How to Properly Powder Coat Geometric Parts
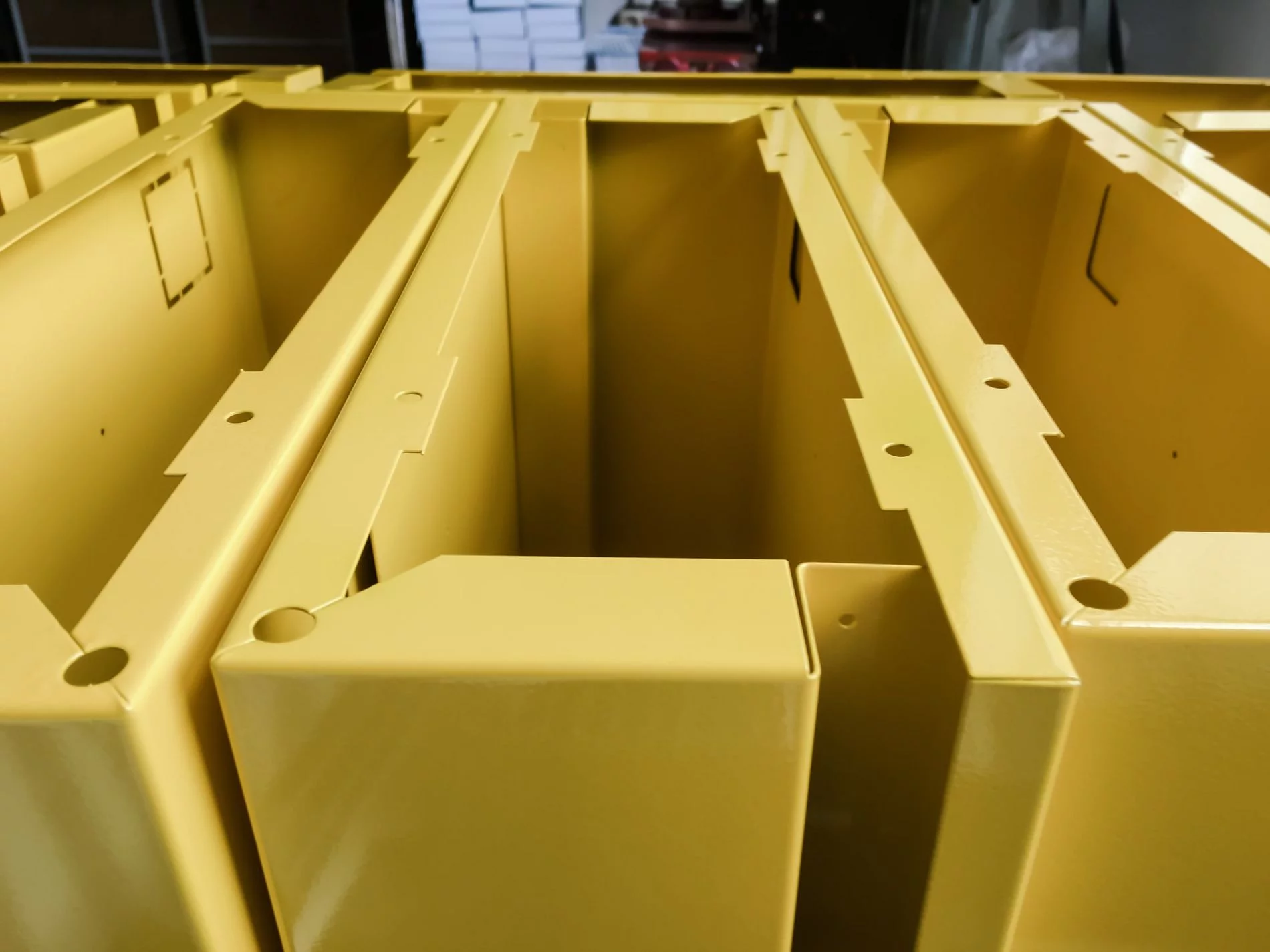
Powder coating complex parts can be frustrating. Here are a few guidelines to help get the job done correctly, the first time, and every time! Products shaped in abstract ways can inhibit the electrostatic application of the powder from reaching in a particular area such as curves, recesses, and faradays. It is one of the most common challenges a powder coaters faces.
- Ensure parts are grounded properly with a solid ground.
- Gun tip to the part is very important to have solid wrapping - 8-12 inches.
- Powder Flow is vital! If there is not enough powder flowing from the gun itself, getting powder into those intricate areas is going to be tough. Appropriate air dispersion of powder, is a gentle and lingering cloud. If adjustments are needed modify the flow and increase the amount of powder exiting the gun.
- Adjusting the amperage and voltage:
- Keep your powder machine voltage set to normal ranges. This allows the powder to be fully charged, and fully attracted to your target.
- Reduce the amperage. Reducing the amperage to 20 micro amps or less will focus the charging within the center of the powder cloud.
- Coat the corners and crevices of geometrical parts first, leaving the simple to coat surfaces for later passes.
- Return the amperage to normal settings following powder application into challenging areas.
- Apply powder coatings to the entire surface of the part that you are powder coating in smooth, machine-like, and even passes. Be sure to include passing over previously coated areas. The powder coating that has been applied will provide insulation, helping to control excessive film build.
- “Quick Tip” Sometimes, preheating the part can allow the powder to adhere quicker to the substrate. Doing this increases the overall film build and how well powder grips to the internal corners. This is not ideal, because heat attracts powder like a magnet and you could end up with a coating that is too thick.
Poor Penetration Into Recesses
Like previously mention a common challenge when powder coating geometric parts is achieving a minimum coating thickness in the corners. With poor penetration procedures, penetration depth is very limited. Extreme film thickness variations are noticeable.
Possible causes | Corrections, testing, procedures |
Feed supplemental or tribo air too high | Change of lower pressure |
Air speed too high | Adjust equipment controls |
Powder flow too high | Adjust equipment controls to suit part |
Not enough powder flow | Adjust/optimize equipment parameters |
Inappropriate application, unsuitable nozzle | Utilize flat spray nozzle or deflector; Adjust nozzle |
Insufficient charging of powder, defective gun | Adjust voltage (increase, test) Contact equipment manufacturer |
Voltage too high | Adjust/reduce voltage |
Faraday cage effect due to electric field | Use tribo equipment and powder; Reduce voltage |
Insufficient grounding | Use clean hooks, test transfer resistance |
Powder spray too wide | Use different gun nozzle of deflector |
Unsuitable particle size distribution | Optimize through testing; Contact powder manufacturer |
Distance from gun to part is too big or too small | Increase or decrease distance |
To discover more causes and corrective solutions regarding powder coating application visit out Technical Information Sheets:
Back to overview