Powder Coating Pretreatment : A Complete Guide
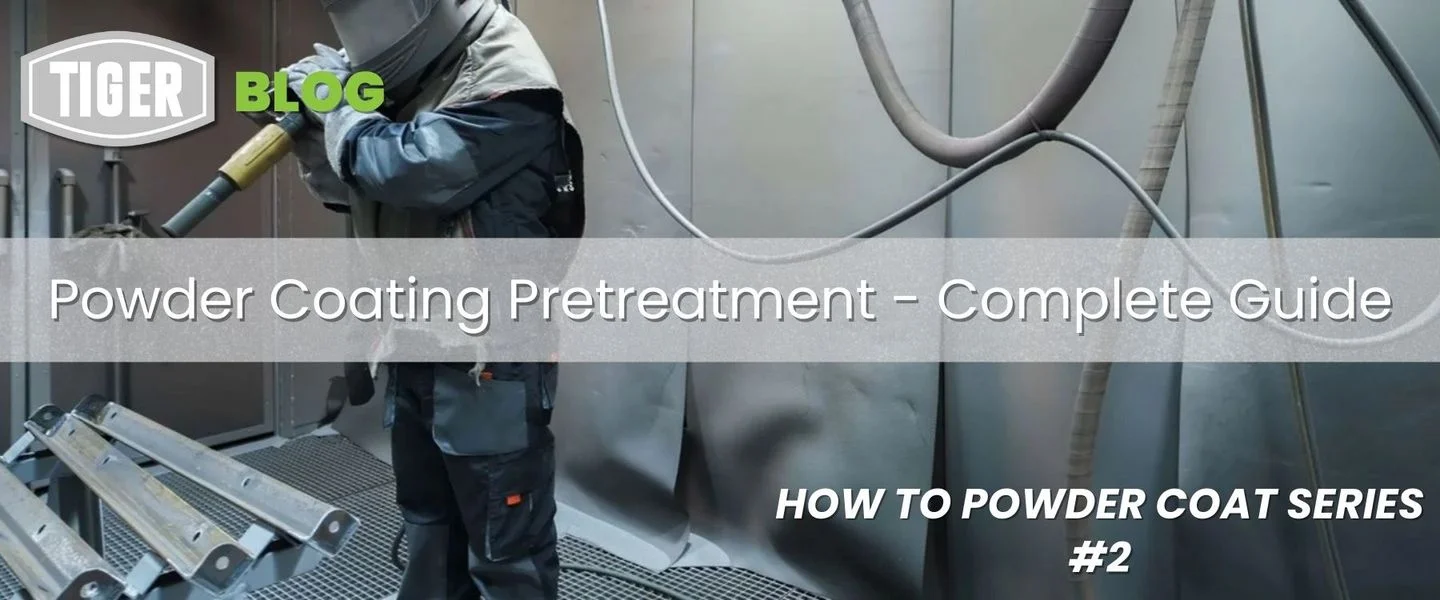
Please note: TIGER Drylac is not a pretreatment company, nor is this blog meant to be technical advice regarding the chemistry, application, or any methodology for the use of pretreatment. The applicator must consult with their chemical provider prior to any adjustment to the initially installed processes.
Powder coating pretreatment might sound like an overwhelming process with many technical aspects that need to be understood and done right for a perfect finish. It can sound daunting at first, but the process can be made easier to learn.
So, we have broken down the entire pretreatment process into a very comprehensive guide that can help you get started right away. Let’s dive in!
- Cleaning
- Types of Soil
- Mechanical Cleaning
- Chemical Cleaning
- Types of Chemical Cleaning Techniques
- How to Measure Cleanliness
- Conversion Coatings
- Rinsing
- Substrates
- Metal
- Wood
- Conclusion & FAQs
1: Cleaning
It’s crucial to thoroughly clean the surface by following the most suitable process for pretreatment for powder coating. If you don’t follow the cleaning step properly, then contaminants including dirt, oil, rust, or old paint can compromise the integrity of the coating. This will lead to poor adhesion, an uneven finish, and even diminished corrosion resistance.
Each surface may require a specific cleaning method based on the type of contaminants present and the desired quality results. By clearly defining the performance requirements, manufacturers can select an appropriate pretreatment approach that effectively addresses these contaminants while remaining cost-efficient. Proper cleaning ensures that the powder coating adheres well and meets the necessary aesthetic and functional criteria.
1.1: Types of Soil
Raw materials used in manufacturing often come with a variety of surface contaminants. For metals, these contaminants can include oily residues from petroleum products, animal fats, or vegetable oils used during operations including rust protection, machining, or forming. Additionally, heavy-duty drawing compounds, lubrication greases, waxes, carbon, graphite smuts, metal shavings, and rust or corrosion may also be present.
Organic contaminants, such as oils, greases, and residues from manufacturing processes, are typically carbon-based and can create weak bonds between the substrate and the powder coating, leading to adhesion issues. In contrast, inorganic contaminants, like dust, rust, or mineral deposits, are generally mineral-based and can affect the surface texture and uniformity of the coating. While organic contaminants often require solvents or degreasers for effective removal, inorganic contaminants usually need mechanical abrasion or acidic treatments to ensure a clean and suitable surface for optimal powder coating adhesion.
For cleaning, it is crucial to identify the specific types of contaminants. Conducting a thorough soil audit helps determine the appropriate mechanical or chemical cleaning methods and ensures that the chosen cleaner effectively removes all contaminants, thereby verifying the surface cleanliness before coating.
1.1.1 Rust inhibitors
These usually include paraffin waxes, lubricants, drawing compounds, oils, and other rust inhibitors made of petroleum oils. A good way to get rid of these would be to use alkaline chemical cleaners.
1.1.2 Shop Dirt
Dust and dirt from shops are commonly found contaminants on the surface of material you want to powder coat. Pretreatment for this kind of contaminant can include both mechanical and chemical methods.
1.1.3 Carbon
Carbon is found in both organic and inorganic compounds, and often appears as metal residue on steel alloys. This inert carbon residue, due to its electrostatic attraction to metal, can adversely affect coating adhesion. Substances like EDTA, Citric Acid, and DTPA are highly effective in breaking down this residue, unlike alkalis, solvents, or acids. Mechanical cleaning also proves efficient in removing carbon residues, ensuring a clean surface for optimal industrial powder coating application.
1.1.4 Oxides
Metal surfaces are prone to having oxides like Aluminum Oxide, Zinc Oxide, and Iron Oxide. This type of contamination acts as a barrier against powder coating film adhesion and can easily cause quality issues. Acidic solutions are highly effective in getting rid of oxides on metal surfaces.
1.1.5 Soaps
Heavy metal soaps, vegetable oil soaps, and soft soaps are sometimes found in products like metalworking fluids. To remove soaps from substrates before applying powder coating, you can rely on good mechanical action coupled with alkaline cleaners.
1.1.6. Polymers
Polymers are used mostly for their lubricity or releasing properties during many manufacturing processes. Silicone is an inorganic polymer and should not be present in paint shops because of their adhesion destroying attributes. There are also certain organic polymers like cellulose and phenolic materials that may be present on the substrate’s surface and need to be cleaned. Depending on the type of polymer, acids, solvents, detergents, and alkaline cleaners can be used to get rid of them.
1.2: Mechanical Cleaning
Mechanical cleaning is a process used in pretreatment for powder coating. It ensures surfaces are well prepared for a durable and high-quality finish. There are many methods that fall under this category. Three most common techniques include the ones mentioned below.

1.2.1 Media Blasting
One of the most robust mechanical cleaning methods is media blasting, which includes techniques like shot blasting. This process is also known as sandblasting. Sandblasting for powder coating uses abrasive particles propelled at a high speed to clean and profile surfaces. The sand blaster method effectively removes rust, old coatings, and contaminants. Similarly, shot blasting uses small steel or cast-iron balls to achieve a uniform surface profile. Both techniques are ideal for large-scale applications or heavy-duty cleaning, providing a clean, textured surface that enhances powder coating adhesion.
1.2.2 Grinding
For more aggressive surface preparation, grinding is employed. This technique uses abrasive wheels or discs to remove significant amounts of material, making it ideal for surfaces with heavy rust or substantial imperfections. Grinding is effective at smoothing out rough spots and preparing surfaces that require extensive cleaning or profile modification. It ensures a solid foundation for powder coating by addressing deep contaminants and surface irregularities.
1.2.3 Sanding
Sanding provides a finer approach for powder coating pretreatment process. With the help of abrasive paper or sanding discs, you can use this method to smooth out any remaining imperfections after initial cleaning. Sanding results in a uniform, smooth surface, ensuring that the powder coating adheres well and that the final finish is aesthetically pleasing.
1.3: Chemical Cleaning
Chemical cleaning involves removing oils, dirt, and other types of soil that can contaminate the surfaces that you want to powder coat. Chemical cleaning methods might be a good fit for certain applications but not for some others.
When it comes to chemical cleaning, technique alone is not enough to achieve the best results in powder coating pretreatment. Choosing the right chemical cleaners for powder coating should be your priority for getting desired results.
For effective pretreatment, several types of cleaners including alkaline cleaners, neutral cleaners, and acid cleaners should be considered. Each type of cleaner offers distinct advantages. For example, alkaline cleaners are known for their ability to manage a broad spectrum of soils, while neutral cleaners also function as detergent additives to enhance cleaning efficiency. Acid cleaners, on the other hand, target specific types of contaminants.
Chemical cleaners for powder coating are often categorized based on their pH levels—acidic solutions have a pH below 7, neutral cleaners have a pH of 7, and alkaline solutions have a pH above 7. Let’s look at these chemical cleaners in detail.
1.3.1 Alkaline Cleaners
Alkaline cleaners play a crucial role in metal treatment before powder coating. They can break down organic soils and offer versatile component options. These cleaners utilize a blend of alkalinity sources and surfactants to target and remove several types of soils / contaminants from metal surfaces. The effectiveness of an alkaline cleaner mostly depends on the chosen source of alkalinity, such as sodium or potassium hydroxide, which are known for their strong saponification properties that convert oils and fats into water-soluble forms. Sodium hydroxide is highly effective, but it can cause rinsing issues and can also attack certain metals. This leads to the widespread use of potassium hydroxide for easier rinsing and reduced metal aggression. Sometimes, carbonates, phosphates, and silicates are added as builders to enhance cleaning power, manage water hardness, and protect sensitive metals like aluminum.
1.3.2 Neutral Cleaners
Neutral pH cleaners are a specific category of surfactant-based formulations. They do not contain alkaline materials, making them ideal for handling light soils or non-saponifiable contaminants. Their gentle nature allows them to clean without altering the pH balance of the solution. This is particularly useful when dealing with sensitive surfaces.
Neutral pH cleaners are often employed as cleaning boosters by being combined with alkaline or acidic cleaners. This contributes to enhancing the overall cleaning efficiency when faced with more challenging residues. Their mildness makes them an essential tool in the powder coating pretreatment process, ensuring surfaces are thoroughly prepared without undue risk of damage.
1.3.3 Acid Cleaners
Acidic cleaners are best suited for specific metal cleaning applications like removing weld smut and rust. These cleaners leverage the power of acidic compounds, which, when combined with certain additives, effectively dissolve, and remove deposits from metal surfaces.
While the range of surfactants suitable for acidic environments is more limited compared to alkaline cleaners, they still play a crucial role in enhancing cleaning efficiency. Common acid cleaners used in industrial powder coating settings include phosphoric, hydrochloric, sulfuric, hydrofluoric, and sulfamic acids. Each acid offers unique benefits tailored to different cleaning challenges to help prepare metal for powder coating.
1.4 Types of Chemical Cleaning Techniques
Now that you have learned about the various types of chemical cleaners used of chemical cleaning, let’s learn more about the different types of chemical cleaning techniques.
1.4.1 Hand Wipe
If you are concerned about how much it costs to powder coat and are looking for an inexpensive pretreatment, then hand wiping might be a good fit in terms of equipment cost. This is assuming that it is suitable for your application. This process involves applying chemical cleaning agents directly onto the surface with a cloth or sponge. This results in precise control and thorough removal of contaminants such as oils, dirt, and residues. Hand wiping can be advantageous for intricate or delicate components that can be damaged by more aggressive cleaning methods, ensuring a smoother finish after the powder coating process.
1.4.2 Immersion Cleaning
Chemical cleaning through immersion is used to pretreat parts for advanced powder coating, particularly suited for large, automated operations. This method involves dipping parts in a cleaning solution, which can be either static or agitated. While static immersion systems are simpler, they require a longer time compared to spray cleaning methods. Agitated immersion systems, on the other hand, lead to improved cleaning efficiency due to the physical movement between the solution and the parts. This agitation, achieved through air addition, blade mixing, or basket hoisting, accelerates the chemical reaction between the cleaning agent and contaminants.
Despite their effectiveness, dip systems need higher concentrations of cleaning chemicals and longer operation times. They can also leave residual chemicals or oils on the parts, which float to the surface of the solution. Therefore, chemical cleaners used in immersion cleaning are specially formulated to emulsify oils rather than allowing them to disperse.
1.4.3 Hand-Held Spray Wand
Hand-held spray wands or steam spray systems are great for cleaning parts in batch powder coating operations. These wands help you achieve an elevated level of precision and thoroughness. This method addresses stubborn soils and hard-to-reach areas that automated systems can sometimes miss.
Spray wands are used within a controlled booth environment that makes them suitable for pretreating larger parts that are otherwise difficult to transport. While effective, this process can become labor-intensive and less efficient for cleaning large quantities of smaller parts before powder coating.
1.4.4 Ultrasonic Cleaning
This type of chemical cleaning is a sophisticated technique that enhances the effectiveness of cleaning chemicals through high-frequency sound waves. For ultrasonic cleaning, transducers are placed either inside or outside the cleaning vessel, which generate sound waves that dislodge particles and contaminants from the material's surface. This technique significantly improves cleaning efficiency by removing dirt and contaminants from even the most intricate or complex geometries, including blind holes.
It is important to note that ultrasonic cleaning is generally less efficient for larger loads, as heavy or large parts can obstruct each other and reduce overall cleaning performance.
1.4.5 Recirculating Spray Washers
Recirculating spray washers help in achieving a thorough chemical cleaning of parts before applying your thermosetting powder coating. These machines operate in multiple stages, each equipped with different solutions tailored to specific cleaning requirements. Although this is a more costly and maintenance-intensive cleaning technique, recirculating spray washers offer unmatched efficiency for continuous industrial coating applications. This technique is capable of handling large volumes and can deliver excellent cleaning results.
1.5: How to Measure Cleanliness
Once you’ve followed all the cleaning steps for your powder coating pretreatment process, determining the results of the process also becomes very important.
There are several methods that can be used to evaluate the substrate’s cleanliness.
Out of all such methods, here are some of the most popular approaches:
-
White Cloth Wipe Test: Wiping the surface with a clean white cloth can help identify residual inorganic or particulate matter like carbon smut. Although not foolproof, this method helps to quickly monitor cleanliness before you transfer your substrate into the powder coating booth.
-
Water-Break-Free Test: Observing if water beads up or sheets off the surface is another practical way to check for organic residues. A “water-break-free” surface means that there are no contaminants / soil present that could affect the powder coating adhesion.
-
Scotch Tape Test: To evaluate the presence of soils like carbon smut and weld smoke, you can apply a clear adhesive tape to the surface and then examine the particulate matter that gets stuck to the tape. This method is good for providing a relative measure of cleanliness.
-
Residue Testing: This is a quantitative approach involving solvent extraction to remove residual soils, followed by evaporation, and weighing of the remaining residue. This technique provides precise measurements of surface cleanliness.
-
Black Light Test: Using a black light to detect fluorescent dyes or oils can reveal residual soils that glow under ultraviolet light. This method is effective if the soil used in testing is known to shine under UV.
-
Contact Angle Water Drop Test: By measuring the contact angle of a water droplet on the surface, you can get an accurate assessment of cleanliness. This test yields the best results when performed in laboratory settings.
-
Infrared (IR) Spectroscopy: Analyzing solvent or salt pellets used to clean or assess the surface for residual soils can offer a detailed analysis of the remaining impurities. This is helpful in confirming surface cleanliness.
All the above methods provide valuable information related to the cleanliness of substrates, ensuring optimal performance of powder coatings.
2: Conversion Coatings
Conversion coatings are an important part of the powder coating pretreatment process. This step includes a chemically applied treatment designed to improve adhesion and corrosion resistance on clean metal surfaces.
The most used types of conversion coatings are iron and zinc phosphate. Some other well-known ones include manganese, chromate, zirconium-based, and vanadium/zirconium-based coatings.
These coatings work by converting the metal substrate into a uniform, inert surface that improves paint adhesion, limits corrosion spread if the coating is damaged, and enhances the overall corrosion resistance of the final product. In this pretreatment process, which is applicable to both ferrous and nonferrous surfaces, the parts are immersed in an acidic bath. This creates a complete chemical film on the metal surface and alters its chemical and physical properties.
2.1 Iron Phosphate
Iron phosphate conversion coating creates a thin, often uneven layer of metal phosphate on an iron oxide base, resulting in a surface that exhibits a gray to blue finish. The formulation of this coating includes phosphate salts, accelerators, or oxidizers, and optionally, a surfactant package.
The choice and concentration of these components can have a significant impact on the performance and appearance of the final coating. The applications of this coating can vary, from hand wiping to immersion and spray washers, with the spray washer being the most popular method.
The effectiveness of this conversion coating depends on factors like time, temperature, chemical concentration, and ph. All these factors play a crucial role in achieving the desired coating weight and quality.
2.2 Zinc Phosphate
Zinc phosphate is a nonmetallic crystalline coating that adheres chemically to steel, and offers superior performance in adhesion, coating of recessed areas, and corrosion resistance when compared to iron phosphate. This conversion coating consists of phosphoric salts, accelerators, and zinc salts, but lacks a surfactant package.
It is important to note that zinc phosphate requires a separate cleaning and pre-conditioning stage due to its inability to clean and coat simultaneously. Before applying this coating, an activator - a mild alkaline solution with active titanium salts - is used to prepare the surface. This leads to the formation of a dense coating with optimal adhesion and corrosion resistance.
Key factors that influence zinc phosphate coatings include concentration, contact time, temperature, and pH, with precise control necessary to achieve consistent, high-quality results. The automobile industry frequently uses this coating for its brilliant corrosion resistance properties.
3: RINSING
Rinsing plays a crucial role in determining how successful your pretreatment processes will be. It is also a process that demands careful execution at every stage. Effective rinsing between process steps helps prevent residue build-up, which can further disrupt subsequent treatments and lead to issues like adhesion failure or early corrosion. The final rinsing stage holds particular significance, as residual soils or unreacted salts can worsen the coating’s durability.
If rinse water maintenance is neglected, salts can accumulate, affecting coating adhesion and corrosion resistance properties. Water impurities / salts can undermine the entire pretreatment process, shortening the final product’s lifespan.
You should follow a more aggressive spray pressure in the initial rinse to ensure thorough removal of residual alkaline cleaner. On the other hand, following a gentler approach in the final rinse will protect the conversion coating and prevent surface defects.
Some good rinsing practices include:
-
Regularly dumping rinse tanks.
-
Maintaining appropriate overflow rates, typically between 3 and 10 gallons per minute.
-
Keeping a check on rinse water hardness.
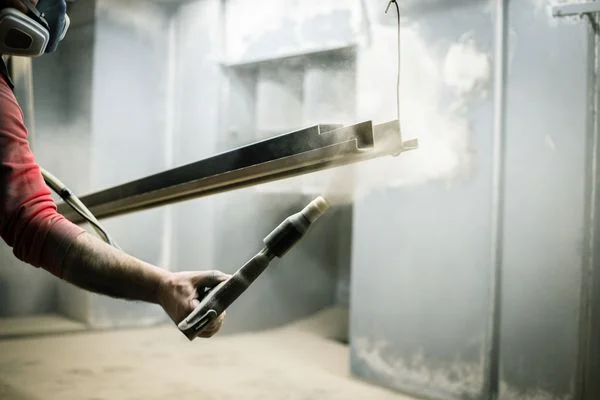
4: Substrates
Substrate is the material of the product that is going to be powder coated. The type of substrate you have, and the type of performance you want, will together determine the type of pretreatment you should do.
Various kinds of substrates have diverse kinds of soils / contaminants. For the variety of soils, there will be a corresponding variety of process sequences and different chemistry to choose from to get rid of them.
Let’s understand some common types of substrates for a better understanding of how to pretreat them for powder coating application.
4.1 Metal
When you’re discovering how to powder coat metal, it is equally important to learn how to pretreat metal substrates. Metal surfaces can form an oxide layer that impedes adhesion and the final finish. While you can use rust inhibitors like mill oil, it is helpful to know that they provide only temporary protection. Over time, these rust inhibitors degrade and can create compounds that affect the metal substrate’s finish, making it crucial to remove them and ensure the surface is oxide-free before painting.
Some metals that are widely coated include cold-rolled and hot-rolled steel, aluminum, galvanized steel, and cast zinc. While copper, brass, and stainless steel are less frequently used. The specific properties of these metals, influenced by alloying and heat-treating, must be understood to achieve a high-quality finish after powder coating.
4.1.1 Steel
Steel is the most prevalent substrate in manufacturing and is available in various alloys and forms. It is composed of iron and around 2% carbon, along with other alloying elements. This substrate’s characteristics vary based on its refining process. Initial refining produces rougher grades like structural steel and plate, while further refining reduces carbon and impurities and enhances quality.
The composition of steel has a substantial impact on the effectiveness of organic coatings. For instance, iron phosphate offers basic corrosion resistance, and zinc phosphate is preferred for more demanding performance requirements.
4.1.2 Aluminum
Aluminum is prized for its lightweight, corrosion-resistant, and highly conductive properties. It naturally forms an aluminum oxide layer that shields it from environmental elements. This substrate is available in various alloys and forms such as cast, extruded, forged, or rolled. All aluminum substrates require specific pretreatment for effective powder coating.
For achieving proper adhesion, aluminum substrates must be cleaned thoroughly. Powder coating lines handling both steel and aluminum often use agents like ammonium fluoride to clean these substrates. For outdoor applications, more robust treatments are necessary to prevent oxidation and maintain coating adhesion. Inadequate pretreatment can lead to moisture infiltration and accelerated coating failure.
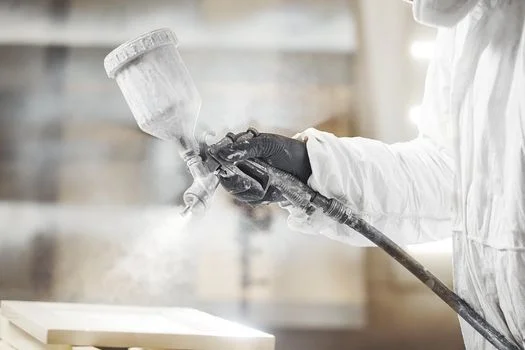
4.3 Wood
Like all other substrates, it is important to ensure that the wood substrate is free of all contaminants that can cause issues with the final coating. The wooden substrate might have blemishes on its surface that can either be a part of the material, or a result of contamination during machining operations. It is important that you get rid of such defects before coating.
You can try sanding the wood substrate between coats. This will improve the appearance if done with a fine grain and lighter touch. The goal here should be to remove raised grains from the surface and make it smoother for application.
Make sure to follow the most appropriate pretreatment technique for every substrate to get the best results!
5: Conclusion
This blog has given you a good idea about what powder coating pretreatment is, how to pretreat effectively before you powder coat, and all the different pretreatment techniques. Before you make the final choice on the type of pretreatment you follow, you should keep certain factors in mind, including the final desired finish, the type of substrate, the type of contaminants / soil present on the substrate, and the resources available to you for your project.
After you’ve completed the pretreatment stage, you should also conduct one final inspection before you move on to the powder coating application process. This step will help you identify any imperfections left behind that need to be treated before the application begins.
Please Note: TIGER Drylac is not a pretreatment company, nor is this blog meant to be technical advice regarding the chemistry, application, or any methodology for the use of pretreatment. The applicator must consult with their chemical provider prior to any adjustment to the initially installed processes.
FAQs
A. The steps you should follow completely depend on the type of finish you want, the resources you have, and the substrates you are working with. However, most powder coating pretreatment processes start with cleaning, followed by rinsing, and then application.
A. Priming metal before powder coating can help prepare the substrate for installation in more corrosive environments where it can deteriorate quickly. For instance, in the case of installation in external environments, using a primer is suggested.
A. The type of material you are working with (metal, glass, wood, etc.), and the contamination it has on its surface will determine what chemicals you can use to clean the material. The most used ones include alkaline, acidic, and neutral cleaners.
A. The choice of powder coating primer depends on your substrate and application, for example, Zinc Rich primers are often used for steel, Zinc-free primers are used for aluminum, and Flex-cure epoxy primers are often used on parts with varying metal thicknesses. In addition, “OGF” type primers are available for cast substrates or parts which are prone to outgassing.
Pure epoxy powder coating primers are definitely worth exploring for a lot of applications. You can head to the TIGER Drylac Webshop to explore some of the best primers that will help you achieve the finish you desire.
Back to overview