Powder coating wheels and rims: Advantages and Costs
An article by TIGER Coatings and Claudio from CV2 Design
Be it on a car or motorcycle: Wheels are the eye-catcher on every vehicle. However, in addition to their aesthetic appeal, these parts also must withstand a lot of stress: Rain, ice and weather, road salt, UV radiation, aggressive cleaners, stone chips, etc.
The challenge is to combine function with a stunning appearance. Powder coating can be a solution! Powder coated wheel rims offer properties such as corrosion protection, weather resistance, chemical resistance, and impact resistance - combined with amazing colors, effects, and finishes!
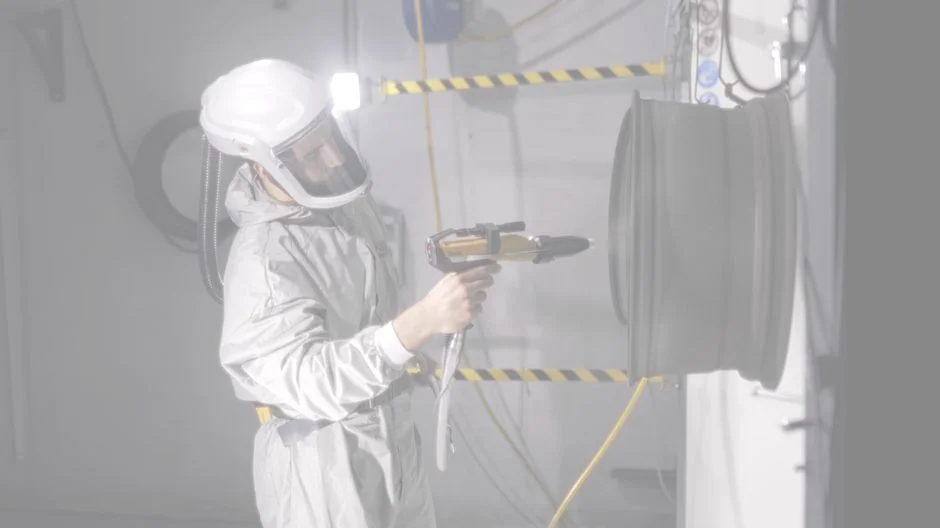
No coating without pre-treatment! - Preparing wheels for powder coating
Before even a grain of powder hits the rim, the following preparatory steps must be carried out:
Step 1: Stripping
If the powder coating is to replace an older layer of paint, the first step is to remove it completely. Two main methods are used for this:
Mechanical pretreatment
Here, the paint layer is removed using processes and techniques that rely on the application of mechanical force, for example sanding, brushing and/or blasting.
Chemical pretreatment
In this process, the paint is dissolved or removed from the workpiece by immersion in a chemical stripping agent, which can consist of acids, bases, and various solvents. The exact composition of the chemicals can vary depending on the application.
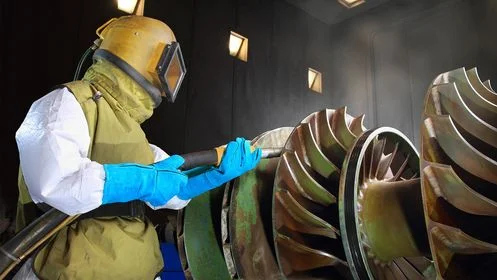
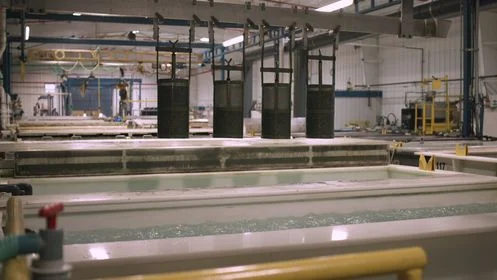
Attention with aluminum rims!
Unlike steel rims, which can be stripped of paint both mechanically and chemically, aluminum rims should only be treated chemically. The reason: alloy rims tend to bend when blasted under high pressure. This causes problems later on during balancing and, in the worst case, makes the wheel completely unusable.
Step 2: Repair (optional)
This step is not absolutely necessary. However, if a flawless set of rims is desired, it is advisable to repair any defects such as kerb damage, scratches or dents after the paint has been removed. ATTENTION: repairing deep damage or hairline cracks is an incalculable safety risk!
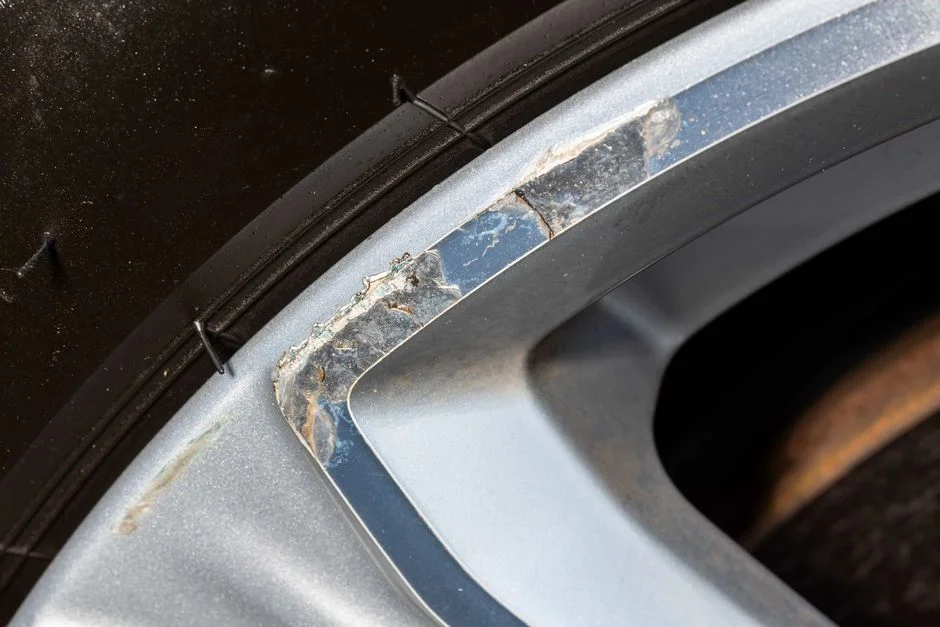
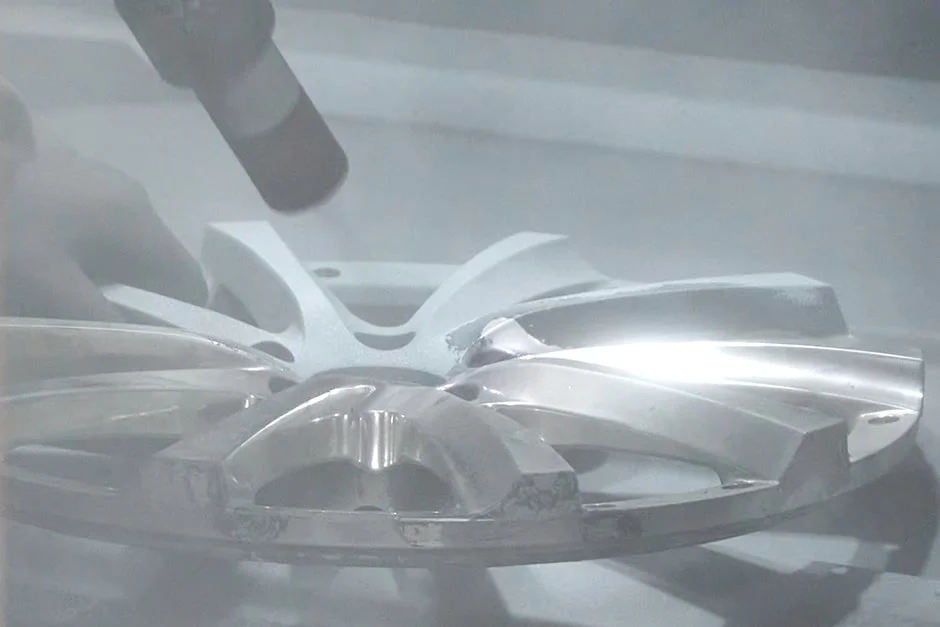
Step 3: Sandblasting
During so-called "sweeping", the workpiece is roughened under low pressure (2 to 3 bar) with a sharp-edged abrasive. This improves the adhesion of the powder to the surface. Any residue from chemical paint stripping is also removed in this step. To prevent contact corrosion, it is important to use a separate blasting booth for each substrate and to avoid the use of blasting granulates.
Step 4: Degreasing (optional)
Even if grease residues have already been largely removed by the previous steps, this final cleaning step can additionally be carried out after blasting. To do this, any separating agents are removed from the rims using cleaners such as isopropanol, silicone cleaner or acetone (be careful when using - flammability!). Due to the rough surface of the rims caused by blasting, cloths should not be used to wipe them (risk of fraying / lint formation); simply rinsing off the cleaner is sufficient.
Procedure for powder coating wheels
1. Masking: To begin with, all surfaces that are not to be coated, such as screw holes and the stop surface, are covered. The valve hole is left out and used for earthing/suspension.
2. Tempering: Chemical stripping has caused liquid components to penetrate the casting and sandblasting has also opened up casting pores in the substrate. In order to prevent outgassing and thus craters and/or pinholes in these cavities, the workpiece is heated in the oven before coating at a temperature at least 20°C above the later specified curing temperature of the powder coating (curing window product data sheet). The duration depends on individual conditions - in general, however, the curing time of the powder coating is recommended for tempering.
3. Primer and Basecoat: For optimum corrosion protection, a primer is applied to the rim before the effect-creating layer. This is followed by the second coat in the desired color and texture. In practice, the primer is not fully cured before the basecoat is applied, but merely "gelled" (50-70% of the curing time according to the curing window). This increases adhesion with the next coat. It also saves process time and energy.
4. Clear Coat (optional): As the effect-giving pigments in powder coating are oriented to the surface, abrasion or the use of aggressive rim cleaners can lead to changes in the original appearance. We therefore recommend applying an additional layer of clear coat (3-layer system). Thanks to their good chemical resistance, acrylic or polyurethane-based clear coats are particularly suitable for a high-quality, road-washable, and winter-proof coating.
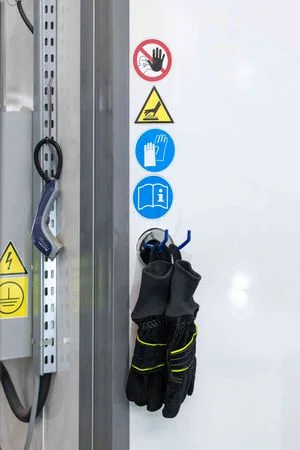
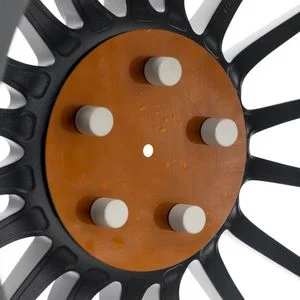
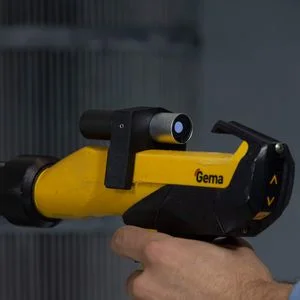
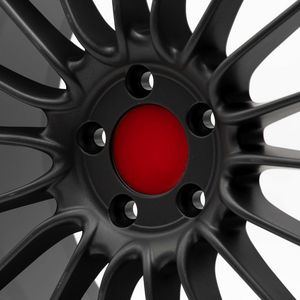
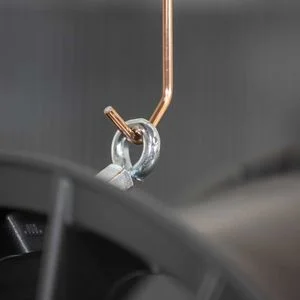
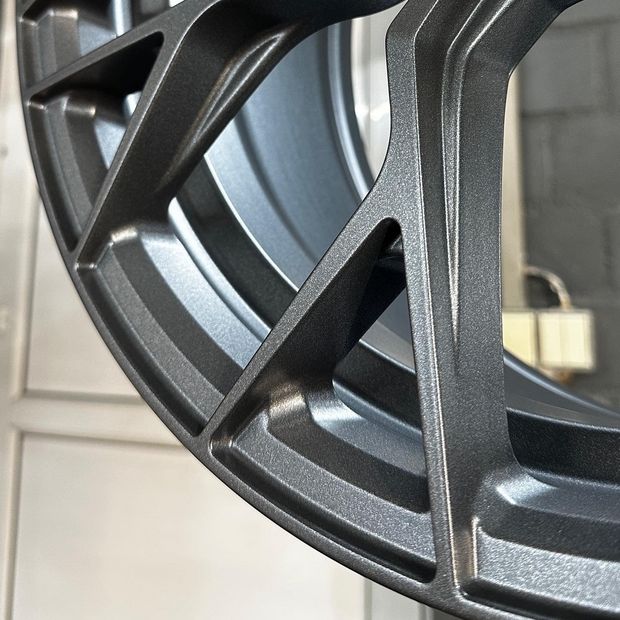
Advantages of powder-coated rims
Powder coating offers numerous advantages in general and in comparison, to wet painting:
- Outstanding corrosion protection
- Very good weather and UV resistance
- Resistance to mechanical stress (stone chips, scratches, etc.)
- Easy to clean
- Free from solvents
Are there any disadvantages?
- Repairability: Reworking and corrections to an already hardened powder coating are difficult to carry out. Defects often require the entire workpiece to be repainted.
- Blendability: Powder coatings cannot be matched as easily as liquid coatings and therefore cannot be easily adapted to other colors.
Tip: If you have components made of different materials (e.g. plastic and metal) where one is to be powder-coated and the other wet-painted, start with the powder coating. This allows the coater to create a sample sheet for the painter, who can then mix the color accordingly.
- Effect choice: Very smooth surfaces and intensive effects (e.g. metallics) are easier to achieve with wet paint. In terms of the richness of effects, however, powder coating has developed steadily and enables a variety of spectacular finishes such as metallics, flip-flop, dormant or pearlescent.
Revitalizing Wheels with TIGER Powder Coatings: A Success Story with Alloy Wheel Repair
At TIGER Drylac, we take pride in providing high-quality powder coatings for a wide range of applications, including automotive wheel repair and refinishing. One of our most successful collaborations has been with Alloy Wheel Repair Specialists, LLC, a premier provider of wheel repair services across North America.
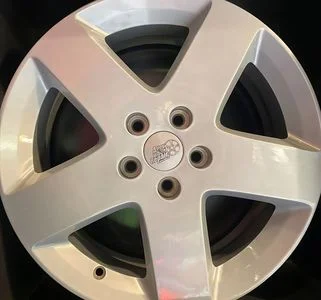
A Trusted Name in Wheel Repair
Founded in Atlanta, Georgia in 2001, Alloy Wheel Repair Specialists has grown from a single location to a vast network of over 120 locations nationwide. Their mission is to be the global leader in shop-based and mobile wheel repair, wheel remanufacturing, and custom wheel coloring. In addition to their expert repair services, they also supply OEM replacement wheels, ensuring customers receive high-quality solutions tailored to their needs.
Why Alloy Wheel Repair Trusts TIGERs Powder Coatings
The leadership team at Alloy Wheel Repair is committed to exceptional service and premium-quality finishes. To maintain their high standards, they meticulously source the best products, conducting thorough quality and performance tests across their nationwide locations. As part of their standard operating procedures, TIGER Drylac’s “Wet Black” and “Bengal Silver” have become go-to powder coatings for wheel refinishing.
TIGER “Wet Black”
- An automotive-approved, single-stage powder
- Provides an exceptionally smooth, high-gloss finish
- Outshines other gloss black powders on the market
TIGER “Bengal Silver"
- A perfect match for Sparkle Silver, a popular OEM finish
- When paired with a clear coat, it enhances shine and delivers a sleek, OEM-quality appearance
Thanks to consistent results, superior durability, and fast lead times of our powder coatings, we have become a preferred vendor for Alloy Wheel Repair’s coating and color-matching needs.
Powder Coating in OEM Wheel Manufacturing
Beyond wheel repair, our coatings are also used by manufacturers who supply OEM wheels. These manufacturers often apply a three-layer coating system for added protection and aesthetics:
- Powder Primer
- TIGER 200/80012 Wheel Black or 200/70022 Wheel Gray Powder
- Liquid Base Coat
- Note: TIGER Drylac specializes in powder coatings and does not supply liquid paints.
- Acrylic Clear Coat
- TIGER 250/00108 Acrylic Clear (if using powder clear coat)
- Alternatively, a liquid acrylic clear coat may be used from another supplier.
Elevating Wheel Coating Standards
Whether for repair specialists or OEM manufacturers, TIGER Drylac continues to provide industry-leading powder coatings that enhance both performance and appearance. With our commitment to quality, innovation, and customer satisfaction, we help businesses achieve a flawless, durable finish that meets the highest standards.
For more information on our powder coatings for wheels, contact us today or explore our extensive range of automotive-approved finishes!
What do powder-coated rims cost?
The cost of a rim coating depends on its condition and size, the desired structure, and the selected surface, but also on the cost of machines and materials plus working and dwell time.
The price for a powder coating in standard colors including basic pre-treatment and a 3-layer structure is between $ 98 and $ 130 per rim. Depending on the quality of the service, the amount can also be lower or significantly higher in individual cases (incl. polishing, bicolor effect, etc...).
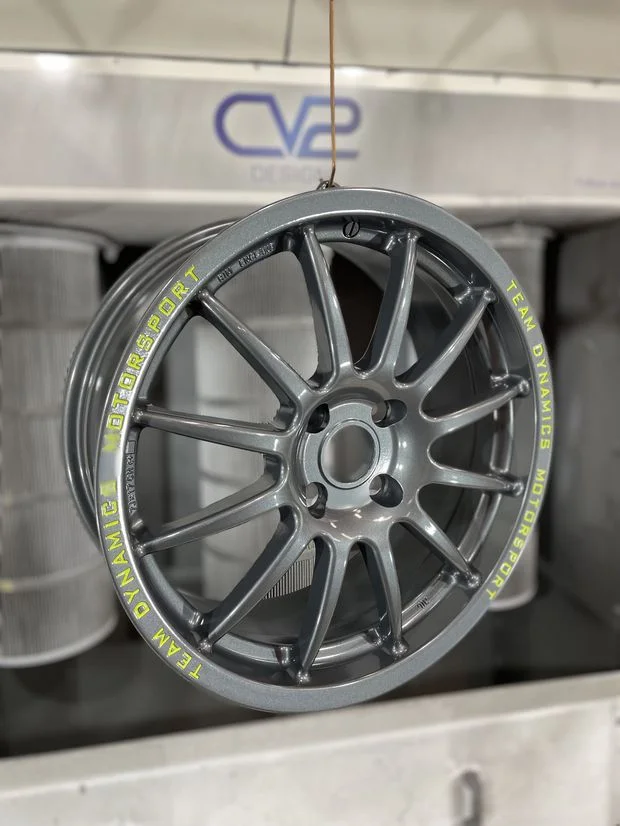
FAQ
Rims made of aluminum and steel can be coated with powder without any problems. With special materials such as magnesium alloys, however, undesirable interactions can occur, which is why the suitability for coating must be checked carefully in advance.
A clear no - unless it is a pure show car! If cracks have been welded in a rim, it may no longer be used on the road!
Chrome-plated rims can also be powder-coated if the coating adheres to the surface. In this case, it may be advisable to roughen the chrome layer beforehand by sanding.
In general, yes! However, the coater must have extensive expertise in masking with heat-resistant cover materials. A good basis for bicolor coating with powder coating is provided by polished rims, for example.
This depends, among other things, on whether the job shop carries out all the steps itself or, for example, outsources stripping to external professionals. Due to the numerous work steps and necessary dwell times, the processing time can be around 10 to 15 working days if a coater is working to capacity.
Back to overview