Electrostatic Dissipative Coatings
Electrostatic charge is created wherever friction happens. Everybody knows the phenomenon, which happens for example when you pull off a plastic packaging from a product. A necessary consequence of electrostatic charge is its discharge which is shortly called “ESD”. It happens abruptly and creates voltage peaks of 100.000 V between two objects.
Why do we need conductive surfaces?
Conventional powder coatings are electrically insulating with a surface resistivity of more than 1 TΩ. Therefore, they cannot conduct away the voltage peaks and become a risk for electronic components or can act as a source of ignition for dust explosions. That's why coaters that deal with products such as electrical cabinets, electrical housings, wire harnesses and computers require specific powders.
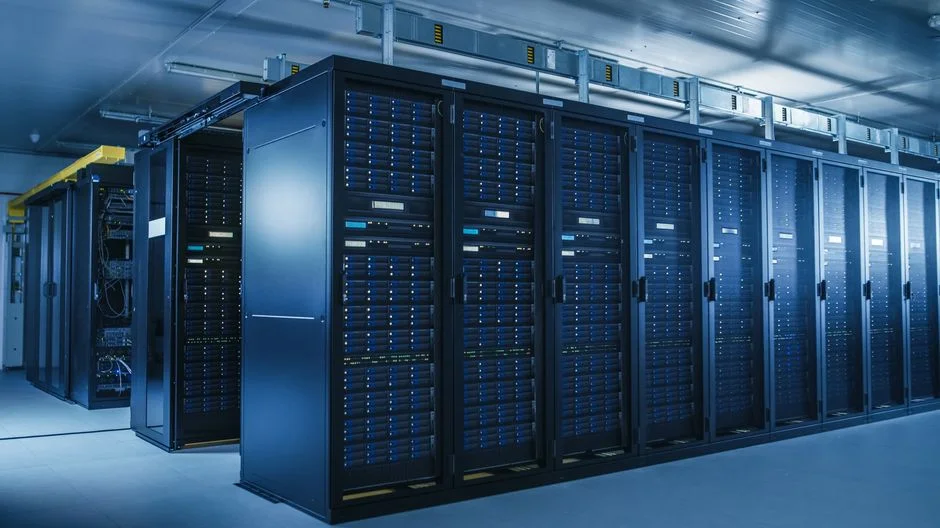
Classification of Conductivity
Materials are characterized according to their resistivity and can be assigned to different classes. They are divided into electrical insulators, materials showing antistatic behavior, electrostatic dissipative materials and conductors.
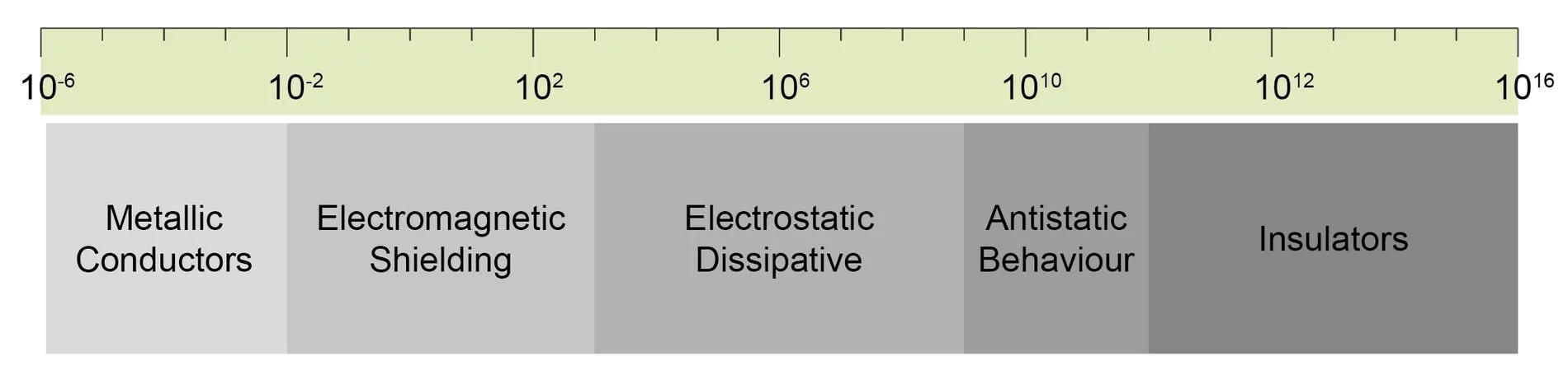
Electrical insulators
These materials exhibit resistance greater than 1011 ohms. Within them a charge is barely able to move. Rubber, porcelain, glass, diamonds and air as well as most powder coatings fall within this category. When it comes to powder coatings, they can be divided into the different resin systems which behave differently. Epoxides show higher resistivities than polyesters for example. When insulators experience extremely high voltages of several kilo or megavolts it can happen, that electrons are forced to move from their position. The result is a disruptive discharge (e.g. a lightning) where a lot of energy is transported in a short period of time.
Antistatic behavior
Antistatic behavior is shown between 109 - 1011 Ω and it is necessary for example in clean room environments.
Electrostatic dissipative
Materials showing a surface resistivity between 103 – 109 Ω are electrically conductive respectively electrostatic dissipative. This means materials are able to slowly discharge and that they can be used for electrical components in explosion-endangered areas. A material which is electrostatic dissipative is ALWAYS antistatic, but not vice versa.
Conductors
Conductors are materials in which charges can flow freely. The best-known are metals, acids, alkalis, salt solutions and graphite. Their surface resistivity is lower than 106 Ω.
How to make a powder coating conductive
Conductivity can be added through the addition of conductive additives. With a low concentration of the additive nothing will happen, but as one increases the dosage of the additive it is more likely that additive parts will be in touch with each other through the material and can form current paths. The conductivity increases in a small concentration range by the power of ten and more. This area is the so-called critical concentration. If we keep on adding additive, the conductivity will rise higher, but not as rapid as around the CC. After reaching a certain additive concentration, further addition does not improve the conductivity anymore. The graph is called a percolation curve and the CC is also called the percolation threshold.
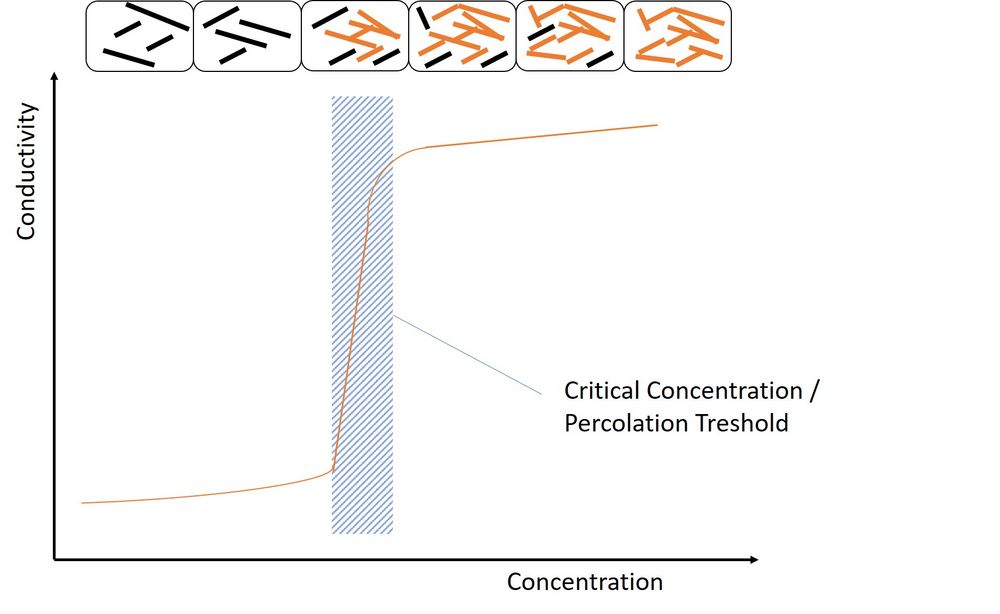
Graphite
Additives made from electrically conductive carbon have been used for a very long time. In earlier times graphite was used, while nowadays usually single-layered graphite crystals are used, which are called graphene. Powder coatings with a surface resistivity of 103 to 109 Ω are only possible in black or anthracite colors.
Carbon black
Carbon black is used in areas where only moderate conductivity is necessary. Carbon black results from incomplete burning of carbon-compounds in chemical reactions. But why is carbon black conductive? Carbon black is built from primary particles in which carbon atoms are arranged as in small graphite crystals.
Fibers
Carbon fibers are known for their mechanically reinforcing effect, but they are also electrically conductive. They color the component, but do not color their surroundings through touch or abrasion which is the case for carbon black or graphite filled components. Therefore, they are mostly used in clean room applications or for paper handling.
CNT’s
Carbon Nano Tubes are tiny tubes made from graphite with varying wall thickness. We distinguish between S (Single), D (Double) and M (Multi) walled nano tubes. Even at very low concentrations (0,04 weight percent) high conductivity values can be reached. Similar to other additives they influence the color of a coating, but with them brighter colors are possible.
Mica pigments
With these a surface resistivity of 109 to 1011 Ω is possible. Light greys as well as colors can be achieved.
TIGER – Your partner for ESD Powder Coatings
Thanks to its state-of-the-art R&D center, TIGER is able to develop ESD powder coatings that are precisely adapted to meet individual needs. Together with our customers, we develop custom formulations to meet any requirement.
Contact us today!
Back to overview