How to Powder Coat – An Extensive Overview
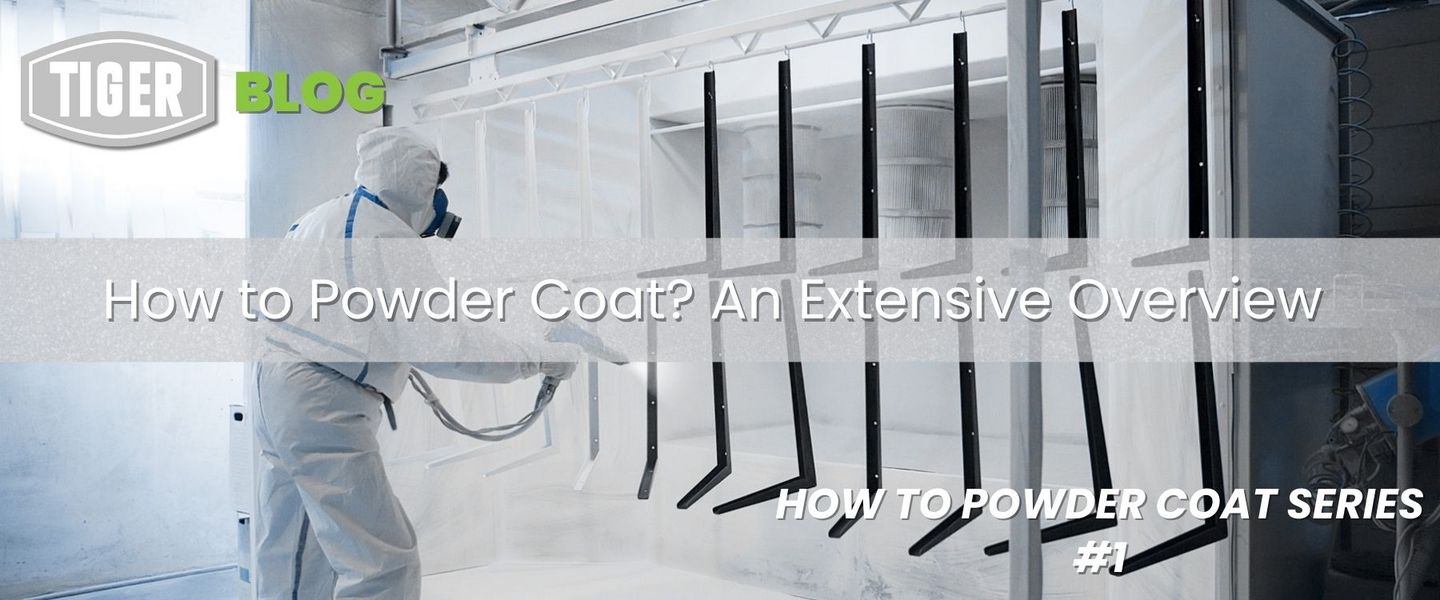
Your smartphone can help you learn a little something about the history of powder coating.
Curious? Let’s break it down.
Before smartphones, we relied on multiple devices like cameras, MP3 players, GPS units, and phones. Each device served its purpose but also required separate attention, maintenance, and sometimes a lot of space.
Similarly, before industrial powder coating, traditional painting methods that involved multiple stages, each with their own complexities, time-consuming processes, and hazards were used. Surface preparation, priming, applying multiple coats of paint, and waiting for each layer to dry or cure added a lot of time and effort to the process of painting.
When smartphones were introduced, they integrated all these functionalities into a single device. Now you can take photos, listen to music, navigate, and communicate - all from one device that fits in your pocket. This integration simplified life, reduced clutter, and made tasks more efficient.
The introduction of powder coating did something similar for the industries that relied on other forms of paint. Powder coating consolidated the surface finishing process into a streamlined, efficient method. With this new form of painting, you eliminate the need for multiple coats and long drying times. The powder is applied electrostatically in one step, adheres uniformly, and cures quickly under adequate heat, creating a durable and aesthetically pleasing finish.
Over the years, powder coating has emerged as a preferred method for applying protective and decorative finishes to a variety of surfaces, from automotive parts to household appliances.
This comprehensive guide has been put together to help you understand the fundamentals of how powder coating is done, its historical context, industrial applications, and more.
The Rise of Powder Coating
Origins and Development
The origins of powder coating can be traced back to the mid-20th century (1940s and 1950s) when researchers sought alternatives to traditional liquid paint applications. Initially used for functional coatings in industries such as automotive and appliances, powder coating gained popularity due to its environmental benefits and superior performance and quality when compared to solvent-borne (or liquid) paints.
Advantages of Powder Coating Over Liquid Paints
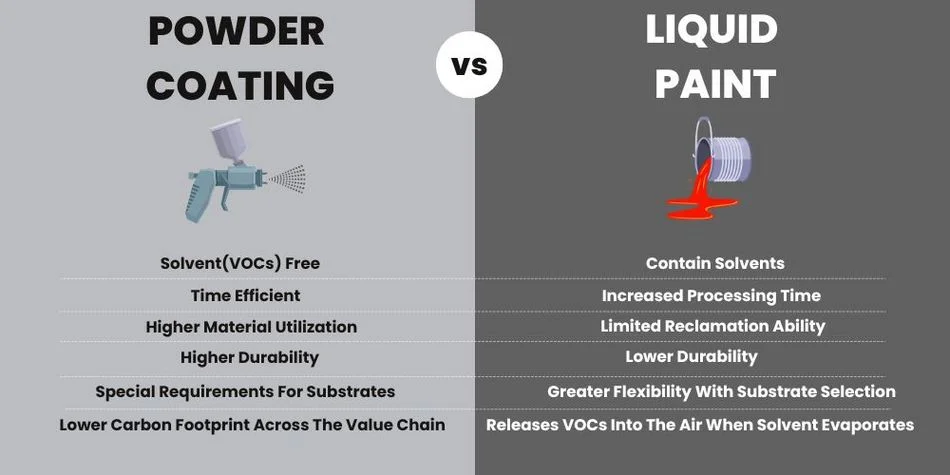
As previously mentioned, powder coating is more popularly used today than solvent borne (liquid) paints. Some of the advantages that contribute towards the popularity of powder coating are listed below.
Environmental Friendliness: Unlike liquid paints, which contain volatile organic compounds (VOCs) and require solvents to keep the resin and pigment in liquid form, powder coating is composed of finely ground particles of pigment and resin that are electrostatically sprayed onto a surface. This method eliminates VOC (volatile organic compounds) emissions and overspray, making it more environmentally friendly and efficient.
Durability: Powder coating provides a durable finish that is resistant to chipping, scratching, fading, and corrosion. This durability is crucial for industrial components exposed to harsh weather conditions, road debris, and chemicals of any kind.
Efficiency: The application process of powder coating is more efficient than liquid paints in terms of material usage and application time. Powder coating can be applied in a single coat without the need for multiple layers. This significantly reduces processing time and costs.
Aesthetic Versatility: Powder coating offers a wide range of colors, textures, and finishes, allowing manufacturers to achieve custom designs and branding requirements.
Health and Safety: The process of powder coating poses fewer health and safety concerns than solvent borne paints which put the workers at the risk of being exposed to solvent emission. Powder coating typically has a non-toxic nature which makes the workplace safer.
Industries That Use Powder Coating
Powder coating is a commonly used finishing technique in many industries. Some of the biggest ones are listed below.
Automotive Industry
One of the largest users of powder coating, the automotive industry applies this method to everything from vehicle chassis and wheels to engine components and decorative trim. Powder coating has changed the game for surface furnishing in automotives.
Powder coating rims, struts, metal racks, exterior trim, and other chassis parts provide robust protection against corrosion, UV damage, and everyday wear and tear. Manufacturers in the automotive industry also prefer powder finish over liquid paints due to their ability to withstand harsh environmental conditions while maintaining a customized and vibrant finish.
When it comes to specializing in this sector, TIGER Drylac ® is a trusted manufacturer of powder coatings for automotive industrial applications for both OEM and Aftermarket use cases. We have a specific list of automotive powder coatings that have been approved by several large OEMs.
Furniture
Powder coating patio furniture, indoor metal furniture like refrigerators, ovens, and washing machines is quite common these days. Powder coating provides a anti-corrosion coating for steel and other metal furniture. It also protects your valued pieces from scratches and fading, making them truly timeless.
Furniture makers appreciate the variety of options that powder coating comes with. They can choose any kind of surface finish, texture, and color to get their desired outcome. Along with extending the longevity of your furniture, powder coating metal also enhances its visual appeal.
We offer a range of powder coating colors that you can pick your favorites from for your next furniture project. Find out more about TIGER Drylac ® powder coating furniture applications here.
Architecture
Classic, modern, or industrial. Whatever you pick, all architectural designs have something in common – powder coating. Architectural powder coating combines aesthetic allure with practical durability. Whether its towering skyscrapers or the intricate architectural details, powder coating offers a spectrum of customizable finishes for metal structures, window frames, doors, and fencing. Unlike traditional liquid paints, techniques involving advanced powder coating deliver a uniform coat that can withstand chipping, corrosion, and fading. Textured powder coating is often used in architectural applications for an upgraded look and feel.
Powder coating is also an architect’s and construction manager’s top choice because of its unique anti-graffiti prevention properties. Anti-graffiti powder coating prevents paint-based vandalism without compromising the appearance of the surface.
Aerospace and Military Applications
An ideal finish combines performance with protection. This is exactly what powder coating stands for in the realm of aerospace and military. When compared with liquid paints, powder coating emerges as a winner for this industry. Let us look at some of the reasons why that is so:
- Powder coating is more sustainable than liquid paints.
The absence of harmful solvents and volatile organic compounds (VOCs), and the production of minimal waste, ensures that the federal agencies are reducing their carbon footprint.
- Enhanced longevity and functionality.
Powder coating contributes significantly to extending the lifetime of any aerospace or defense equipment by keeping it safe from environmental damage, fading, and corrosion. This also ensures operational readiness of the equipment.
- Customization options.
When it comes to defense and aerospace applications, powder coating provides tailored formulations that can enhance properties like adhesion, thermal stability, and much more. Additionally, this method of painting also helps in achieving the best texture and color required for different components.
As technology continues to shape the future of this industry, powder coating remains indispensable for engineers and designers aiming to push the boundaries of innovation and performance.
Job Shops
Job shops are specialized facilities that offer custom powder coating services tailored to meet the unique needs of individual clients and projects. Take for example, automotive parts requiring durable finishes or intricate metalwork needing a protective clear powder coating. Job shops excel in delivering high-quality results with precision and efficiency.
By partnering with job shops, businesses leverage their specialized equipment and technical knowledge to achieve superior surface finishing that can withstand harsh environments and rigorous use. These facilities typically offer a range of coating options, including polyester, epoxy, and polyurethane powders, each chosen for its unique properties like chemical resilience, UV resistance, and color retention. This diversity allows job shops to cater to a broad spectrum of powder coating applications.
Sports and Leisure
This industry thrives on a finishing that can withstand daily wear and tear and harsh external conditions. This is where powder coating plays a pivotal role in improving the durability and aesthetics of various equipment. For example, for cycling enthusiasts, powder coating a bike frame not only gives life to its appearance but also protects it against scratches, corrosion, and UV damage. Similarly, for skateboards and rollerblades, powder coating wheels makes them look better while also making them more resistant to abrasions and impact.
Powder Coating Process - A Brief Overview
The powder coating process has a few main elements that should be followed in the given order.
Preparation
Before applying powder coating, the surface needs to be thoroughly cleaned and treated to ensure adhesion and longevity of the finish. This step typically involves removing oils, rust, and other contaminants through methods like sandblasting, chemical cleaning, or phosphate treatment.
Application
During the application phase, the electrostatically charged powder particles are sprayed onto the grounded workpiece. This step results in the creation of an even coating that adheres electrostatically.
Curing
Once applied, the coated workpiece is transferred to a curing oven where it is heated to temperatures typically ranging from 300 to 450 degrees Fahrenheit. This elevated temperature causes the powder particles to melt and fuse into a smooth and durable finish. The curing time varies for different applications, depending on the powder formulation and thickness of the coating.
Cooling and Inspection
After curing, the powder coated item should cool down to room temperature before undergoing final inspection. As a last step, the quality control team performs several checks to ensure the powder coating meets specified thickness, appearance, and performance standards.
The entire process of powder coating involves a lot more details. It requires precision and knowledge about every stage to be able to produce a uniform coating.
How to Choose the Right Powder Coating System
When you are choosing the right powder coating system for your needs, consider these factors:
Size and Volume: Assess the size and volume of the items you intend to coat. For large-scale industrial applications, a conveyorized or batch system with robust capabilities may be necessary to handle high volumes efficiently. On the other hand, for smaller projects or DIY powder coating, a compact manual system would be more appropriate, offering flexibility and ease of use.
Type of Finish: Different powders require specific application techniques and curing processes. Metallic powders may need a system that ensures uniform coverage and proper curing to achieve specific visual effects. Understanding these requirements helps in selecting a system that supports the diversity of your coating needs.
Environmental Conditions: Some powder coating systems may require adequate ventilation or temperature controls to prioritize safety and quality of application. Additionally, you should also assess the energy efficiency and waste management capabilities of the system to ensure alignment with sustainable practices, reducing operational costs and environmental impact.
Budget Considerations: It is important to factor in the cost of powder coating and long-term maintenance requirements when choosing the right system. Remember, investing in a high-quality system can pay off in terms of reliability, efficiency, and longevity. So, look for systems with proven durability and support services that ensure ongoing performance and the lowest possible downtime.
By weighing all these factors carefully, you can confidently choose a powder coating system that aligns with your end goals, restrictions, and operational needs.
Supporting Your Powder Coating Needs
Our powder coating is trusted for a range of projects of all scales. We offer high-quality powders that ensure you reap the benefits of durability, aesthetic appeal, and longevity in an environmentally sustainable manner. The TIGER Webshop is your one-stop shop for a wide array of finishing options to take your project to the next level!
Check out some of our industry-specific resources to get more details.
FAQs
A. The powder coating process majorly involves three steps: Pre-treatment and surface preparation, application, and curing. This process is also often followed by quality inspection.
A. It is not recommended that you apply powder coating over existing paint since it can interfere with the chemical reaction that takes place when powder coating is applied. So, it is best to powder coat directly on the surface after it has been pre-treated.
A. When it comes to choosing the right material for powder coating, keep in mind that it needs to be able to collect and hold electrostatic charge and withstand high curing temperatures. Powder coating metal is therefore one of the most common materials.
A. Some of the most common problems arise from inadequate surface preparation before powder coating application. This can lead to issues like poor adhesion, uneven coating thickness, or defects like peeling. Proper cleaning, degreasing, and treatment of the substrate are crucial for a durable and smooth finish in powder coating applications.
Back to overview