Scratching, Abrasion and Mar: How powder coating helps!
Outside appearance is directly associated with product quality. Decoratively finished workpieces should therefore look like new for as long as possible. This places a large number of demands on the coating: among other things, it must offer protection against abrasion and marring (=loss of material due to friction) and should have increased resistance to scratching (= forces exerted by sharp objects).
Potential Risks and Countermeasures
A properly applied powder coating, after thorough pre-treatment, provides the surface with strong protection against various mechanical stresses. However, this does not guarantee that damage cannot occur over time. Parts exposed to substances like sand, dirt, stone chips, brushes and aggressive chemicals are at special risks for scratching, abrasion and mar to happen.
The resin used in powder coatings is a critical factor, as some are offering more mechanical resistance than others. To further improve scratch, mar and abrasion protection, powder coatings can be engineered with certain additives in their formulation, which can be enhanced when required.
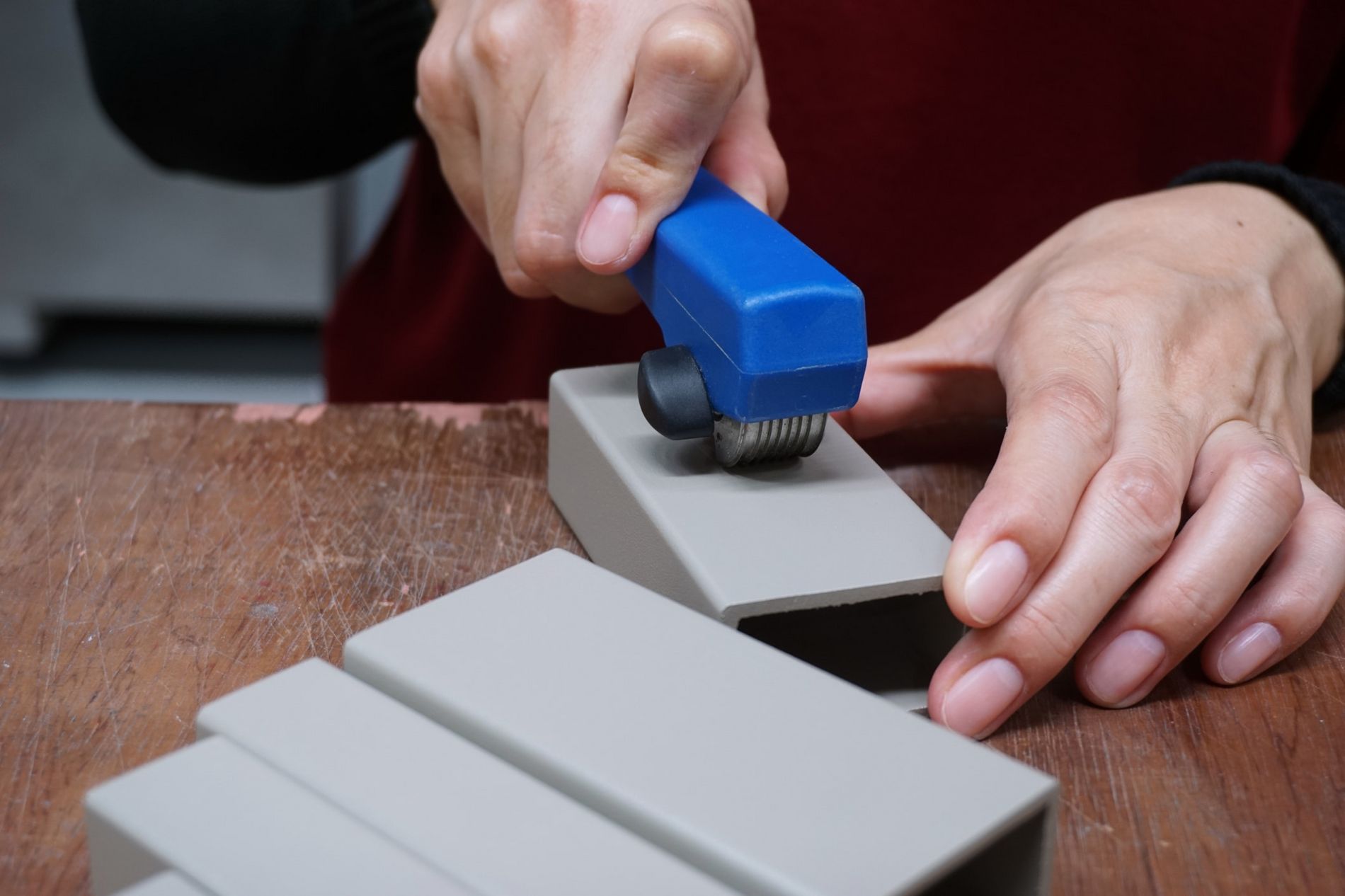
Which industries are particularly affected?
Architecture
Coated architectural components such as facade panels and window frames can be affected by scratching and abrasion even before installation. Mechanical stresses act on the components already as they pass through production - a clear risk to their later appearance. Once in use, scratching can occur, especially during cleaning. To prevent this, we recommend to always follow our General Cleaning Recommendations.
Furniture production
A piece of furniture is used every day - just as daily, it is moved, stacked on top of other furniture and/or contaminated by substances that chemically attack the surface. This results in a significantly increased susceptibility to damage.
Other outside applications
The already mentioned stresses to some extent apply to every piece of equipment, that is placed outdoors and/or in public areas. Public kiosks are a prime example for this, most often found in restaurants, malls and in the streets.
Going the extra mile for outstanding performance
With a TIGER AR (abrasion resistant) formulation, the abrasion resistance can be improved by up to 100% over that of a conventional powder coating (as measured by Taber® abrader testing), and with no additional wear-and-tear on the powder application equipment.
Most TIGER products are available in abrasion or scratch/mar resistant formulations upon request. Ask your TIGER Representative for additional details.
FAQs
Abrasion refers to the wear and tear of friction caused by mechanical parts and instances of repetitive scraping or rubbing, while Mar is described as physical deformations or markings that do not break through the surface. This includes gloss and shade differences.
In a laboratory environment the Martindale Test is very commonly used. Here a coated panel is rubbed against a surface at a specified force for a certain time period. Afterwards the results in e.g. gloss retention are compared.
Other common testing methods could be the Pencil Hardness Test (EN ISO 15184:2020), the Buchholz Indentation Test (EN ISO 2815:2003) or using a Manual Clemen Unit (EN ISO 1518:2019)
TIGER performs the following 3 lab tests:
1. Panel rub test:
Starts by performing 50 double rubs of 2 coated panels (same material), then a visual assessment is conducted.
2. Crock meter test:
Another lab test for mar resistance, commonly used in the automotive industry. Results are expressed as visual assessment or color / gloss retention after the surface is marred with crocking cloth or abrasive paper.
3. Scrub tester:
Also used in automotive industry this test is simulating car wash resistance. A coated panel is scrubbed with nylon bristle brush until failure occurs. Results are measured by the number of cycles until failure or measurement of color and gloss after 100 cycles. Scrub resistance is visually checked after 5,000 scrubs.
In the field the quickest way of testing for mar resistance is a simple coin mar test.
The TABER test is the most common method for testing abrasion resistance.
A coated panel is mounted on turntable that rotates at fixed speed. Then a weighted abrading wheel is lowered onto the panel. Results are measured by weight loss of coating per number of revolutions under a specified load (500g or 100g). The lower the mass loss → the better the abrasion resistance.
There are two ways of fixing a scratch in a powder coating. The choice depends on the severity of the damage:
- surface scratches: here, the surface is pretreated with a polishing agent and then sealed with another special agent. It should be noted here that this type of treatment can influence the gloss level of the surface.
- deep scratches: if scratches reach down to the substrate, the defect is usually repaired with wet paint. Coaters must pay special attention to matching the paint to reduce later inconsistencies in color and gloss level.
Back to overview