGER Drylac® Series 59 coatings, which have been individually adapted to our needs and also perfectly cover sharp edges on welded structures.
TIGER: What were the biggest initial challenges?
Rudolf Mayrhuber: We had zero experience with powder coating and were confronted with unexpected challenges at the beginning. The coating process itself worked perfectly - our liquid painters were retrained in powder and coped well with the new technology. Components that are coated with powder are transported on hooks through the powder booth and the curing oven. Initially, we only had two hooks for workpieces of different sizes. These in turn lacked the holes to be able to hang them properly. The throughput was correspondingly low at the beginning, and we also had a small wet paint shop in operation on the side.
Thanks to the Japanese philosophy of Kaizen, the permanent improvement of activities, processes or products by all employees, the process has gradually improved. The utilization of our powder coating plant rose sharply and one year later - in 1997 - we also started job coating. Our first customer was REFORM, the Wels-based manufacturer and developer of special vehicles for mountain and municipal technology. Today, we coat both in Upper Austria and in Vodňany in the Czech Republic, for example for Rosenbauer, Palfinger and Liebherr.
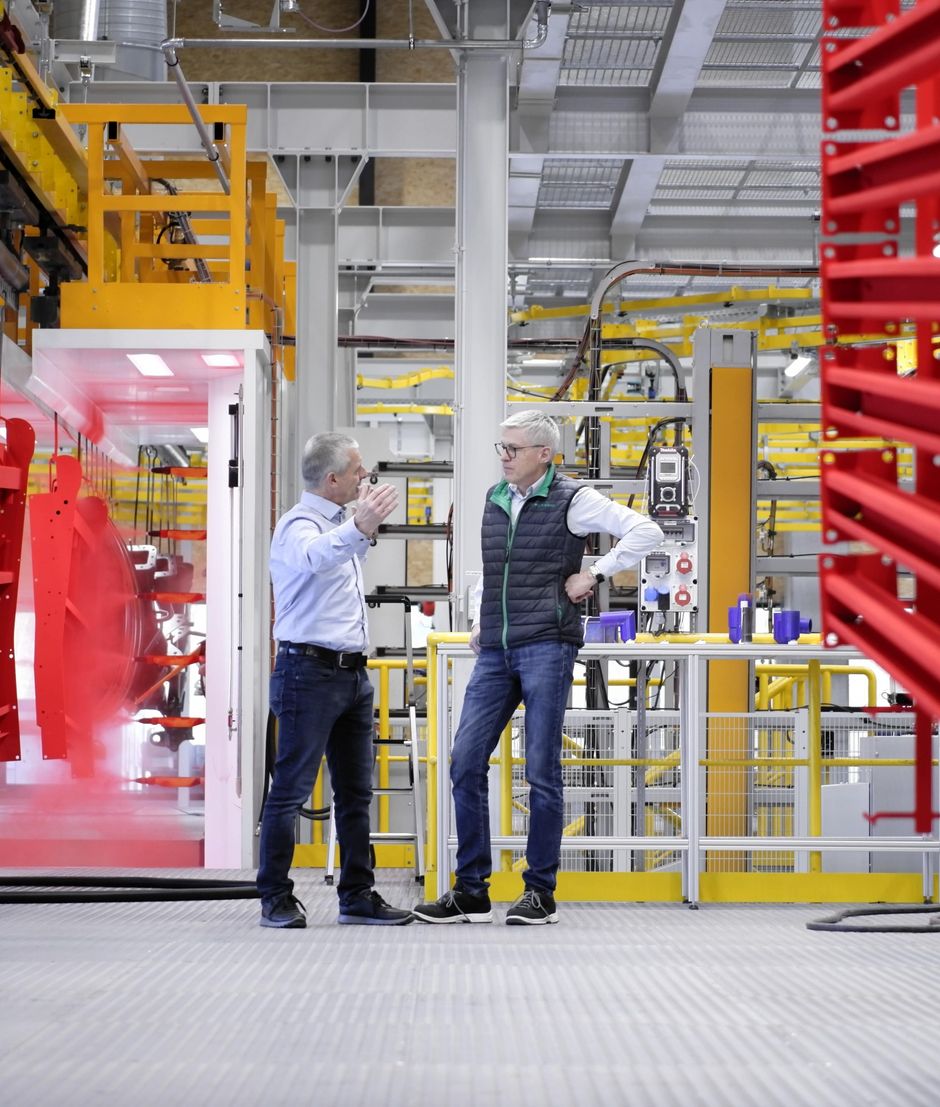
TIGER: How would you describe the partnership with TIGER in three words?
Rudolf Mayrhuber: Geographical proximity, personal contacts and an almost friendly relationship. You know when you need to call - the response time is excellent! Your sales representatives Michael Penner and then Norbert Huber were available at all times and always had an open ear for our concerns. Marcel Martin is now continuing this task in the same manner. Our consignment warehouse in Grieskirchen is stocked daily by TIGER with the five main PÖTTINGER colors. However, if we need more powder at short notice, we can pick it up in Wels directly.
TIGER: How long has PÖTTINGER been ordering powder coatings from TIGER?
Rudolf Mayrhuber: TIGER has been with us right from the start! We started together in 1996 and received perfect advice and support. Your laboratory team has developed our signature PÖTTINGER red in exterior quality.
TIGER: In 2023, PÖTTINGER put another state-of-the-art cathodic dip coating and powder coating facility into operation in St. Georgen near Grieskirchen. What were the reasons for this investment?
Rudolf Mayrhuber: Expanding capacity due to major growth in agricultural engineering! Our plants in Grieskirchen and Vodňany were already working at full capacity in three shifts, and we wanted to continue job coating. The demand for components that are powder-coated by PÖTTINGER is enormous! This is partly due to the outstanding quality of TIGER Drylac® and partly to the fact that we operate a sandblasting system and can therefore also optimally prepare rusted parts for the coating process, for example.
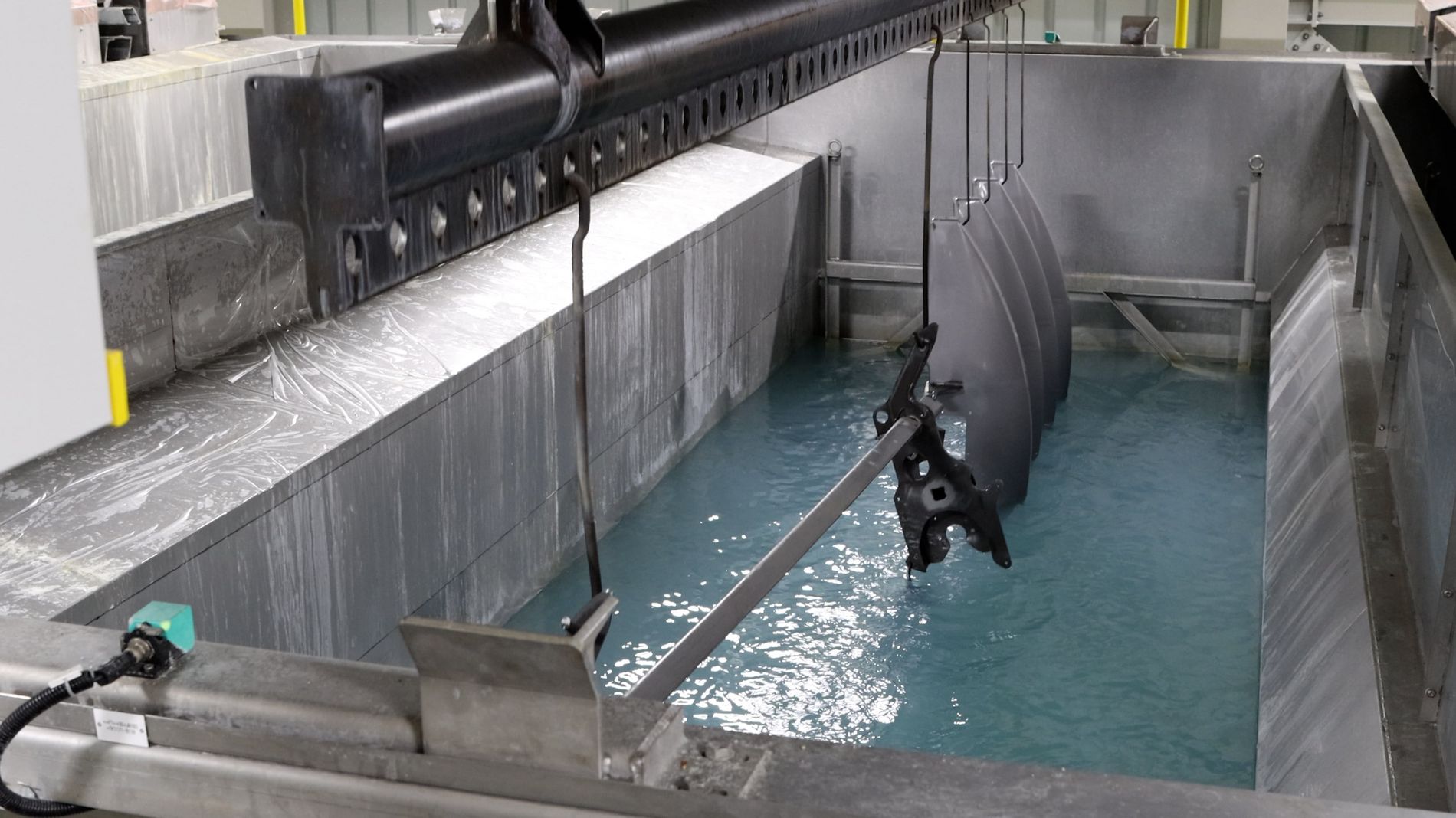
TIGER: Can you describe the installation in a little more detail and briefly explain the difference between cathodic dip coating (CDC) and powder coating?
Rudolf Mayrhuber: Basically, you can say that cathodic dip coating is used for priming and powder coating serves as the base coat. The multi-stage wet-chemical pre-treatment in the course of cathodic dip coating enables us to achieve outstanding corrosion protection. In combination with the perfect weatherability of powder coating, our components are optimally protected against external influences and ready for use on the meadows, fields and farmlands of this world.
TIGER: Your favorite TIGER Drylac® color?
Rudolf Mayrhuber: Our PÖTTINGER red, of course!
Back to overview