Outgassing in Powder Coatings and how to prevent it
Outgassing describes the release of a gas or air that was dissolved, trapped, or absorbed in a material. Powder coaters may face specific issues related to outgassing when working with porous metal substrates like iron, steel and aluminum. These materials tend to release gasses when heated during the curing process. These gasses can then get trapped under the powder coating and create defects like bubbling or pinholes. A loss of interlayer adhesion is the consequence. In such cases rework is required. That’s why gasses and impurities must be released from the substrate prior to powder coating.
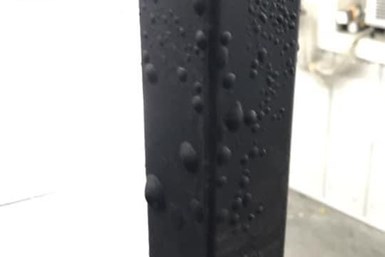
Why does Outgassing occur?
As to why Outgassing occurs, there are different factors, that lead to different causes:
- Castings: Contaminants are trapped into the casting material during the pouring process of both sand and die type castings. These contaminants can be from air trapped during the casting process or gas formed during the cooling of the molten metal.
- Galvanized Substrates: Outgassing can also occur when powder coating is applied to a zinc coated surface. The process of applying zinc to the steel substrate produces gasses (hydrogen gas) that can become trapped and then released during the curing process.
- Surface Contamination: Oil, grease or other organic residues (materials) tend to vaporize during the curing cycle and create surface defects.
- Coating Thickness: High film thickness may lead to outgassing during the cure cycle.
Can the damage be repaired?
Unfortunately, the defects created by outgassing require the part to be reworked. First one needs to strip the damaged layer, followed by proper cleaning and outgassing of the substrate. Then, a new powder coating can be applied.
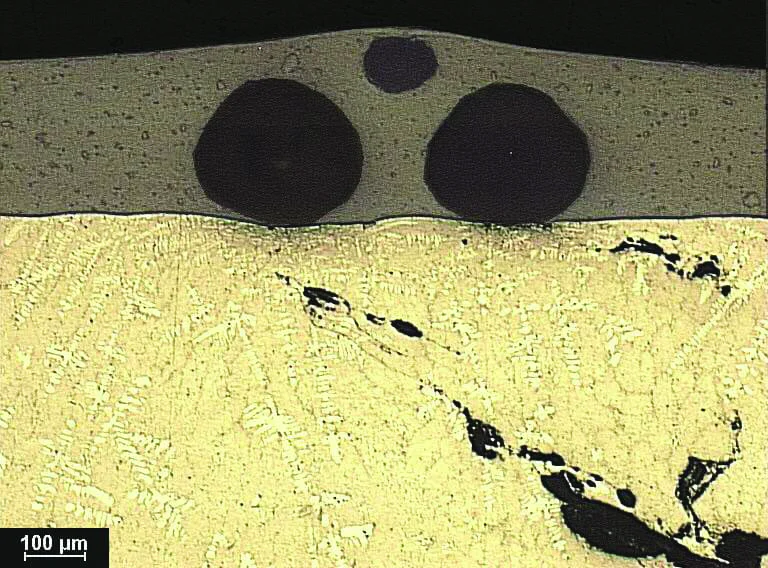
How to prevent Outgassing
To outgas the substrate prior to powder coating, follow these steps:
- Heat the substrate to a temperature at least 20 °C (68 °F) higher than the Part Metal Temperature (PMT) based on the Technical Data Sheet (TDS) for the coating.
- Coat the part before it cools to ambient temperature. This prevents air from re-entering the porosity of the substrate.
- Clean the surface. Parts must be free of contaminants such as oil, grease and other organic substances.
- Make sure to stay within the powder coating Technical Data Sheet (TDS) specification on film thickness.
- Use Outgassing-Forgiving powders when coating.
TIGER Outgassing-Forgiving Powder Coatings
For coating porous metal substrates, we have products, that help to deal with outgassing. In addition to our stock products, we can custom-formulate Outgassing-Forgiving (OGF) powders for basecoat primers or for single application topcoats. There also exists the possibility to work with our OGF-Additive, that can be blended with the powder onsite to mitigate the effects of outgassing!
Back to overview