What Are Electrostatic Dissipative Powder Coatings And How Do They Work?
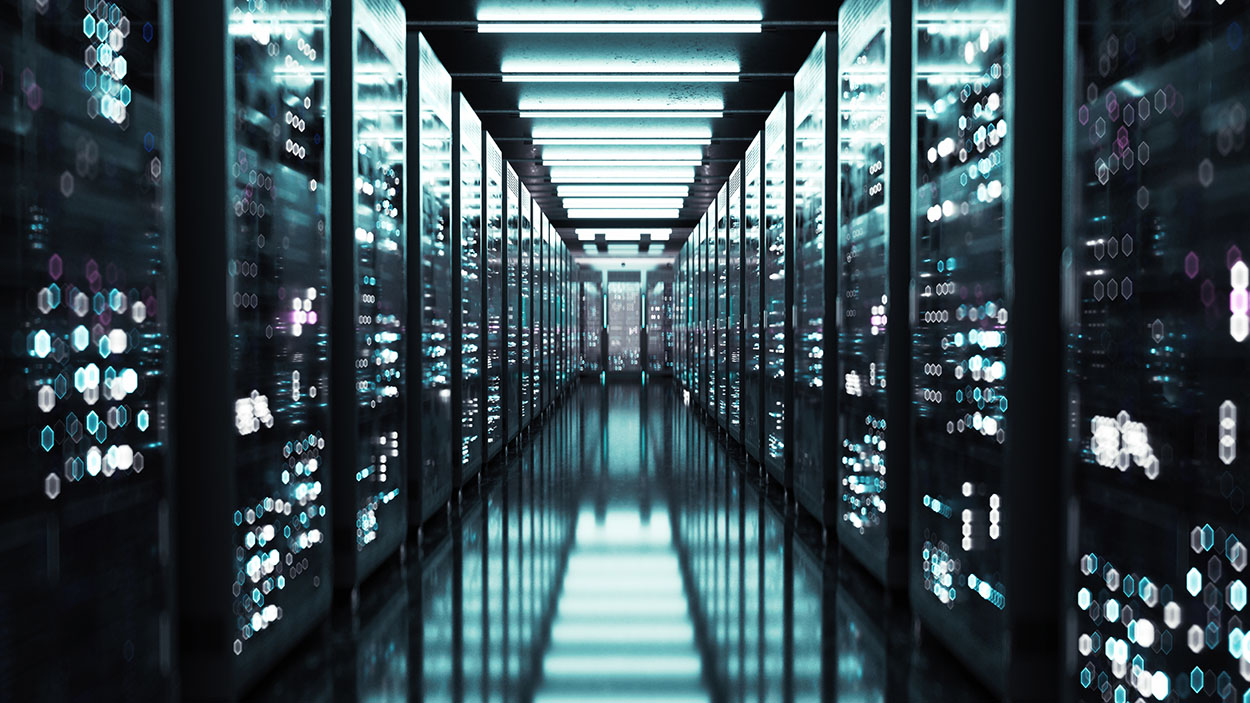
Electrostatic dissipative powder coatings are a specialized type of coating that provides protection against electrostatic discharge (ESD) by dissipating static electricity. They are commonly used in coating applications that deal with electronic appliances such as computers, electrical cabinets, and housings.
In this article, we will explore the characteristics and working principles of electrostatic dissipative powder coatings.
What Is an Electrostatic Charge?
Have you ever experienced a sudden shock when reaching out to pet your dog or witnessed your hair standing on end after removing a hat on a dry winter day? Maybe you've even marveled at a balloon sticking to a wall after rubbing it against your clothes. But what causes these peculiar occurrences? Is it some form of magic? Not quite! It's actually a fascinating phenomenon called static electricity.
At its core, static electricity arises from an imbalance between negative and positive charges within an object. These charges can accumulate on the object's surface until they find a means of release or discharge.
What Causes Electrostatic Discharges (ESD)?
Electrostatic discharge, commonly referred to as ESD, is an inevitable consequence of electrostatic charge. It occurs suddenly, creating voltage peaks of up to 100,000 volts between two objects. Traditional powder coatings, with their high electrical insulation properties (surface resistivity of over 1 Terra Ohm (1TΩ)), are unable to dissipate these voltage peaks. As a result, they pose a risk to electronic components and can even ignite dust explosions. This is why coaters dealing with products like electrical cabinets, housings, wire harnesses, and computers require specialized powders.
What Are Electrostatic Dissipative(ESD) Powder Coatings?
Electrostatic dissipative coatings are a special type of powder coating formulated with additives that promote conductivity and dissipate static charges. These coatings are applied as a dry powder and then cured to form a hard and durable finish. Unlike traditional coatings, electrostatic dissipative powder coatings have unique electrical properties that allow them to control and neutralize static electricity.
Buy ESD Coatings From Our Webshop
There are a wide variety of powder coating technologies used in many different industries. Coaters that are dealing with products that come in contact with electricity such as electrical cabinets, electrical housings, wire harnesses and computers require very specific powders. Thus, it is imperative to know how these powders will react to electrical charges.
How Do Electrostatic Dissipative Coatings Work?
To address the challenges posed by electrostatic discharge, electrostatic dissipative coatings have been developed. These coatings are specifically designed to counteract the buildup of charges on the surfaces of sensitive electrical equipment or components. They provide resistance to the flow of electric current and swiftly dissipate static electricity, ensuring minimal impact on the surrounding environment. However, it is essential that the substrate itself is a conductive material and a proper grounding mechanism is established.
The application of electrostatic dissipative coatings is primarily done using electrostatic spraying equipment, irrespective of the ambient relative humidity. In addition to their protective function, these coatings also offer aesthetic value, enhancing the appearance of the coated surface once they have cured. They also prevent the accumulation of particles, minimize the appearance of scratches and microorganisms, and provide corrosion resistance. Furthermore, electrostatic dissipative coatings offer enhanced resistance to UV radiation, ensuring color retention and a glossy appearance over time. To learn more about how powder coating can be made more conductive, check out our complimentary blog that delves deeper into the science behind ESD powder coatings.
Benefits of Electrostatic Dissipative Powder Coatings
Electrostatic dissipative powder coatings offer several advantages over traditional coatings, making them an ideal choice for industries where electrostatic discharge poses a risk. Some notable benefits include:
ESD Protection
The primary benefit of electrostatic dissipative powder coatings is their ability to protect sensitive electronic components from electrostatic discharge. By quickly dissipating static charges, these coatings prevent damage to circuitry, memory chips, integrated circuits, and other critical electronic parts. This helps to enhance product reliability, reduce failures, and minimize costly repairs or replacements.
Durability
Electrostatic dissipative powder coatings provide a durable finish that can withstand harsh operating conditions. These coatings exhibit excellent resistance to abrasion, impact, chemicals, and UV radiation. Consequently, they extend the lifespan of coated objects and maintain their appearance even in challenging environments.
Cost-Effectiveness
While electrostatic dissipative powder coatings may have a slightly higher upfront cost compared to traditional coatings, they offer long-term cost savings. The durability of these coatings means that objects coated with them require less frequent maintenance, repair, and replacement. Additionally, the protection they provide against electrostatic discharge helps to prevent costly damage to sensitive electronic components, reducing the risk of product failures and associated expenses.
Versatility
Electrostatic dissipative powder coatings are available in a wide range of colors, textures, and finishes, allowing for customization to suit specific aesthetic and functional requirements. Whether it's a sleek and smooth surface or a textured and slip-resistant coating, these coatings can be tailored to meet diverse application needs while maintaining their electrostatic dissipative properties.
Common Applications of Electrostatic Dissipative Coatings
So, where are ESD powder coatings used? The unique properties of electrostatic dissipative powder coatings make them highly suitable for various industries and applications. Some of the most widely known applications include:
Electronics Manufacturing
In the electronics industry, where the production and handling of sensitive electronic components are prevalent, electrostatic dissipative powder coatings are widely used. They provide protection against electrostatic discharge during manufacturing processes, assembly, packaging, and transportation, ensuring the integrity and reliability of electronic products.
Automotive and Aerospace
The automotive and aerospace sectors also benefit from electrostatic dissipative powder coatings. These coatings are applied to components, such as instrument panels, consoles, dashboards, and aircraft interiors, to prevent static buildup and potential damage to electronic systems. Additionally, electrostatic dissipative coatings on fuel tanks and other fuel-related parts help mitigate the risk of explosions caused by static electricity.
Telecommunications and IT
Telecommunications and IT infrastructure often involve sensitive electronic equipment, such as servers, routers, and data storage systems. Electrostatic dissipative powder coatings are applied to racks, cabinets, and enclosures to create a controlled electrostatic environment, minimizing the risk of data loss or equipment malfunction due to electrostatic discharge.
Conductivity of Different Types of Electrostatic Dissipative Materials
There are a wide variety of powder coating technologies used in many different industries. Coaters that are dealing with products that come in contact with electricity such as electrical cabinets, electrical housings, wire harnesses and computers require very specific powders. It is imperative to know how these powders will react to electrical charges. Materials are generally classified as insulators, static dissipative or conductive. These properties are a measure of resistance and resistance is the inverse of conductivity. The unit of measure is called ohms (Ω). The classifications are as follows:
- Insulating materials exhibit resistance greater than 1 X 109 ohms. Insulators have tightly bound electrons whose internal electric charges do not flow freely; very little electric current will flow through it under the influence of an electric field. Most powder coatings are in this range, with epoxy being higher than polyester. These type of applications can be found used to insulate wires, pipes and hoses.
- Static dissipative materials exhibit resistance between 1 X 106 and 1 X 109 ohms. For these materials, the charge flows through the material slowly and in a somewhat more controlled manner than with conductive materials. Dissipative materials are classified “Antistatic” and are considered to be the ideal range for ESD materials. These materials are widely used in and around all computer components to eliminate shock.
- Conductive materials exhibit resistance less than 1 X 106 ohms. Conductors have low electrical resistance, electrons flow easily across the surface or through the bulk of these materials. Charges go to ground or to another conductive object that the material contacts or comes close to. Metals have resistance of 0 to 0.1 ohms. Zinc rich will be less than 1 X 106 ohms. Conductive features are typically not sought after in the coatings that deal directly with electricity. One should always consult the engineer of the project as well as a powder coating specialist to make sure all requirements are being achieved.
Takeaways – Electrostatic Dissipative Powder Coatings
Going from a black color to a white color will change the resistance, also additives will influence based on their conductive nature, so If I add zinc to the same formulation, the resistance will drop as I increase the zinc level. If you are a manufacture or a coater of components such as electrical cabinets, robotics, computer housings and /or a surface that requires specific resistance to electricity, contact TIGER and let us help. We have stock options of powders that have been tested to the fullest measures. Visit our webshop to check out a variety of stock options of powders that have been tested to the fullest measures.
FAQs (Frequently Asked Questions)
Yes, electrostatic dissipative powder coatings can be applied over existing coatings as long as the surface is properly prepared and compatible with the new coating.
Electrostatic dissipative powder coatings are typically formulated to be environmentally friendly. They are free of volatile organic compounds (VOCs) and hazardous air pollutants (HAPs), making them a more sustainable choice.
Yes, electrostatic dissipative powder coatings can be used outdoors. However, it's essential to select coatings with UV resistance to ensure long-term performance and durability in outdoor environments.
Back to overview