The Powder Coating Process Explained - A Detailed Breakdown
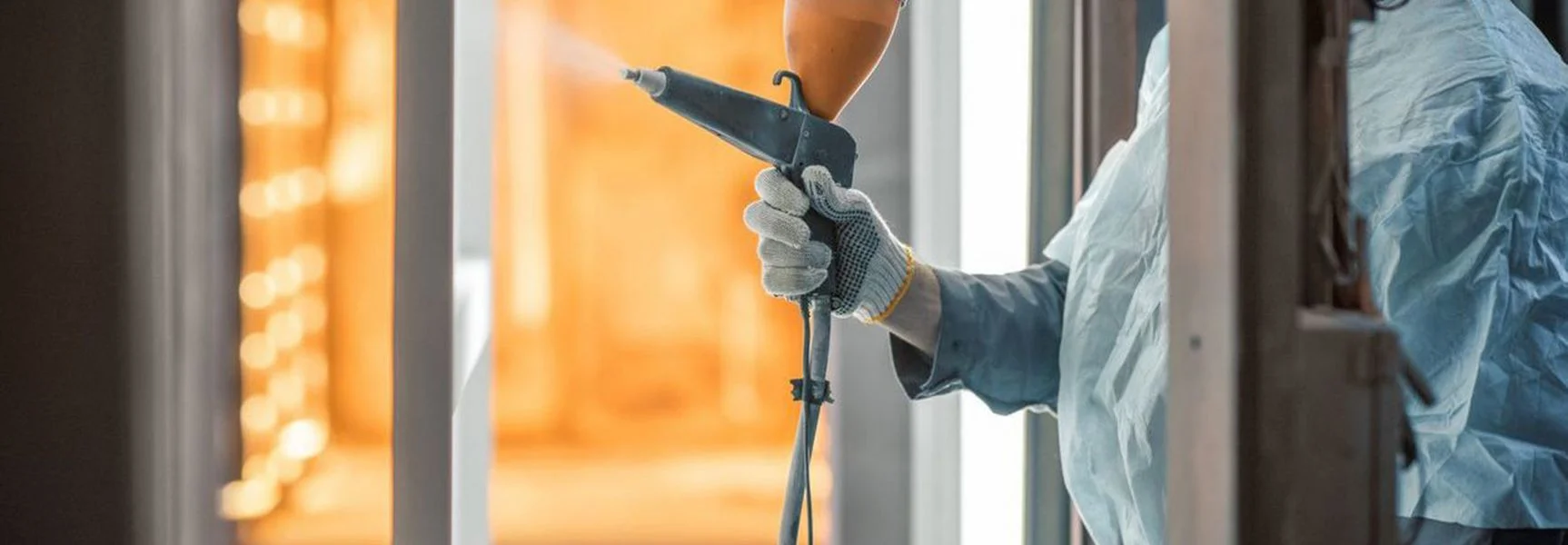
Introduction to Powder Coating
Before we go into the specifics of the process on how powder coating is applied, let’s take a moment to cover the concept of powder coating as a whole. Powder coating stands out as one of the most recent advancements in surface finishing techniques popular today. It emerged as a novel finishing method during the 1960s, and its environmentally friendly benefits make it the leading choice among coating systems due to its solvent-free composition. This technology can achieve a coating thickness of approximately 2-4 mils with a single coat, demonstrating exceptional efficiency in material usage.
Furthermore, powder coating delivers robust mechanical properties and exceptional edge protection, ensuring that the finished product retains its integrity and appearance. Notably, this finishing method consistently yields optimal results with just one application. Additionally, it minimizes waste through its remarkable overspray recovery rate, which can reach up to 95%. All in all, powder coating proves to be a cost-effective choice, benefiting both the environment and your budget by reducing material and application expenses.
Different types of powder coating substrates
The choice of substrates plays a crucial role in determining the final finish, durability, and suitability for a wide range of applications. Here, we'll explore some of the most common powder coating substrates and delve deeper into their unique characteristics and uses.
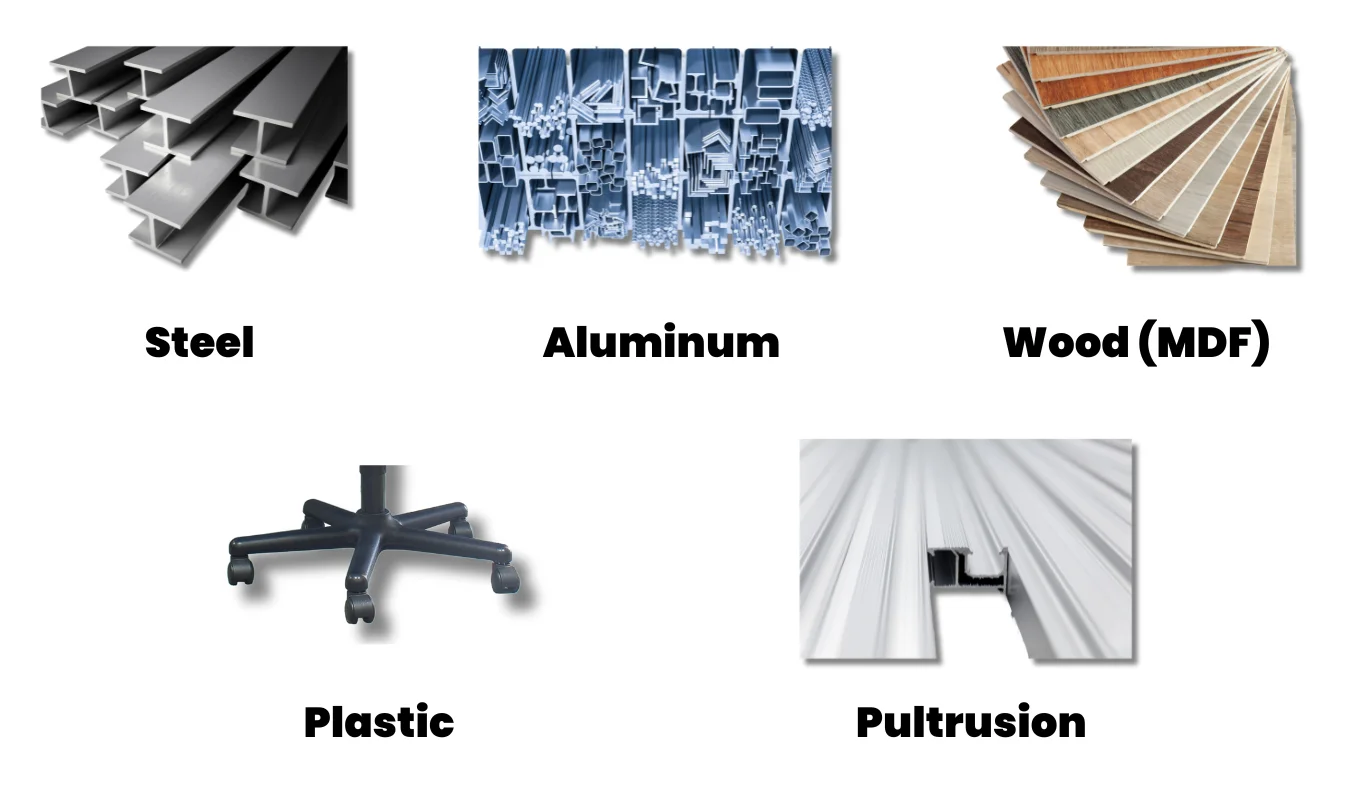
1. Steel: Steel structures are one of the most popular substrates for powder coating. It's durable, strong, and versatile, making it a prime choice for various industries. Powder-coated steel is commonly seen in automotive parts, appliances, outdoor furniture, and industrial equipment. Its ability to withstand harsh environmental conditions, such as exposure to UV rays and moisture, makes it a reliable option.
2. Aluminum: Aluminum is another highly favored substrate for powder coating. It boasts lightweight properties and excellent resistance to corrosion, therefore an ideal choice for architectural elements, outdoor structures, and aerospace components. The smooth surface of aluminum allows for a flawless powder coating finish, enhancing its aesthetic appeal.
3. Wood (MDF): Wood substrates, particularly Medium Density Fiberboard (MDF), have gained popularity in recent years for powder coating applications. Powder-coated wooden surfaces are used in furniture, cabinetry, and interior design, offering an extensive color palette and a durable finish.
4. Plastic: Powder coating on plastic substrates is another innovative approach. It enhances the durability and scratch resistance of plastic materials while providing a visually appealing finish. Examples for powder coatable plastic substrates include polyamide and our own 3D-Set material for SLS 3D-Printing.
5. Pultrusion (Composite Material): Pultrusion is a composite material crafted from fibers and resins. This strong and lightweight substrate is highly corrosion-resistant, making it suitable for challenging environments. Powder coating on pultrusion materials is often found in structures like bridges, handrails, and offshore platforms, where durability and longevity are paramount.
In essence, powder coating provides a versatile and durable finish for a diverse range of substrates. The choice of substrate depends on the intended application and the specific qualities required, from the strength of steel and aluminum to the aesthetic possibilities of wood and plastic, and the specialized attributes of pultrusion materials. Whether for functional or decorative purposes, powder coating offers a solution for enhancing the performance and appearance of countless products and structures.
Understanding the Powder Coating Process Steps
Powder coating is a dry finishing process that involves the application of fine, electrostatically charged powder particles to a substrate's surface. This application method ensures an even and consistent coating, free from drips, sags, or unevenness.
1. Surface Preparation & Pre-treatment
Before applying the powder, the substrate must undergo thorough cleaning to remove any contaminants like oil, grease, or rust. This crucial step ensures proper adhesion and a flawless finish. The substrate is freed from dust, scale, rust, grease, dirt, and any oxide layers (for example on aluminum). There exist chemical and mechanical pre-treatment processes. To increase the corrosion protection and improve the adhesion of the powder coating a conversion layer is created on the piece during the pre-treatment. Following this, the workpiece must dry completely.
Cleaning Methods: The cleaning process involves the use of weak alkali and neutral detergents, often in dip tanks or wash stations. These stations are equipped to spray parts with hot water, steam, detergents, and other pretreatment solutions to clean and chemically prepare the surface before coating. They ensure a spotless foundation for your powder coating.
Masking Methods for Precise Applications: Sometimes, parts require specific areas to remain uncoated. This is where masking products like masking dots come into play. They're available in various shapes and forms, generally constructed of paper or plastic film coated with a pressure-sensitive adhesive. These nifty tools adhere to the substrate, safeguarding the covered areas from meeting the powder material during the coating process.
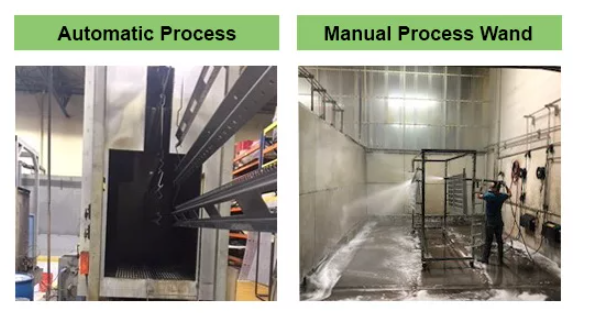
The Role of Chemical Pretreatment: Chemical pretreatment involves the use of chemicals to clean the surface, which promotes adhesion of the powder coating to adhere on slick or difficult metals. This process is typically carried out using a series of spray nozzles or an alkaline immersion dip. Parts undergo multiple stages to ensure optimal surface preparation. Chemical pretreatment processes can either be automatic comprising of a conveyer line with multiple stages or manual operated using spray parts with wands or hoses.
First, the substrates are cleaned using an alkaline, acidic, or neutral cleaner (generally alkaline). Following this, parts are surface treated with a conversion coating, after which an acid etches the surface to prepare it for subsequent operations. The specific type of conversion coating can vary based on the material being coated and the desired properties of the final product. A rinse stage is typically included between each pretreatment stage to remove any residual chemicals and contaminants. Lastly, a RO (Reverse Osmosis) or DI (Deionization) Rinse is applied to improve coating performance and reduce pretreatment chemical usage. It is important to note however that this rinse shouldn’t contain any chlorides or fluorides to prevent further chemical contamination.
Mechanical Pretreatment for Tough Contaminants: Mechanical pretreatment involves the use of abrasive media which essentially means rubbing or grinding to polish or clean a substrate. For certain applications where inorganic contaminants like rust, mill scale, and laser oxide need removal, this pretreatment method is preferred. Techniques like sand or shot blasting use high-velocity air to drive abrasive materials (like sand, grit, or steel shot) toward the substrate.
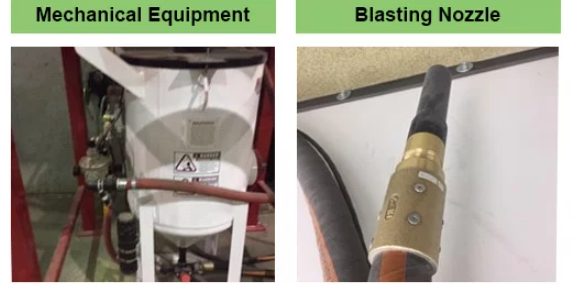
This creates an anchor pattern on the part's surface, significantly improving the adhesion of the powder coating to the substrate. Several different types of abrasives are available, and their use depends on the type of finish and contaminant to be removed. For instance, Walnut shells would be used for de-burring while plastic grit will be used to remove paint. Similarly, glass beads are preferred if the end goal is to get a matte and satin finish. Mechanical cleaning can be used independently or alongside a chemical treatment. While it enhances adhesion, it does not offer additional corrosion protection. In many cases, after mechanical blasting, the surface is coated with a suitable primer to add extra corrosion protection. The primer may also incorporate zinc-containing materials for further enhancements.
Best practices or things to keep in mind for surface preparation and pretreatment.
- Cleaning and Degreasing: Start with a clean surface free from any contaminants such as oil, grease, dirt, or rust. Use appropriate cleaning methods like alkaline cleaning, solvent cleaning, or mechanical cleaning depending on the substrate's condition and the type of contaminants present.
- Abrasion: In some cases, especially with metals, abrasive methods like sandblasting, grinding, or chemical etching may be necessary to create a roughened surface. This enhances the adhesion of the powder coating.
- Conversion Coating: For enhanced corrosion resistance, consider applying a conversion coating such as iron phosphate or zinc phosphate. This process chemically alters the surface to improve the adhesion of the powder coating.
- Rinsing: After cleaning and pretreatment steps, ensure thorough rinsing to remove any residual chemicals or contaminants. Contaminants left behind can affect the adhesion and performance of the powder coating.
- Drying: Properly dry the substrate to prevent the formation of water spots or surface defects in the powder coating. Air drying, oven drying, or forced air drying can be used, depending on the substrate and facility’s capabilities.
- Selection of Pretreatment Method: Choose the pretreatment method that best suits the substrate and the specific requirements of the coating. For example, zinc phosphate is effective for steel substrates, while chromate conversion coating is often used for aluminum.
- Measuring pH: pH levels impact chemical reactions, adhesion, corrosion resistance, and cost-efficiency. So, maintaining the right pH is essential.
- Temperature, Water Conductivity, and Spray Nozzle Pressure: These factors ensure consistency, efficiency, and quality in the treatment process. So, make sure to properly control them for optimal results.
How does the pretreatment process change based substrate selection?
The type of substrate you use can have a major influence on the pre-treatment process you follow.
- Steel: Steel substrates are typically pretreated with iron phosphate or zinc phosphate to enhance adhesion and provide corrosion resistance.
- Aluminum: Aluminum substrates require a different approach. A chromate conversion coating is often used to improve adhesion and corrosion resistance, especially for architectural or outdoor applications.
- Wood: For wooden substrates, the emphasis is on surface cleaning and ensuring there is no moisture content in the wood, which can impact adhesion.
2. Powder Application Phase - How Are Powder Coatings Applied?
Based on your project’s needs and the size of your business, there are a wide range of different powder application options to choose from. But generally, for the most part, there are two primary methods used across the industry: Electrostatic deposition (ESD) and fluidized bed powder coating.
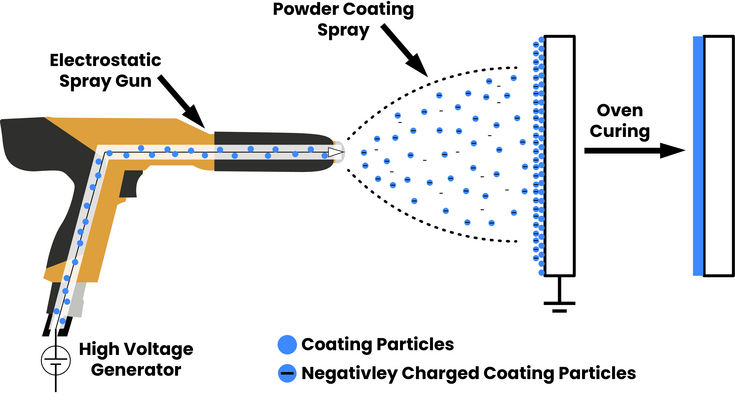
Electrostatic Deposition (ESD)
ESD is the more common of the two methods, particularly for coating metal parts. The powder is applied using a spray gun, creating an electrostatic charge that draws the particles to the grounded substrate. This attraction results in a uniform and efficient coating. It is essential to avoid the entry of dust and dirt at this step. The powder spray gun creates a charged cloud of powder. As a result, the paint particles adhere electrostatically to the piece and form a layer.
A typical manual setup of this application process involves the following components:
- Powder Spray Booth: This serves as the workspace for applying the powder material to a part. It also acts as an air filter and overspray containment and recovery system.
- Powder Feeder: This unit distributes the powder material to the spray gun.
- Electrostatic Spray Gun: The gun imparts an electrical charge onto the powder and applies it to the substrate. There are three common types of electrostatic guns: Corona, and Tribo.
- Corona Charging Guns: These are the most widely used and create a high-voltage, low-amperage electrostatic field between the electrode and the product being coated. Powder particles pass through the ionized electrostatic field, become negatively charged, and are deposited on the electrically grounded surface of the part.
- Tribo Charging Spray Guns: In this type of gun, powder particles gain their electrostatic charge through friction when they rub against a solid insulator or conductor inside the gun. This process results in positively charged powder particles eliminating the Faraday's cage effect - a common problem with Corona guns, making it perfect for coating complex shapes. It's versatile - working with epoxy, acrylic, nylon, Teflon, and polyester powders, ensuring smooth and precise application. Plus, it's ideal for re-coating defective parts.
- Recovery and Retrieval Systems: These collect overspray material for reuse in future coating applications.
Importance of Spray Systems During Powder Coating Application
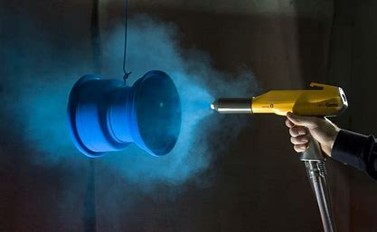
Spray systems are pivotal in the powder application process, offering efficient and precise coating application across various surfaces and part geometries. Spray systems in powder coating include components such as the powder hopper for holding the coating materials, an application gun for spraying, a feed system for transporting the powder from the hopper to the gun, a control unit that regulates and fine-tunes various application parameters, as well as air-supply and recovery systems. So, what makes a good powder coating spraying system? Let’s find out!
A notable characteristic of effective spray systems lies in their field-serviceable design and utilization of quick-turn components. This strategic approach simplifies maintenance procedures, leading to reduced downtime and ensuring a continuous, reliable performance throughout various coating tasks. When considering spray systems focus on adaptability as well and choose ones with versatile configurations, as they offer flexibility to cater to diverse coating requirements. An innovative pump design is another important consideration as it further enhances the functionality of the overall system by optimizing energy consumption, contributing to both efficiency and sustainability in coating processes.
Lastly, all-digital control units are becoming more common, providing precise control over electrostatic and pneumatic settings. This level of control is crucial in achieving optimal coating performance, ultimately leading to the production of high-quality finished products.
Fluidized Bed Powder Coating
In contrast, fluidized bed powder coating is somewhat different. Here's how it works:
- Preheating: Parts are preheated to ensure the powder adheres effectively. It must reach a temperature of at least 350°F, ideally ranging from 400 to 450°F. This elevated temperature is essential to keep the part hotter than the melting point of the powder. Typically, a conventional gas-fired convection oven is used to achieve this preheating.
- Dip-Coating: The next step involves dip-coating the preheated part. An air pump facilitates the flow of air through the powder coating fluidizer, creating a fluid-like suspension of powder particles. The hot part is then immersed in this fluidized bed of powder coating and moved around to ensure a continuous coating.
- Submerging: The part remains submerged in the fluid bed to allow the powder paint to create a thick, wear-resistant coating. The final thickness of the coating depends on the initial heat of the object before immersion and the duration it spends in the fluidized bed of powder coating.
- Post-Fusing: The last phase of fluidized bed powder coating is the post-fusing process. After any excess powder drips off the product, it is transferred to an oven set at a lower temperature for curing. Importantly, the post-heat temperature must be lower than that of the initial preheating oven. This step ensures that all the powder adheres to the part during the dip and melts into a smooth, uniform coating. Using too high a temperature in the oven could lead to undesirable outcomes such as the coating melting off, sagging, or dripping.
Automated Optimizations for Powder Coating Application
Employing oscillators, reciprocators, and robots to manage spray equipment offers cost savings and ensures consistent coverage in numerous applications. Gun triggering, which involves automatically turning the spray gun on and off based on part positioning, reduces overspray, leading to reduced material consumption.
Significance of Grounding & Best Practices When Applying Powder Coating
Grounding is arguably the most important aspect of a successful powder coating application. We’re saying “arguably” because this is a subjective statement and for some other factors may be more important whether that be the spraying system or the powder itself.
From a safety perspective, ungrounded parts can accumulate charge, posing a risk of electrical discharge when approached. This discharge can not only be startling but also hazardous. Discharges across small distances between charged surfaces and ground can contain enough energy to ignite the powder being sprayed from the gun, further emphasizing the safety aspect.
On a quality level, maintaining a solid ground is crucial for achieving consistent film thickness and uniformity in powder application. Issues such as Faraday cage penetration and back ionization can arise without proper grounding. A study conducted by Kolene Corporation highlighted that maintaining an excellent ground during the powder application process significantly improved powder-coated surface topography.
Lastly, from a cost perspective, poor grounding adversely affects transfer efficiency and minimum film thickness. Inefficient grounding can result in excessive powder usage to achieve the desired film thickness, leading to increased waste and expenses.
To ensure effective grounding, it is essential to have a traceable path from the part to the powder coating earth ground rod, with no breakdown in electrical conductivity. Using an 8 to 10-foot ground rod, preferably longer in high resistivity soil conditions, and measuring resistance between ground rods can help ensure a reliable ground. Employing solid copper ground bars of appropriate length further enhances the effectiveness of the grounding system. Overall, proper grounding is a critical factor in achieving both safety and efficiency in powder coating applications.
3. Curing
After application, the coated substrate is subjected to high temperature curing in an oven. During this process, the powder particles melt and fuse, forming a robust and durable finish. The powder coating is cured in an oven at temperatures between 110 and 250 °C. Various factors such as heating time and substrate thickness affect the final curing time. Thermoset powder coatings require specific heat energy and time to trigger the chemical reaction needed for cross-linking into a film. When exposed to heat, the powder material melts, forms a smooth film, and starts to cross-link, eventually reaching full cure. Different methods can be employed to provide the necessary energy for curing.
Different types of curing ovens & significance and limitations of each
Convection Ovens: Convection ovens use a heat source (typically natural gas) and a fan to circulate heated air through an oven's duct. The hot air transfers heat to the part and the coating. This is the most common type of oven for powder curing. As the part reaches the desired temperature, it conducts heat into the coating, leading to powder curing.
Infrared (IR) Ovens: IR ovens use gas or electricity as an energy source to emit radiation in the IR wavelength band. This radiation is absorbed by the powder and the substrate directly beneath the powder without significantly heating the entire part. This approach enables a quicker temperature rise, causing the powder to flow and cure when exposed for a sufficient duration. However, curing uniformity may be influenced by the part's shape and density.
Radiation Curing Technologies: These include near-infrared, ultraviolet (UV), and electron beam (EB) processes. These technologies offer potential applications for powder coating on heat-sensitive substrates like wood, plastic parts, and assembled components with delicate features.
- UV Curing: Special powders are used that can cure upon exposure to ultraviolet light. These powders are initially heated, typically through infrared or convection methods, to a molten state. UV lamps then provide the energy to solidify the coating in a matter of seconds.
- Near-Infrared Curing: This method involves specially formulated powders, high-energy light sources, and precise reflector systems to complete the powder coating and curing process in a matter of seconds. It's particularly useful for heat-sensitive assembled parts.
Tips for improving your powder coating line
Generally, powder coating operation lines are measured on their efficiency, scrap/defects, and waste generated. Ideally, you’d want a high-speed operation line with minimal rework, and material wastage. So, with that in mind, here are some tips to help you get there and make the most out of your powder coating process.
- Equipment Maintenance: Regularly maintain and clean all equipment, including spray guns, booth filters, and curing ovens. Proper maintenance ensures consistent performance and extends the life of your machinery.
- Powder Management: Optimize powder storage and handling to prevent contamination and waste. Invest in efficient powder delivery systems and storage containers.
- Pre-treatment Process: Ensure thorough cleaning and surface preparation before powder coating. Proper pretreatment enhances adhesion and prevents defects.
- Quality Control: Implement a robust quality control process, including inspection, testing, and monitoring. Detect and address issues early to prevent costly rework.
- Powder Selection: Choose the right powder coating material for your specific application. Consider factors like color, finish, effects, durability, and substrate compatibility.
- Optimize Curing: Fine-tune curing oven settings to achieve the desired finish and performance. Monitor temperature and time to ensure proper curing.
- Training and Certification: Ensure your team is well-trained and certified in powder coating techniques. Continuous education improves skill levels and consistency.
- Waste Management: Implement effective waste management practices for overspray recovery and recycling of excess/residual powder.
- Customization: Tailor your powder coating line to meet the specific needs of your products and customers. Not every business is the same, which is why a customized setup is going to be the best fit for you to improve efficiency and operational quality.
- Safety First: Prioritize the safety of your team by providing the necessary protective gear and training. A safe working environment contributes to overall productivity.
Some Of TIGERs Most Popular Powder Coating Finishes
TIGER SHIELD - Primers
With TIGER SHIELD, TIGER has developed a system that permanently protects steel and galvanized substrates against corrosion. In addition to use on steel and galvanized steel, selected TIGER Drylac® primers can also be used for aluminum substrates.
TIGER 3D Metallics
TIGER Drylac® 3D Metallics based on a super durable polyester combine the advantages of powder coating technology with the brilliance of wet paint metallic effects and transform ordinary objects into extraordinary custom pieces.
TIGER Superdurables
Our superdurable powder coatings are specially formulated and rigorously tested to last over periods of time well over 10 years. Their outstanding corrosion, UV and weather resistance makes them the ideal choice for outdoor applications like in architecture and the furniture industry!
Choose TIGER For Premium Powder Coating Colors & Finishes
As we conclude our journey through the fundamentals of the powder coating application process, it becomes evident that this innovative finishing method offers unparalleled durability and versatility. Whether in the automotive, architectural, appliance, or furniture industry, powder coating continues to revolutionize the way we beautify our world: one surface at a time. Embrace the power of TIGERs powder coating offerings from our Webshop and unlock a world of possibilities for your surface finishing projects.
Back to overview